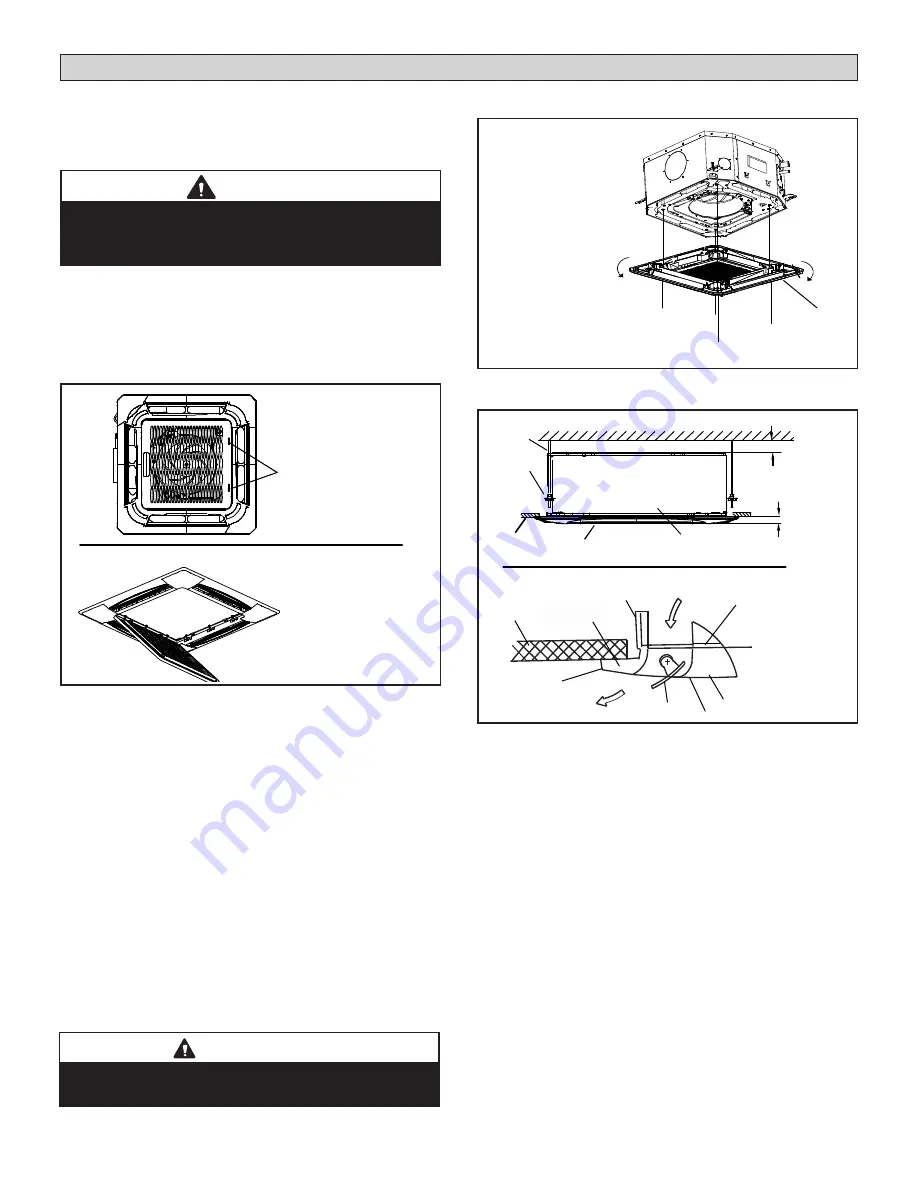
18
Cassette Cover Panel Installation
1. Carefully remove the cassette cover panel from its
protective packaging and place the panel diffuser-
side-out on a clean, level surface.
Cover Panel
Swing motor installation cover
2
3
Cover
Steel rope
1
3
Drain side
Make note of the arrows to
ensure proper installation of
cover. If impropery installed,
cover cannot be easily
removed in the future.
Latch Release Tabs
45º
Slide tabs toward each
other to release latch.
Tilt return air grille outward,
then, lift to remove grille
from panel.
≥7/8 (22 mm)
1-7/8 (48 mm)
⅜”
Threaded
Rod
Cassette
Unit
Base
Cover
Panel
Ceiling
Leveling
Nut
air ou
t
Cassette Bas
e
Ceiling
Foam
Insulation
Cover
Panel
Suppl
y Ai
r
Louver
Foam
Insulation
Side View Cutaway
Panel
Foam
Insulation
Figure 23. Remove Return Air Grille
CAUTION
Do not place the cover panel with the diffusers face down
on the floor or other surface. Louvers will be damaged if
pressure is applied to them.
2. Slide the two grille latches toward each other at the
same time to release the grille. See Figure 24. Tilt the
return air grille outward at a 45º angle (grille is held
in place by tethers). Release the tethers and lift the
grille away from the panel. Carefully place the return
air grille off to the side.
3. Position the ceiling panel so that the arrow on the
panel is aligned with the arrow sticker on the cassette
base (both arrow stickers should be on the same
side of the cassette base).
NOTE - If the panel and
the base are not properly aligned, the airflow will be
blocked and the harness plugs from the panel to the
cassette base will not be long enough to plug together.
See Figure 24.
4. Connect the six-pin harness plugs from each of the
two swing motors to the matching six-pin plugs from
the control box in the cassette base.
5. Connect the black harness from the display on the
cover panel to the corresponding black plug from the
control box in the cassette base.
6.
Connect the return air sensor (behind the filter) on the
cover panel to the corresponding white plug from the
control box in the cassette base.
7. Adjust the cover panel by turning slightly clockwise,
if necessary, to make sure that the panel is properly
aligned with the cassette base.
8. Use the provided screws to secure the cover panel
to the unit base. Continue to tighten the cover panel
securing screws until the insulation between the cover
panel and the cassette base has been compressed to
approximately ¼” (6 mm). The cover panel must form
a seal with the ceiling and the cassette base around
the entire perimeter of the unit. See Figure 25.
9. If it is necessary to adjust the cassette height after the
cover panel has been installed, access the leveling
nut through the return air grille opening.
10. The return air grille is tethered to the cover panel and
must be reinstalled. Align the four tabs on the grille
with the four slots in the cover panel. Tilt the panel
back into place. Press the opposite side of the cover
gently until the latches engage.
Figure 24. Install Panel Cover
Figure 25. Cover Panel In Place
NOTE - Cover panel must be ordered as a separate accessory.
IMPORTANT
Connect the return air sensor on the cover panel to the
white plug in the control box.
.