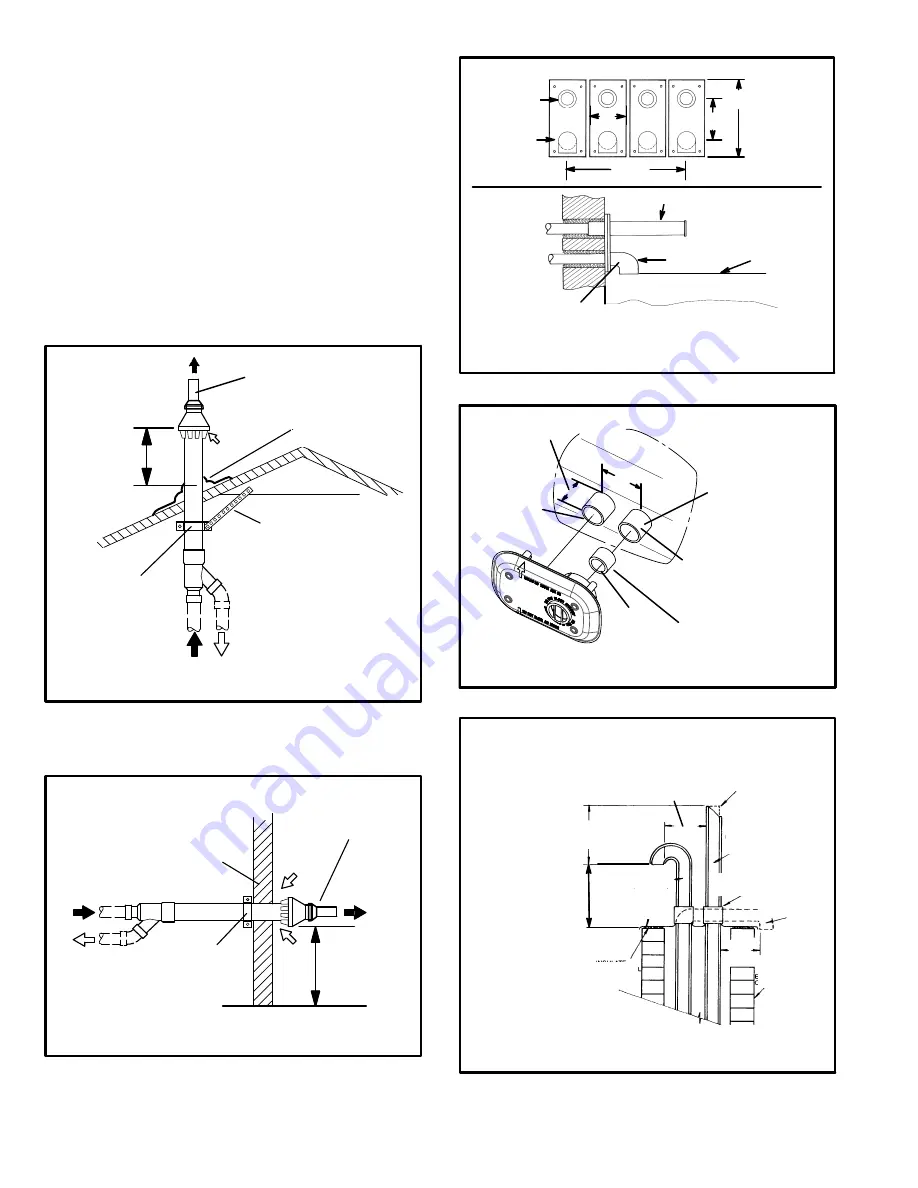
Page 32
7. If intake and exhaust piping must be run up a side wall
to position above snow accumulation or other ob
structions, piping must be supported. At least one
bracket must be used within 6” from the top of the el
bow and then every 24” (610mm) as shown in figure
41, to prevent any movement in any direction. When
exhaust and intake piping must be run up an outside
wall, the exhaust piping must be terminated with pipe
sized per table 17.The intake piping may be equipped
with a 90° elbow turndown. Using turndown will add 5
feet (1.5m) to the equivalent length of the pipe.
