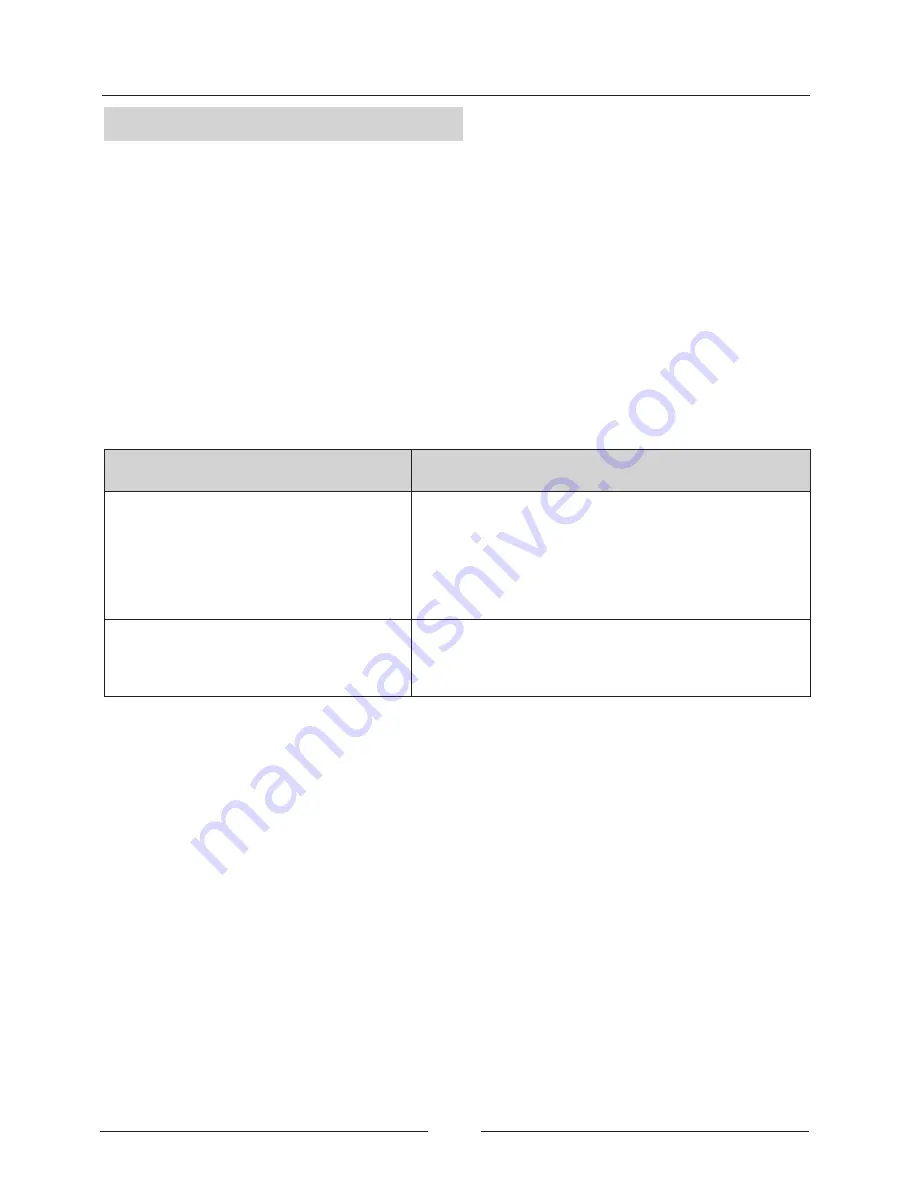
10
• The unit under supply, have rotating objects and high temperature into the pipe. Make sure to turn off electrically
the unit before to access for maintenance or revision.
• Air filter: Clean the filter (maximum each 6 months), but the clean of the filter depend on the ambient where the
units is working.
• Water filter: Realise a clean of the filter.
• Security elements: The unit include electrical elements of security( Internal thermal protection on the compressor
and motor fan, external thermal protection on the compressor and motor three phase) and cooling elements of
security like high and low pressostat pressure with electrical rearm. If limits of function of the unit is out of conditions
of work, some protections will be display.
LOCALISATION OF PROBLEMS
PROBLEMS
CAUSES
SERVICE AND MAINTENANCE
• Cut low pressure (Electrical rearm) (*)
• Cooling capacity low.
• Freeze on coil
• Air in temperature very low
• Defect on refrigerant charge.
Test that the refrigerant is correct.
• Air filter dirty
• low air flow.
• Water temperature is too low
• High water temperature
• Low air flow
• Cut high pressure (Electrical ream) (*)
• High consumption
• Thermal compressor protection cut
(*) Rearm electrically the unit turning off/on, after repair the cause which produce a cut on high and low pressure.
Summary of Contents for SNE 2
Page 14: ...14 NOTAS...
Page 15: ...SNE K OPERATION SERVICE AND INSTALLATION MANUAL...