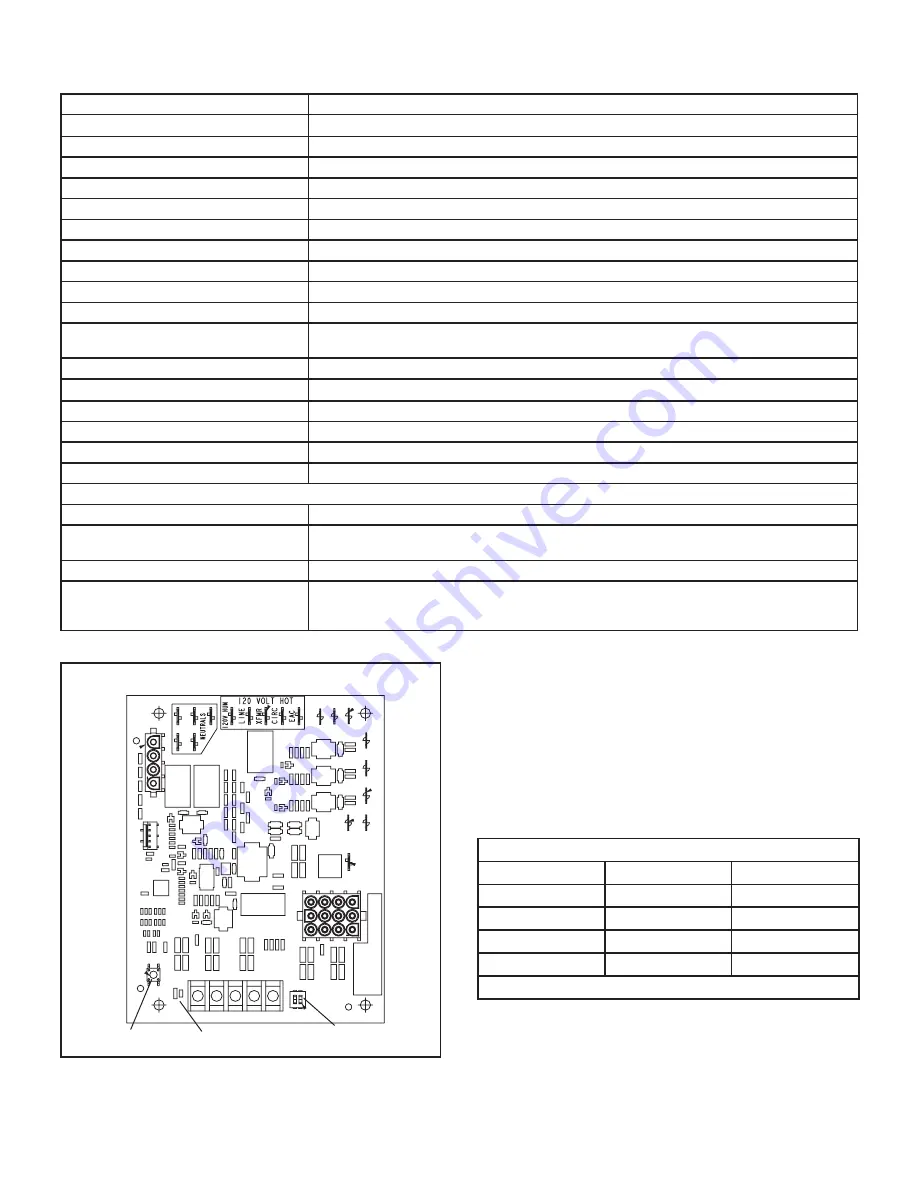
Page 9
TABLE 5
Ignition Control 107163-01
RED LED Flash Code
Diagnostic Codes / Status of Furnace
Off
No Power to Control or Board Fault Detected
On
Board Fault Detected
Fast Heartbeat
3
Call for Heat / Burner Operation
Slow Heartbeat
1
Normal Operation – Idle, Continuous Fan, or Cool
1 Flash
2
Reverse Line Voltage Polarity or Phasing of 120V power
2 Flashes
2
Improper earth ground
3 Flashes
2
Burner failed to light, or lost flame during heat demand
4 Flashes
2
Low flame signal – check flame sensor
5 Flashes
2
Watchguard – burner failed to light, exceeded maximum number of retries/recycles, 1 hour lockout
6 Flashes
2
Not used
7 Flashes
2
Primary or Secondary limit switch open or Watchguard mode – Limit Switch open longer than 3
minutes
8 Flashes
2
Roll-out Switch Open
9 Flashes
2
Pressure Switch failed to close or opened during heat demand, inducer on
10 Flashes
2
Watchguard - Pressure switch opened 5 times during a single heating demand
11 Flashes
2
Pressure switch stuck closed prior to activation of Combustion Air Inducer
12 Flashes
2
Flame sensed without gas valve energized
13 Flashes
2
Low line voltage
Notes
Note - 1
A slow heartbeat is indicated by 1s on / 1s off. It is used for idle, continuous fan and cool modes.
Note - 2
Error codes are indicated by a “rapid flash” - the LED flashes X times at ½ second on ½ second off,
remains off for 3 seconds then repeats.
Note - 3
A fast heartbeat is indicated by 0.5s on / 0.5s off. It is only used during a heat call.
Note - 4
Last 10 error codes are stored in memory including when power is shut off to the unit. - To recall,
press, and release button, most recent will be displayed first, LED off for 3 sec, then next error code
is displayed, etc. To clear error codes, depress and hold button longer than 5 seconds.
IGNITION CONTROL 107163-01
Push Button
Error Recall
Diagnostic LED
Heating Blower Off
Delay Selector Switch
FA
N
HE
AT
COOL
24VCO
M
PARKS
HUM24
FIGURE 5
Ignition Control 107163-01
The heat fan-on time of 30 seconds is not adjustable. The
cool fan-on time of 2 seconds is not adjustable. The heat
fan-off delay (amount of time that the blower operates af
-
ter the heat demand has been satisfied) may be adjusted
by changing the two position dip switch on the integerated
control, to one of four selections. Blower off delay is facto
-
ry set at 90 seconds. For other blower off delay settings,
please refer to the following chart:
Blower Delay Select
SW2-1
SW2-2
60
OFF
ON
90
OFF
OFF
120
ON
OFF
180
ON
ON
Factory Setting is 90