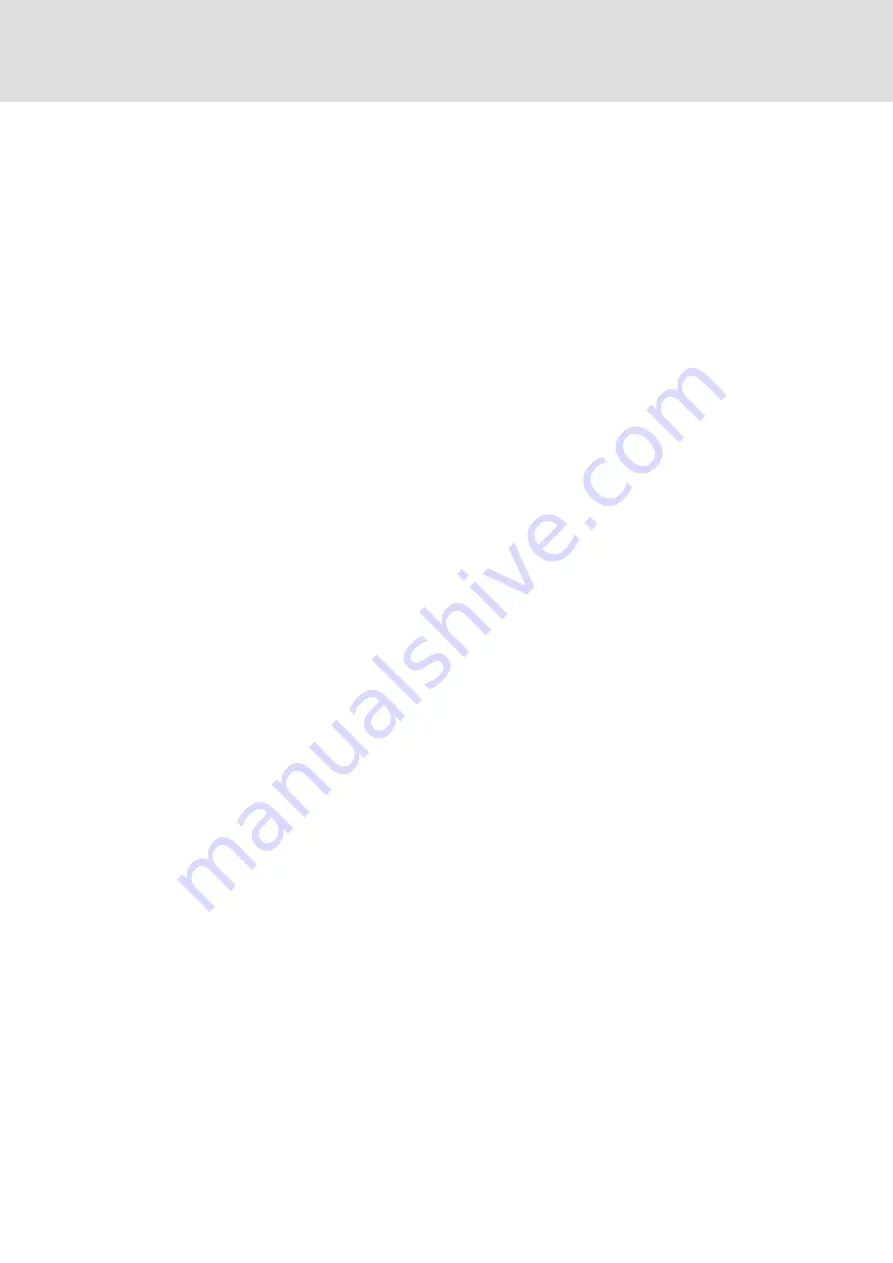
DC−bus operation
Introduction
Terminology and abbreviations used
7
l
110
EDS700ACBA EN 5.1
7
DC−bus operation
7.1
Introduction
7.1.1
Terminology and abbreviations used
Explanations of special terms concerning DC−bus operation can be found in the chapter
"About this documentation" under "Terminology and abbreviations used" (
¶
7.1.2
Advantages of a drive system
When several controllers are operated in a DC−bus connection (DC bus), this offers the
following advantages:
ƒ
Energy exchange between controllers in generator−mode (braking) and motor−mode
operation.
ƒ
The energy exchange reduces the supply power from the AC mains.
ƒ
DC−supply modules or feeding single−axis controllers can be dimensioned with a
lower rated power.
ƒ
The energy exchange reduces the braking losses in generator−mode operation.
Advantages for installation:
ƒ
Only one AC−mains connection (e.g. at the DC−supply module).
ƒ
Reduced wiring costs.
Summary of Contents for E70AC Series
Page 1: ...EDS700ACBA Usx Usx Hardware Manual i700 l E70AC Servo Inverter i700 Translation...
Page 2: ...0Fig 0Tab 0...
Page 75: ...Mechanical installation 5 l 75 EDS700ACBA EN 5 1...
Page 147: ...Accessories overview Terminals 11 l 147 EDS700ACBA EN 5 1 E70AZEVK001 i700ZM001 A...
Page 148: ...Accessories overview Terminals 11 l 148 EDS700ACBA EN 5 1 E70AZEVK002 i700ZM001 C...
Page 149: ...Accessories overview Terminals 11 l 149 EDS700ACBA EN 5 1 E70AZEVK003 i700ZM001 B...
Page 150: ...Accessories overview Terminals 11 l 150 EDS700ACBA EN 5 1 E70AZEVK004 i700ZM001 D...
Page 151: ...Accessories overview Terminals 11 l 151 EDS700ACBA EN 5 1 E70AZEVK005 i700ZP005 a...
Page 152: ...Accessories overview Terminals 11 l 152 EDS700ACBA EN 5 1 E70AZEVK006 i700ZP005 b...
Page 161: ......