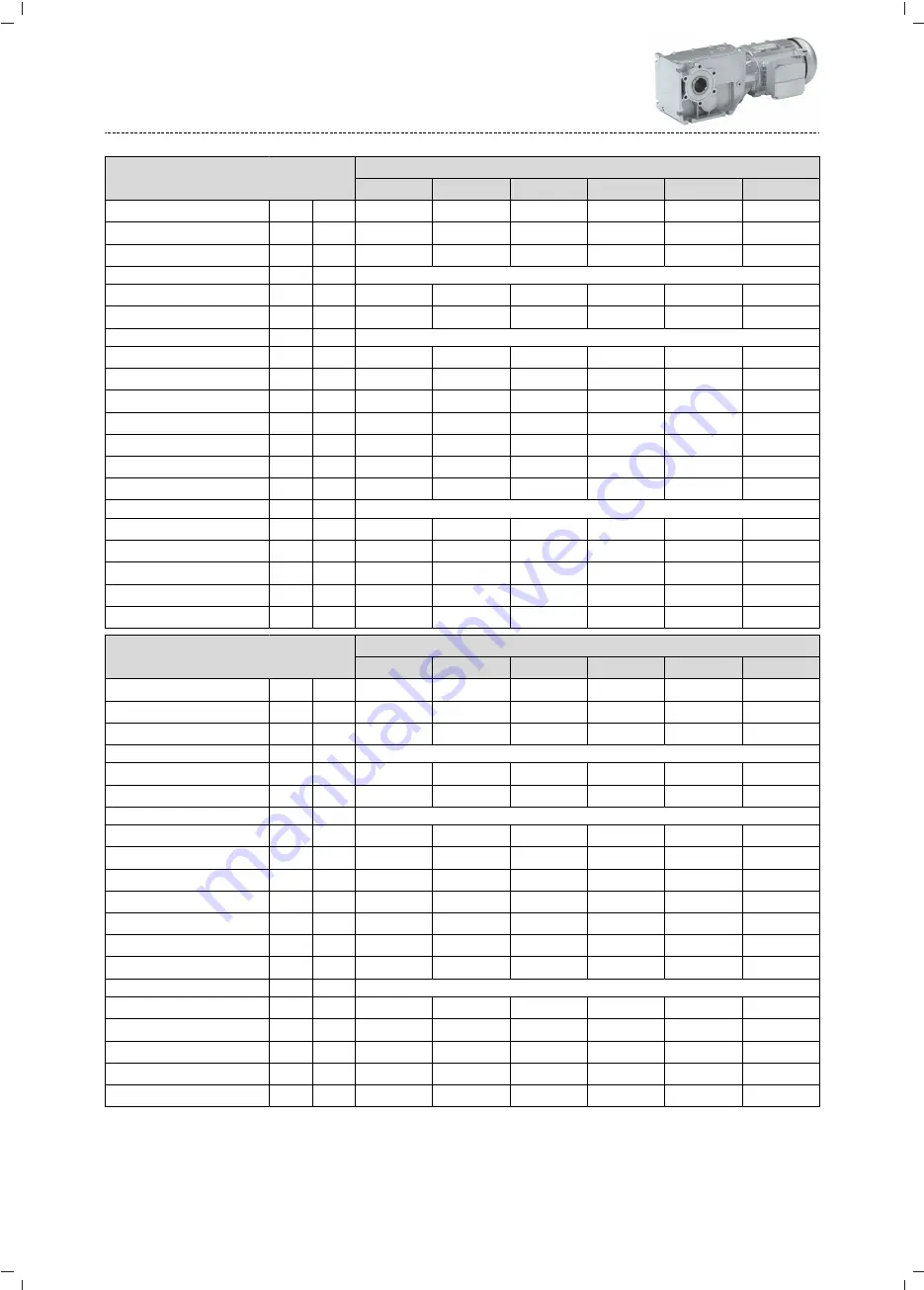
Motor
M55BP
080M04
090M04
090L04
100M04
100L04
112M04
Rated power
P
rated
kW
0.75
1.1
1.5
2.2
3
4
Rated speed
n
rated
rpm
1455
1465
1465
1470
1470
1470
Max. speed
n
max.
rpm
4500
4500
4500
4500
4500
4500
Rated voltage
Dreieck
V
rated, Δ
V
230
230
230
230
230
230
Stern
V
rated, Y
V
400
400
400
400
400
400
Rated current
230 V
I
rated, Δ
A
2.77
4.00
5.51
7.72
10.6
13.5
400 V
I
rated, Y
A
1.60
2.31
3.18
4.46
6.10
7.82
Starting current
I
a
A
8.91
16.4
22.5
35.8
47.1
58.3
Rated torque
M
rated
Nm
4.92
7.17
9.78
14.3
19.5
26.0
Starting torque
M
a
Nm
7.38
14.4
20.6
31.3
43.1
44.1
Stalling torque
M
b
Nm
16.2
25.2
34.3
49.8
66.6
83.1
Power factor
cos ϕ
0.84
0.83
0.82
0.83
0.84
0.86
Efficiency
at 50% P
rated
η
0.826
0.844
0.851
0.879
0.883
0.898
at 75% P
rated
η
0.825
0.841
0.853
0.867
0.877
0.886
at 100% P
rated
η
0.825
0.841
0.853
0.867
0.877
0.886
Moment of inertia
J
kgcm²
27.2
53.8
58.3
123
130.3
198
Weight
m
kg
12.28
17.33
18.43
30.41
31.61
40.38
Motor
M55BP
132M04
132L04
160M04
160L04
180M04
180L04
Rated power
P
rated
kW
5.5
7.5
11
15
18.5
22
Rated speed
n
rated
rpm
1480
1480
1485
1485
1485
1480
Max. speed
n
max.
rpm
4500
4500
4500
4500
4500
4500
Rated voltage
Dreieck
V
rated, Δ
V
230
230
230
230
230
230
Stern
V
rated, Y
V
400
400
400
400
400
400
Rated current
230 V
I
rated, Δ
A
18.3
25.4
36.0
49.2
57.6
67.2
400 V
I
rated, Y
A
10.6
14.6
20.8
28.4
33.3
38.8
Starting current
I
a
A
84.9
117
163
228
315
312
Rated torque
M
rated
Nm
35.5
48.4
70.7
96.5
119
142
Starting torque
M
a
Nm
53.3
77.6
98.9
144
251
241
Stalling torque
M
b
Nm
131
179
226
308
465
467
Power factor
cos ϕ
0.86
0.85
0.86
0.849
0.893
0.906
Efficiency
at 50% P
rated
η
0.903
0.908
0.920
0.928
0.932
0.937
at 75% P
rated
η
0.896
0.904
0.914
0.921
0.926
0.930
at 100% P
rated
η
0.896
0.904
0.914
0.921
0.926
0.930
Moment of inertia
J
kgcm²
470.6
485.9
1360
1550
2330
2400
Weight
m
kg
61.82
64.26
168.4
183.2
168.4
183.2
Technical data
Motor data
Rated data
68