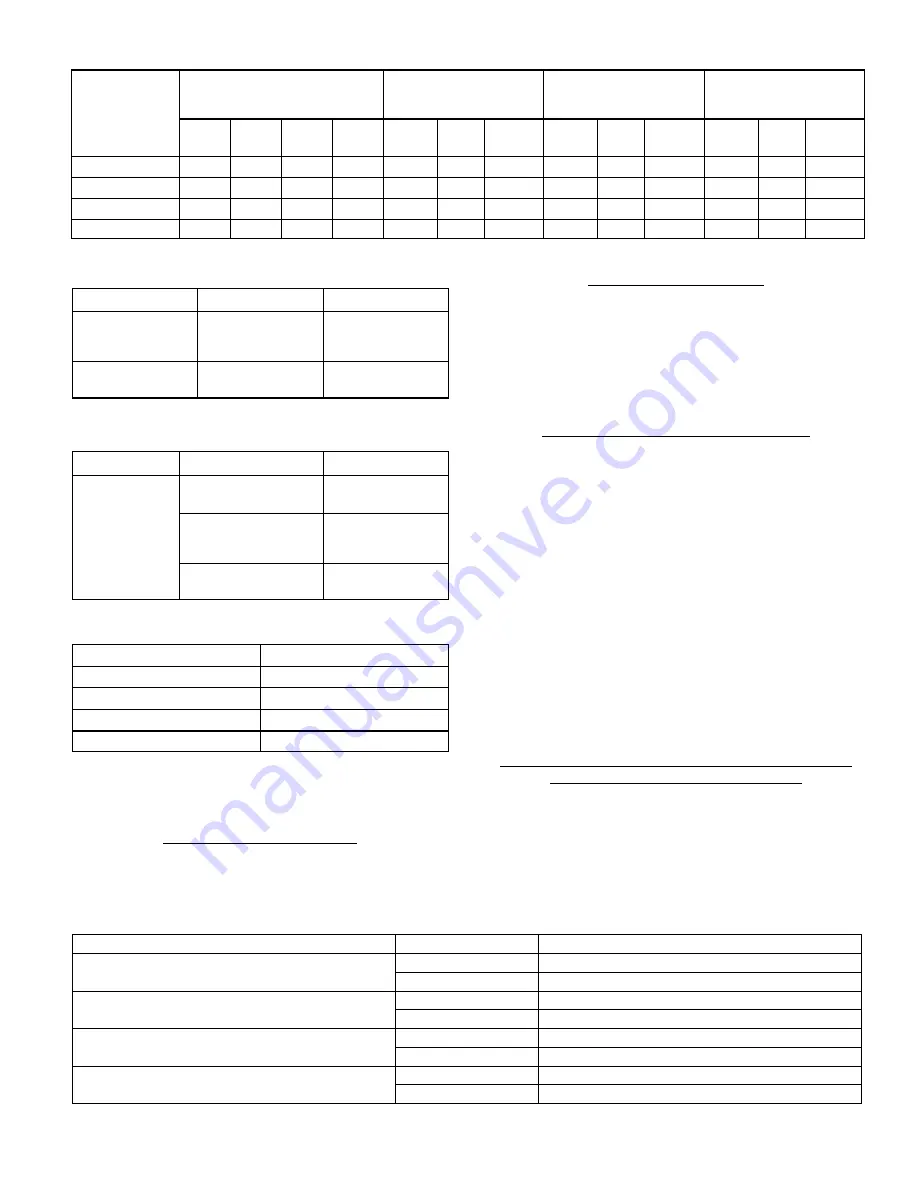
Page 49
XP21 SERIES
Table 15. Fan Motor Control RPM, LED Code and DC Voltage Output
Application
CFM Profile Pin Select
Low Stage ECM1/Y1
Only
High Stage ECM1/Y1
and ECM2/Y2
EDA Operation
ECM2/Y2 Only
4
3
2
1
RPM
LED
Code
DC Volt
RPM
LED
Code
DC Volt
RPM
LED
Code
DC Volt
XP21−024
ON
ON
OFF
ON
425
6
13.6
500
7
16.0
200
3
6.3
XP21−036
ON
OFF
ON
ON
525
7
16.8
600
8
19.2
225
3
7.0
XP21−048
ON
OFF
OFF
ON
600
8
19.2
675
9
21.6
225
3
7.0
XP21−060
ON
OFF
OFF
OFF
625
8
20.0
700
10
22.5
225
3
7.0
* LED Code indicates Fan Motor Control LED flash sequence. For example, LED Code 9 indicates 9 slow flashes and pause.
Table 16. Fan Motor Control Error/Fault LED Codes
Unit Status
Motor Control LED
Possible Cause
Mismatched RPM
Fast flash with no
pause
Internal feedback,
PWM does not
match target
CRC Failure
Constant ON.
Microcontroller CRC
failure
Table 17. Fan Motor Control Stage LED Indicator
Codes
Unit Status
Unit Status
Motor Control LED
Two Stage
Operation
Low Stage
ECM1/Y1 ONLY
One slow flash, then
short pause
High Stage
ECM1/Y1 and
ECM2/Y2
Two slow flash, then
short pause
EDA Operation
ECM2/Y2 ONLY
Three slow flash,
then short pause
Table 18. Fan Motor Control Flash and Pause
Durations
Flash or Pause State
Duration
Flash Flash
Three flashes per second
Slow Flash
One flash per second
Short Pause
Two seconds of OFF time
Long Pause
Five seconds of OFF time
Testing
Use the following information to verify and test the fan
motor control (A177).
Verify Jumper Settings (J2)
The unit is shipped from the factory with the default fan
motor speed setting (in RPMs) required for each model.
Use table 15 to verify that jumpers are set correctly for the
unit being installed.
Verify LED Status Codes
During start up, the fan motor control LED will display
any error conditions. If error conditions exist then no
other codes will display. If no error conditions are
present, then the stage status and and RPM indicator
are displayed in sequence.
Two−stage units have
various fan motor speed operations available (see table
15).
Verify Correct DC Output Voltage (J2)
The following three methods can be used to determine
whether the fan motor (B4) is operating at the correct
RPMs based on unit size.
1. Use the information provided in table 15 to verify that all
four jumper terminals are set correctly for the specific
unit.
2. Verify that the fan motor speed / RPM indicator is
displaying the correct flash sequence for the specific unit
(see table table 15).
3. Test DC voltage output on the fan motor control’s J2
terminals (see figure 35) while under full load. The actual
voltage tested should match the voltage listed in table 15
for the specific unit.
4. If no voltage is detected at the
J2
terminals, verify there
is a Y1 demand at the thermostat.
If there is a demand, proceed to the next section for further
testing.
Verify Correct Input Voltage (ECM/Y1, ECM/Y2,
ECM C AND EXT ECM/R) Terminals
Use a voltmeter to check voltages on the following fan
motor control inputs, using table 19. Voltage will only be
present during a thermostat demand. See figure 36 for test
example.
If correct voltages are detected at the applicable inputs
during a demand, and no voltage is present at the J2
terminals, then the fan motor control should be replaced.
Table 19. Fan Motor Control Voltage Inputs
Input
Thermostat Demand
Voltage Present
ECM/Y1 and ECM C (Low Stage)
YES
Between 24VDC and 32 VDC
NO
NONE
ECM/Y1 − ECM/Y2 and ECM C (High Stage)
YES
Between 24VDC and 32 VDC at each input
NO
NONE at each input
ECM/Y2 and ECM C (EDA Operation)
YES
Between 24VDC and 32 VDC
NO
NONE
EXT ECM/R and ECM C
YES
24VAC
NO
NONE