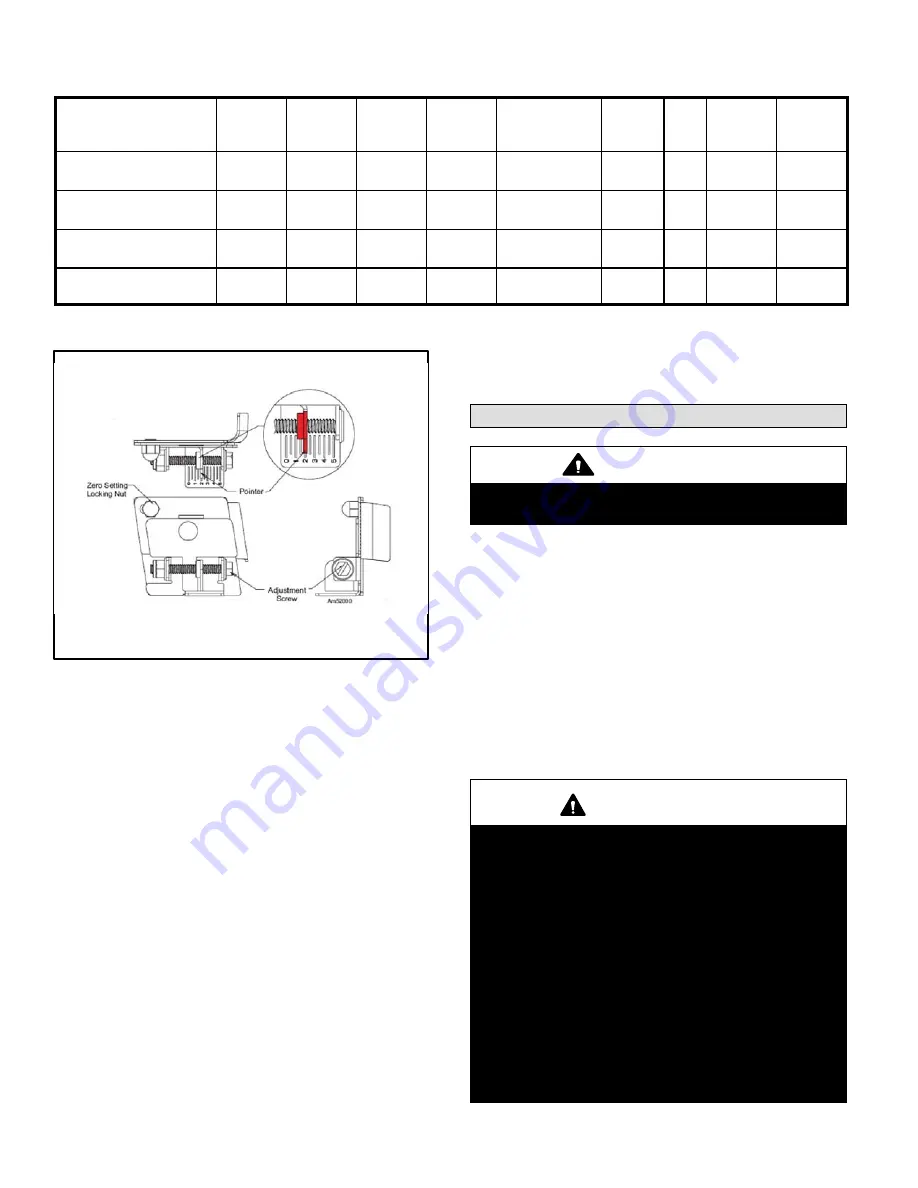
Page 20
Table 9
Burner Specifications
Unit
Burner
Number
Beckett
Spec. No.
Beckett
Air Tube
Part No.
Input
Rating
BTU/HR
Nozzle Size,
Spray, Angle, &
Pattern
Pump
Pressure
Head
Insertion
Length
Static
Plate
Diameter
SLO185UFV-79/105
103880-01
ARM2201
NX70LH
HS
79,000
0.50gph x 60°A
hollow
150
6 Slot
5”
3.00”
SLO185UFV-79/105
103880-01
ARM2201
NX70LH
HS
105,000
*0.65gph x 60 °A
hollow
150
6 Slot
5”
3.00”
SLO185UFV-124/141
103880-02
ARM2202
NX70LCH
S
124,000
0.75gph x 60°A
hollow
145
6 Slot
5”
3.25”
SLO185UFV-124/141
103880-02
ARM2202
NX70LCH
S
141,000
*0.85gph x 60°A
hollow
145
6Slot
5”
3.25”
*Nozzle must be field-installed for conversion to higher heating input.
NOTE - All nozzles are Delavan brand.
Beckett Oil Burner Nozzle Adjustment
Figure 21
3. Take a draft reading at the service hole in the flue out
let. Adjust barometric draft control in the stack to
achieve an overfire draft of -0,1” to -.02” and a breach
of -0.2 to -.04”.
4. Pull and record a smoke reading at the service hole us
ing an industry standard smoke tester.
5. If the burner is producing more than #1 smoke, adjust
the intake air using the zero setting locking nut and ad
justment screw (figure 21). Loosen the locking nut ap
proximately one turn. Turn the adjustment screw
clockwise to increase air or counterclockwise to de
crease air.
6. Once the desired smoke level is achieved, use a suit
able test instrument and take a CO
2
sample at the ser
vice hole in the flue outlet (from step1).
7. Adjust the air from step 5 to achieve the desired CO2
level.
8. Recheck smoke level.
9. Recheck draft and CO
2
reading at the service hole.
10. Using a suitable thermometer, obtain and record the
flue gas temperature at the service hole.
11. Use the CO
2
reading and the flue gas temperature
reading to determine unit efficiency.
12. When proper combustion and smoke readings have
been achieved, tighten the zero setting lock nut and
adjustment screw.
Service
CAUTION
Do not tamper with unit controls. Call your qualified
service technician.
Servicing the Air Filter
NOTE - Under no circumstances should the access panels
to the blower compartment be left off or left partially open.
Throw‐Away Type Filters
—Check filters monthly and re
place when necessary to assure proper furnace operation.
Replace filters with like kind and size filters.
Reusable Type Filters
—Filters should be checked
monthly and cleaned when necessary to assure proper fur
nace operation. Use warm water and a mild detergent. Re
place filter when dry. Permanent filters supplied with
SLO185UFV furnaces do not require oiling after cleaning.
Examine filter label for any for special instructions that may
apply.
IMPORTANT
If a highefficiency filter is being installed as part of
this system to ensure better indoor air quality, the
filter must be properly sized. Highefficiency filters
have a higher static pressure drop than standardef
ficiency glass/foam filters. If the pressure drop is
too great, system capacity and performance may be
reduced. The pressure drop may also cause the limit
to trip more frequently during the winter and the in
door coil to freeze in the summer, resulting in an in
crease in the number of service calls.
Before using any filter with this system, check the
specifications provided by the filter manufacturer
against the data given in the appropriate Lennox
Product Specifications bulletin. Additional informa
tion is provided in Service and Application Note
ACC002 (August 2000).