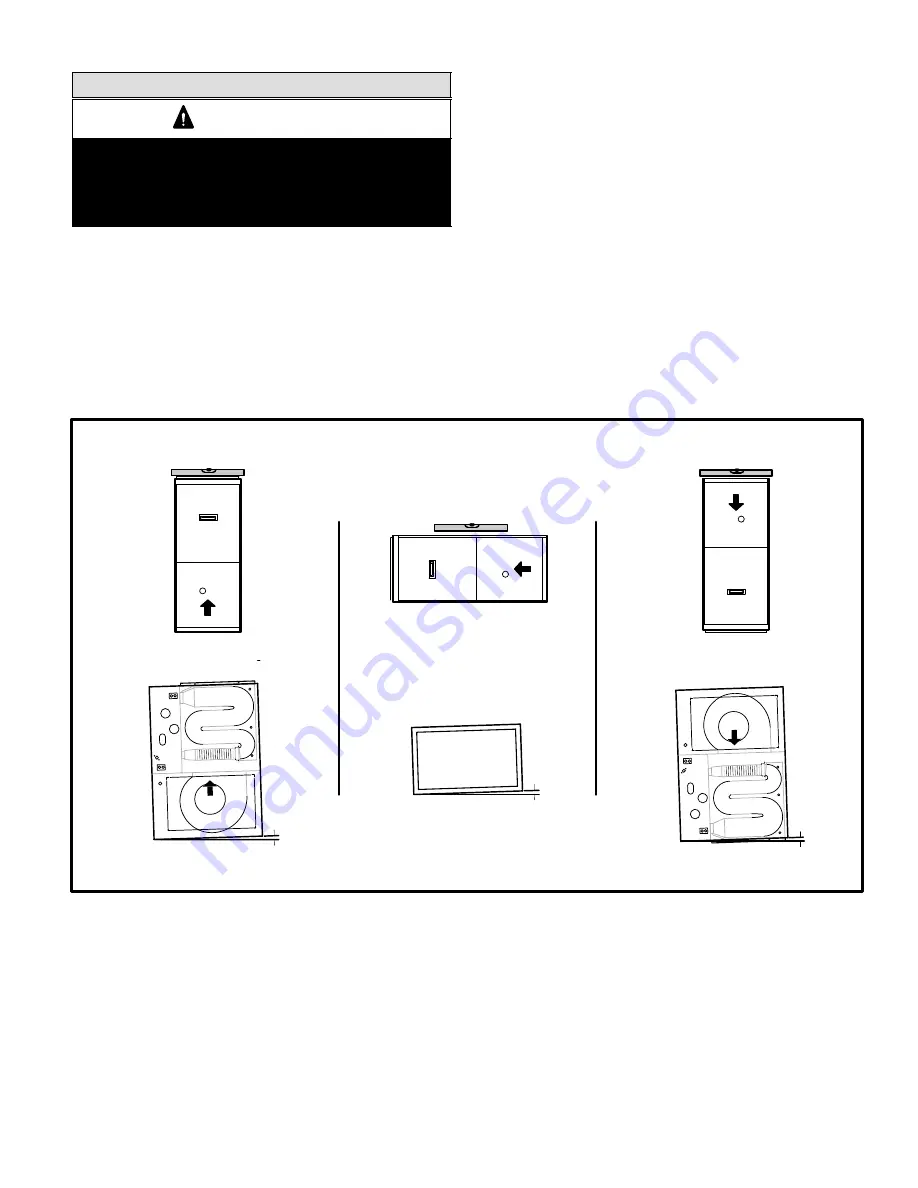
Page 9
Installation − Setting Equipment
WARNING
Do not install the furnace on its front or its back. Do
not connect the return air ducts to the back of the fur-
nace. Doing so will adversely affect the operation of
the safety control devices, which could result in per-
sonal injury or death.
Select a location that allows for the required clearances
that are listed on the unit nameplate. Also consider gas
supply connections, electrical supply, vent connection,
condensate trap and drain connections, and installation
and service clearances [24 inches (610 mm) at unit
front].
The unit must be level from front to back and side
to side. The unit may be tilted slightly (maximum 1/2 in.)
from back to front to aid in the draining of the heat ex-
changer. See figure 7.
NOTE
− 1/3 hp blower motors are equipped with four flex-
ible mounting legs, and 1/2 hp blower motors are equipped
with three flexible legs and one rigid leg. The rigid leg is
equipped with a shipping bolt and a flat white plastic wash-
er (rather than the rubber mounting grommet used with a
flexible mounting leg).
The bolt and washer must be re-
moved before the furnace is placed into operation.
Af-
ter the bolt and washer have been removed, the rigid leg
will not touch the blower housing.
NOTE
− The G51MP−60D−135 units are equipped with a
shipping pad under the blower housing. Remove the ship-
ping pad prior to opertion.
Allow for clearances to combustible materials as indicated
on the unit nameplate. Minimum clearances for closet or al-
cove installations are shown in figures 8, 13 and 17.
FIGURE 7
SETTING EQUIPMENT
UPFLOW APPLICATION
DOWNFLOW APPLICATION
HORIZONTAL APPLICATION
FRONT VIEW
SIDE VIEW
FRONT VIEW
END VIEW
FRONT VIEW
SIDE VIEW
AIR FLOW
AIR FLOW
AIR FLOW
UNIT
FRONT
AIR FLOW
AIR FLOW
UNIT
FRONT
UNIT
FRONT
1/2"
max.
1/2"
max.
1/2"
max.
UNIT MUST BE LEVEL SIDE−TO−SIDE IN ALL APPLICATIONS.
UNIT SHOULD BE LEVEL FROM LEFT TO RIGHT BUT MAY BE
TILTED SLIGHTLY (MAX. 1/2") FROM BACK TO FRONT
TO AID IN THE DRAINING OF THE HEAT EXCHANGER.