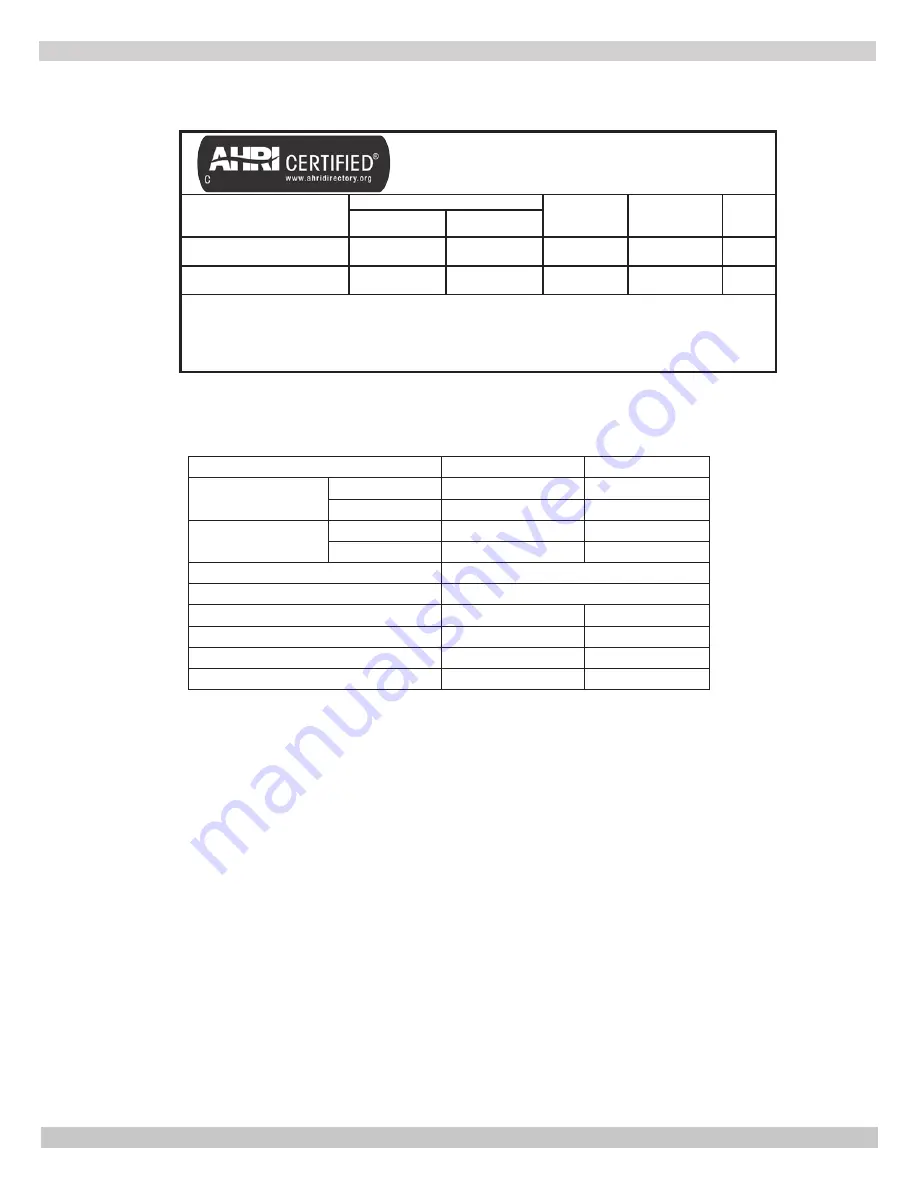
53
240012994 Rev. B [08/31/2020]
12 - RATINGS AND CAPACITIES
12 TECHNICAL DATA
12.1 Ratings and Capacity
Model Number
CH Input, MBH
(1)
(1)(2) CH
Heating
Capacity, MBH *
(1)(3)
Net AHRI
Rating Water, MBH
(2)
AFUE%
Maximum
Minimum
GCWB95W-150
125
22
113
98
95.0
GCWB95W-205
164
29.5
153
133
95.0
(1) 1000 Btu/hr (British Thermal Units Per Hour)
(2) Heating Capacity and AFUE (Annual Fuel Utilization Efficiency) are based on DOE (Department of Energy) test procedures.
(3) Net AHRI Ratings based on piping and pickup allowance of 1.15. Contact Technical Support before selecting boiler for installations having
unusual piping and pickup requirements, such as intermittent system operation, extensive piping systems, etc.
*Max CH Supply temp 176° F (80°C)
Item
GCWB95W-150
GCWB95W-205
Input Ratings (MBH)
Min
22
29.5
Max
153
205
Output Ratings (MBH)
Min
19
26
Max
136
180
Domestic Water Pressure
2.9 psi (0.2 bar) - 116 psi (8.0 bar)
Minimum Flow Rate
0.50 GPM
Maximum Flow Rate
3.50 gpm
5.00 gpm
Flow Rate 77°F (43°C) Temp. Rise
3.25 gpm
4.65 gpm
DHW Supply Connection Size
1/2"NPT
3/4"NPT
Cold Water Input Connection Size
1/2"NPT
3/4"NPT
12.2 Domestic Hot Water Specifications
*Max DHW temp 140° F (60° C)
Factory set at 120° F (40° C)