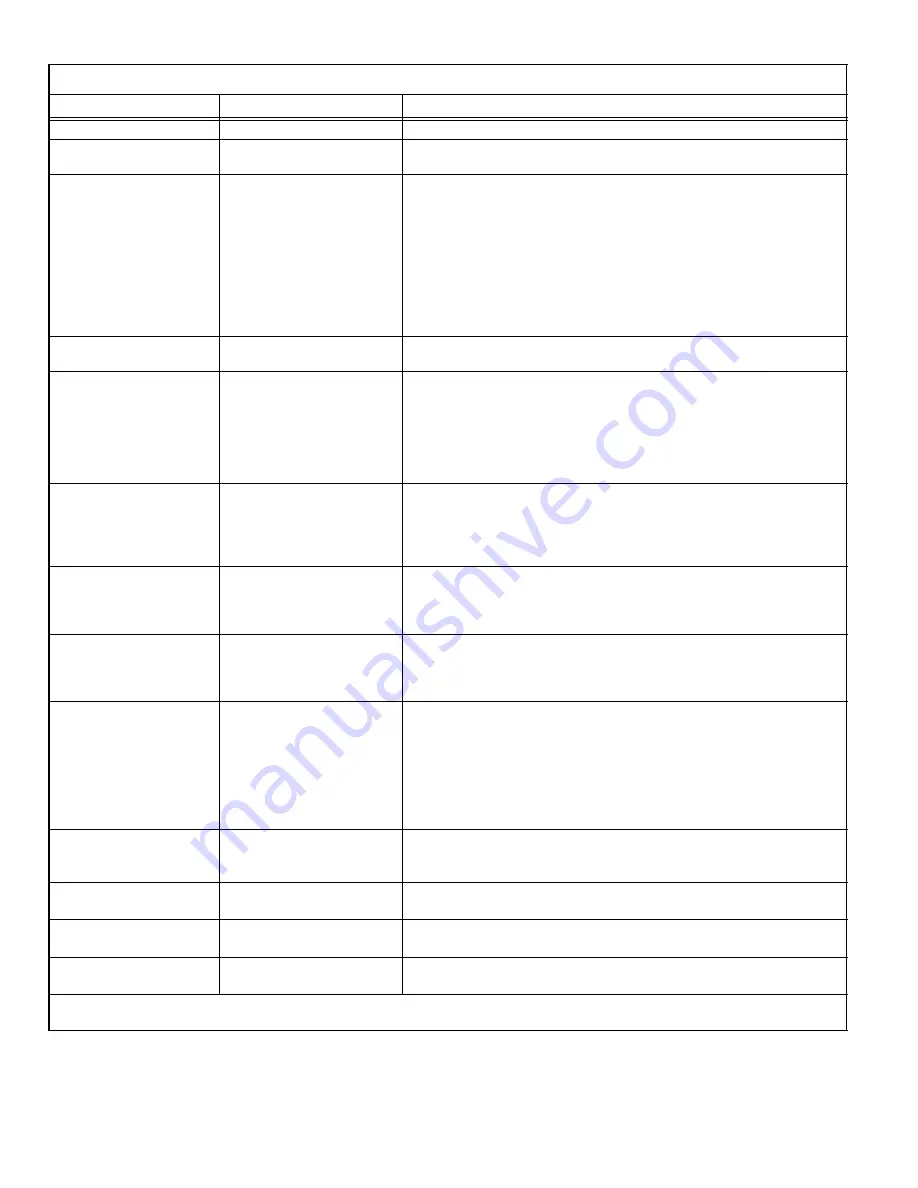
Page 8
TABLE 4
System Operation Monitor LED Troubleshooting Codes
Status LED Condition
Status LED Description
Status LED Troubleshooting Information
Green Power" LED ON
Module has power
24VAC control power is present at the module terminal.
Green Power" LED OFF
Module not powering up
Determine/verify that both R and C module terminals are connected and
voltage is present at both terminals.
Red Trip" LED ON
System and compressor
check out OK
1.
Verify Y terminal is connected to 24VAC at contactor coil.
2.
Verify voltage at contactor coil falls below 0.5VAC when off.
3.
Verify 24VAC is present across Y and C when thermostat
demand signal is present; if not present, R and C wires are reversed.
Thermostat demand signal
Y1 is present, but compres-
sor not running
1.
Compressor protector is open.
2.
Outdoor unit power disconnect is open.
3.
Compressor circuit breaker or fuse(s) is open.
4.
Broken wire or connector is not making contact.
5.
Low pressure switch open if present in the system.
6.
Compressor contactor has failed to close.
Red Trip" & Yellow
Alert" LEDs Flashing
Simultaneous flashing.
Indicates that the control circuit voltage is too low for operation.
Yellow Alert" Flash
Code 1*
Long Run Time
−
Compressor is running
extremely long run cycles
1.
Low refrigerant charge.
2.
Evaporator blower is not running.
3.
Evaporator coil is frozen.
4.
Faulty metering device.
5.
Condenser coil is dirty
.
6.
Liquid line restriction (filter drier blocked if present)
.
7.
Thermostat is malfunctioning
.
Yellow Alert" Flash
Code 2*
System Pressure Trip
−
Discharge or suction pres-
sure out of limits or
compressor overloaded
1.
High head pressure.
2.
Condenser coil poor air circulation (dirty, blocked, damaged).
3.
Condenser fan is not running.
4.
Return air duct has substantial leakage.
5.
If low pressure switch is present, see Flash Code 1 info.
Yellow Alert" Flash
Code 3*
Short Cycling
− Compres-
sor is running only briefly
1.
Thermostat demand signal is intermittent.
2.
Time delay relay or control board is defective.
3.
If high pressure switch is present, see Flash Code 2 info.
4.
If low pressure switch is present, see Flash Code 1 info.
Yellow Alert" Flash
Code 4*
Locked Rotor
1.
Run capacitor has failed.
2.
Low line voltage (contact utility).
3.
Excessive liquid refrigerant in the compressor.
4.
Compressor bearings are seized.
Yellow Alert" Flash
Code 5*
Open Circuit
1.
Outdoor unit power disconnect is open.
2.
Unit circuit breaker or fuse(s) is open.
3.
Unit contactor has failed to close.
4.
High pressure switch is open and requires manual reset.
5.
Open circuit in compressor supply wiring or connections.
6.
Unusually long compressor protector reset time due to
extreme ambient temperature.
7.
Compressor windings are damaged.
Yellow Alert" Flash
Code 6*
Open Start Circuit
− Cur-
rent only in run circuit
1.
Run capacitor has failed.
2.
Open circuit in compressor start wiring or connections.
3.
Compressor start winding is damaged.
Yellow Alert" Flash
Code 7*
Open Run Circuit
− Current
only in start circuit
1.
Open circuit in compressor start wiring or connections.
2.
Compressor start winding is damaged.
Yellow Alert" Flash
Code 8*
Welded Contactor
−
Com-
pressor always runs
1.
Compressor contactor failed to open.
2.
Thermostat demand signal not connected to module.
Yellow Alert" Flash
Code 9*
Low Voltage
− Control cir-
cuit <17VAC
1.
Control circuit transformer is overloaded
.
2.
Low line voltage (contact utility).
*Flash code number corresponds to a number of LED flashes, followed by a pause, and then repeated. Reset ALERT flash code by
removing 24VAC power from monitor; last code will display for 1 minute after monitor is powered on.