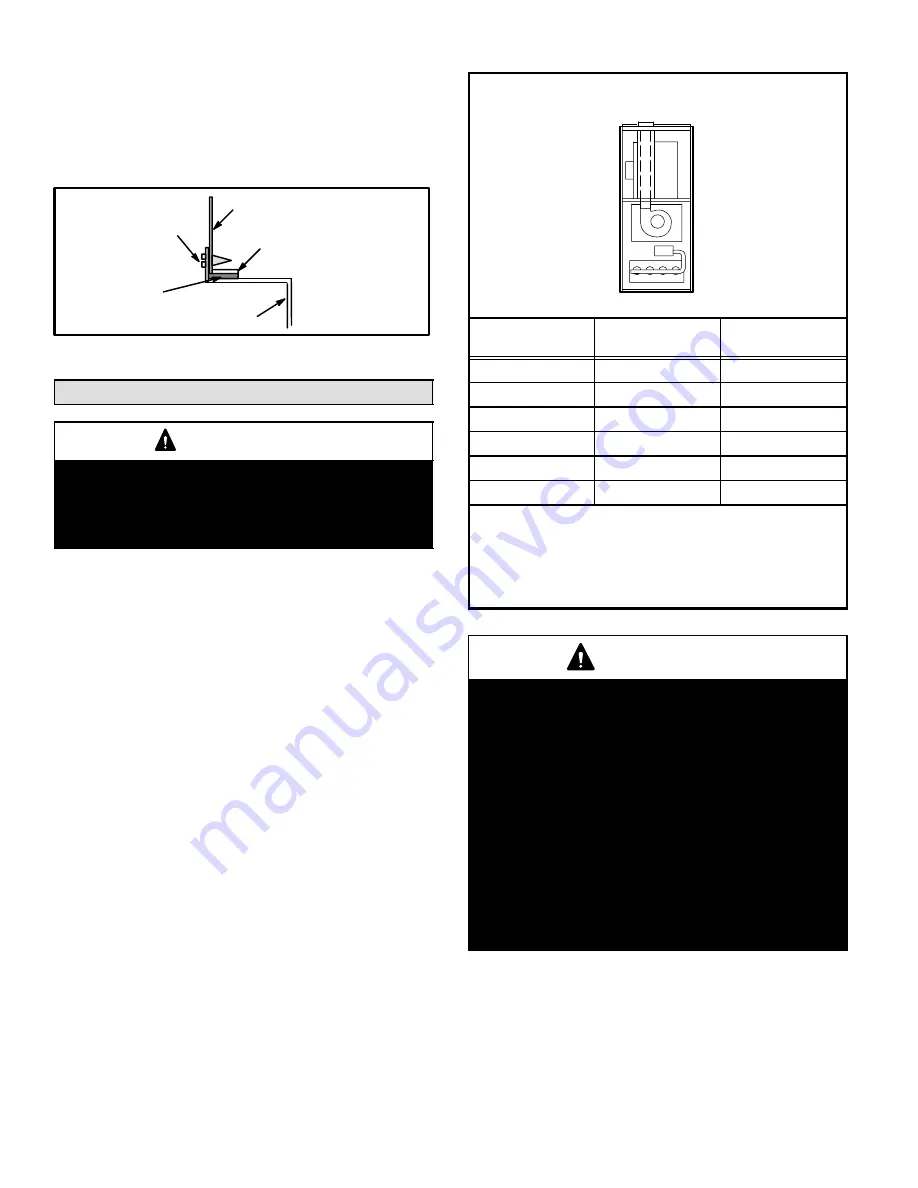
Page 10
506178−01 05/2009
4 − In closet installations, it may be impossible to install
sheet metal screws from the outside. In this case,
make plenum with a removable front and install
screws from the inside (See figure 8).
5 − Make certain that an adequate seal is made.
SECURE FROM IN-
SIDE CABINET
HEMMED EDGE
FIBERGLASS
SEALING STRIP
(Field Provided)
CABINET SIDE
PANEL
PLENUM
Side View
FIGURE 8
Setting Equipment
WARNING
Do not install the furnace on its front or its back. Do
not connect the return air ducts to the back of the fur-
nace. Doing so will adversely affect the operation of
the safety control devices, which could result in per-
sonal injury or death.
Install the G60DF(X) gas furnace as shipped.
Do not
install the furnace horizontally.
Select a location that allows for the required clearances
that are listed on the unit nameplate. Also consider gas
supply connections, electrical supply, vent connection, and
installation and service clearances [24 inches (610 mm) at
unit front].
The unit must be level.
NOTE − Units with 1/2 hp blower motors are equipped with
three flexible legs and one rigid leg. The rigid leg is
equipped with a shipping bolt and a flat white plastic wash-
er (rather than the rubber mounting grommet used with a
flexible mounting leg).
The bolt and washer must be re-
moved before the furnace is placed into operation.
Af-
ter the bolt and washer have been removed, the rigid leg
will not touch the blower housing.
Downflow Application
Allow for clearances to combustible materials as indi-
cated on the unit nameplate. Minimum clearances for
closet or alcove installations are shown in figure 9.
Downflow Application Installation Clearances
Top
Bottom
Left Side
Right Side
Type of Vent
Connector
Type C
Type B1
Top
1 in. (25 mm)
1 in. (25 mm)
*Front
3 in. (76 mm)
3 in. (76 mm)
Back
0
0
Sides
0
†
0
Vent
6 in. (152 mm)
1 in. (25 mm)
Floor
NC††
NC††
*Front clearance in alcove installation must be 24 in. (610 mm).
Maintain a minimum of 24 in. (610 mm) for front service access.
†Left side requires 3 in. if a single wall vent is used on 14 −1/2 in.
cabinets, or 2 in. if a single wall vent is used on 17 − 1/2 in. cabinets.
††The furnace may be installed on a combustible wood floor if an
optional additive base is installed between the furnace and the
combustible floor.
FIGURE 9
WARNING
Improper installation of the furnace can result in per-
sonal injury or death. Combustion and flue products
must never be allowed to enter the return air system
or the living space. Use screws and joint tape to seal
the return air system to the furnace.
In platform installations with bottom return air, the
furnace should be sealed airtight to the return air ple-
num. A door must never be used as a portion of the
return air duct system. The base must provide a
stable support and an airtight seal to the furnace. Al-
low absolutely no sagging, cracks, gaps, etc.
The return and supply air duct systems must never
be connected to or from other heating devices such
as a fireplace or stove, etc. Fire, explosion, carbon
monoxide poisoning, personal injury and/or proper-
ty damage could result.