8. A multiple furnace installation may use a group of up to
four terminations assembled together horizontally, as
shown in figure 38.
FIGURE 36
DIRECT VENT CONCENTRIC ROOFTOP TERMINATION
71M80, 69M29 or 60L46 (US)
44W92 or 44W93 (Canada)
Minimum
Above Average
Snow
Accumulation
SHEET METAL STRAP
(Clamp and sheet metal strap
must be field installed to support
the weight of the termination kit.)
FLASHING
(Not Furnished)
CLAMP
FIELD-PROVIDED
REDUCER MAY BE REQUIRED
TO ADAPT LARGER VENT
PIPE SIZE TO TERMINATION
1 1/2” (38mm) accelerator
provided on 71M80 & 44W92
kits for ML193UH045P24B,
070P24B & 070P36B
12” (305mm)
INTAKE
AIR
EXHAUST
VENT
12” (305mm) Min.
above grade or
average snow
accumulation.
FIGURE 37
DIRECT VENT CONCENTRIC WALL TERMINATION
71M80, 69M29 or 60L46 (US)
44W92 or 44W93 (Canada)
INTAKE
AIR
INTAKE
AIR
INTAKE
AIR
OUTSIDE
WALL
GRADE
CLAMP
(Not Furnished)
FIELD-PROVIDED
REDUCER MAY BE REQUIRED
TO ADAPT LARGER VENT
PIPE SIZE TO TERMINATION
EXHAUST
VENT
1-1/2” (38mm) accelerator
provided on 71M80 & 44W92
kits for ML193UH045P24B,
070P24B & 070P36B
EXHAUST
VENT
FIGURE 38
EXHAUST
VENT
INTAKE
AIR
5-1/2”
(140mm)
Front View
12”
(305mm)
5”
(127mm)
18” MAX.
(457mm)
EXHAUST VENT
INTAKE
AIR
OPTIONAL VENT TERMINATION FOR MULTIPLE UNIT
INSTALLATION OF DIRECT VENT WALL TERMINATION KIT
(30G28 or 81J20)
Inches (mm)
Side View
12” (305mm) Min.
above grade or
average snow
accumulation.
optional intake elbow
FIGURE 39
2” EXTENSION FOR 2” PVC
PIPE1” EXTENSION FOR 3”
PVC PIPE
1-1/2” ACCELERATOR
(
all -45, -070 and -090 units)
FURNACE
EXHAUST
PIPE
FURNACE
INTAKE
PIPE
4''
GLUE EXHAUST
END FLUSH INTO
TERMINATION
FLAT
SIDE
FLUSH-MOUNT SIDE WALL TERMINATION
51W11 (US) or 51W12 (Canada)
ML193UH DIRECT VENT APPLICATION
USING EXISTING CHIMNEY
FIGURE 40
3” - 8”
(76mm-
203mm)
STRAIGHT-CUT OR
ANGLE-CUT IN DIRECTION
OF ROOF SLOPE *
EXHAUST VENT
1/2” (13mm)
WEATHERPROOF
INSULATION
SHOULDER OF FITTINGS
PROVIDE SUPPORT
OF PIPE ON TOP PLATE
ALTERNATE
INTAKE PIPE
INTAKE PIPE
INSULATION (optional)
EXTERIOR
PORTION OF
CHIMNEY
INSULATE
TO FORM
SEAL
SHEET
METAL TOP
PLATE
*SIZE TERMINATION
PIPE PER TABLE 17.
Minimum 12” (305MM)
above chimney top
plate or average snow
accumulation
8” - 12”
(203mm - 305mm)
3”-8”
(76mm-203mm)
NOTE - Do not discharge exhaust gases directly into any chimney or vent stack. If ver
tical discharge through an existing unused chimney or stack is required, insert piping
inside chimney until the pipe open end is above top of chimney and terminate as illus
trated. In any exterior portion of chimney, the exhaust vent must be insulated.