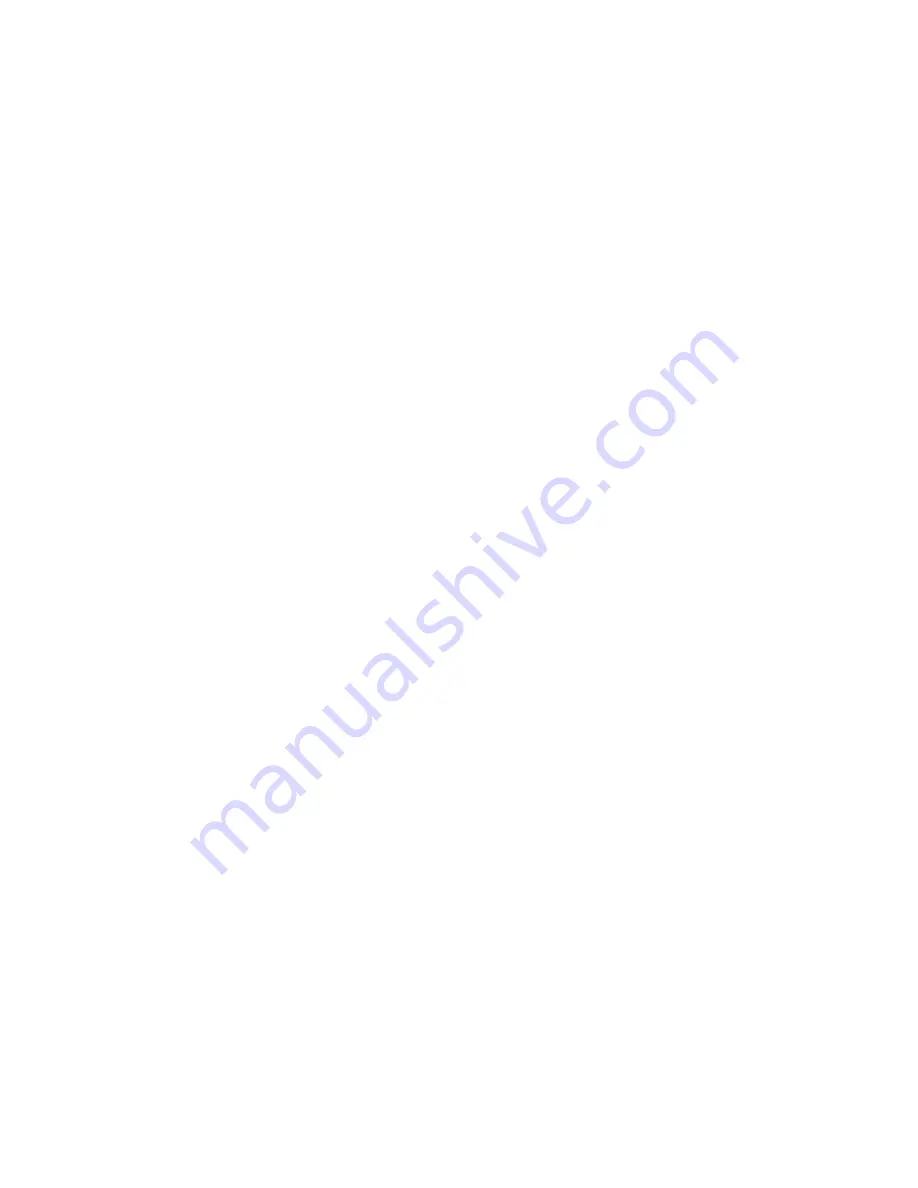
Page 32
506650−01
Defrost Temperature Termination Shunt (Jumper)
Pins (P1)
The demand defrost control selections are: 50, 70, 90, and
100°F (10, 21, 32 and 38°C). The shunt termination pin is
factory set at 50°F (10°C). If temperature shunt is not
installed, default termination temperature is 90°F (32°C).
Compressor Delay Mode (P5)
The demand defrost control has a field−selectable function
to reduce occasional sounds that may occur while the unit
is cycling in and out of the defrost mode. When a jumper is
installed on the DELAY pins, the compressor will be cycled
off for 30 seconds going in and out of the defrost mode.
Units are shipped with jumper installed on DELAY pins.
NOTE − The 30 second off cycle is NOT functional when
jumpering the TEST pins.
OPERATIONAL DESCRIPTION
The demand defrost control has three basic operational
modes: calibration, normal and defrost.
1.
Calibration Mode
The demand defrost control is
considered uncalibrated when power is applied to the
demand defrost control, after cool mode operation, or
if the coil temperature exceeds the termination
temperature when it is in heat mode (see figure 23 for
further details).
2.
Normal Mode
The demand defrost control
monitors the
O
line, to determine the system operating
mode (heat/cool), outdoor ambient temperature, coil
temperature (outdoor coil) and compressor run time to
determine when a defrost cycle is required.
Calibration of the demand defrost control occurs after
a defrost cycle to ensure that there is no ice on the coil.
During calibration, the temperature of both the coil and
the ambient sensor are measured to establish the
temperature differential which is required to allow a
defrost cycle.
3.
Defrost Mode
The following paragraphs provide a
detailed description of the defrost system operation.
TEST MODE
Each test pin shorting will result in one test event.
For
each TEST the shunt (jumper) must be removed for at
least one second and reapplied. Refer to flow chart (figure
24) for TEST operation.
Note: The Y1 input must be active (ON) and the O room
thermostat terminal into demand defrost control must be
inactive.
DETAILED DEFROST SYSTEM OPERATION
The demand defrost control initiates a defrost cycle based
on either frost detection or time.
1.
Frost Detection
If the compressor runs longer than
30 minutes and the actual difference between the clear
coil and frosted coil temperatures exceeds the
maximum difference allowed by the demand defrost
control, a defrost cycle will be initiated.
2.
Time
If six hours of heating mode compressor run
time has elapsed since the last defrost cycle while the
coil temperature remains below 35°F (2°C), the
demand defrost control will initiate a defrost cycle.
3.
Actuation
When the reversing valve is
de−energized, the Y1 circuit is energized, and the coil
temperature is below 35°F (2°C), the demand defrost
control logs the compressor run time. If the demand
defrost control is not calibrated, a defrost cycle will be
initiated after 30 minutes of heating mode compressor
run time. The control will attempt to self−calibrate after
this (and all other) defrost cycle(s).
Calibration success depends on stable system
temperatures during the 20−minute calibration period.
If the demand defrost control fails to calibrate, another
defrost cycle will be initiated after 45 minutes of
heating mode compressor run time. Once the demand
defrost control is calibrated, it initiates a demand
defrost cycle when the difference between the clear
coil and frosted coil temperatures exceeds the
maximum difference allowed by the control or after six
hours of heating mode compressor run time has been
logged since the last defrost cycle.
4.
Termination
The defrost cycle ends when the coil
temperature exceeds the termination temperature or
after 14 minutes of defrost operation. If the defrost is
terminated by the 14−minute timer, another defrost
cycle will be initiated after 30 minutes of run time.