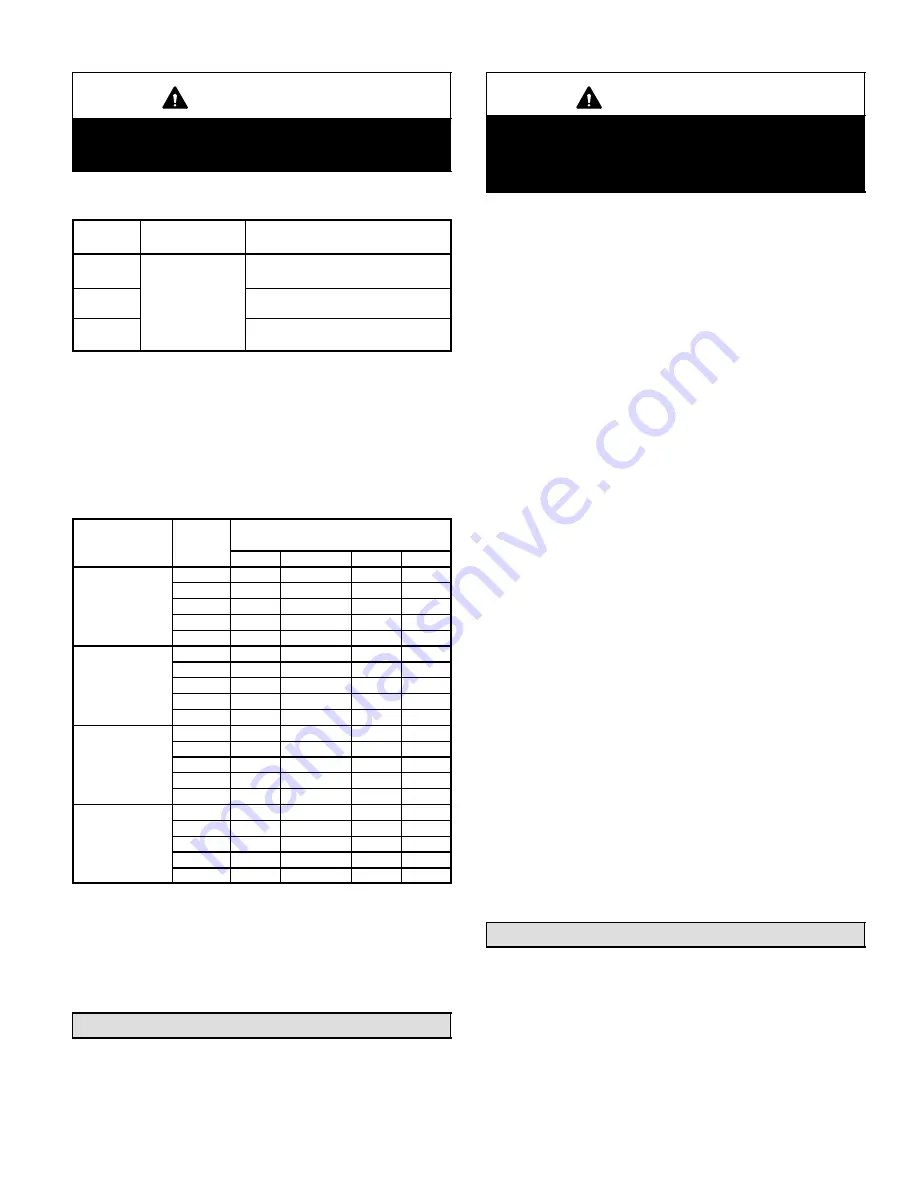
Page 19
IMPORTANT
Do not use screens or perforated metal in exhaust
terminations. Doing so will cause freeze−ups and
may block the terminations.
TABLE 6
MINIMUM VENT PIPE LENGTHS
G51MP
MODEL
MIN. EQUIV.
VENT LENGTH
EXAMPLE
045, 070,
090
15 ft.*
5 ft. plus 2 elbows of 2", 2−1/2", 3"
or 4" diameter pipe
110**
5 ft. plus 2 elbows of 2", 2−1/2", 3" or
4" diameter pipe
135***
5 ft. plus 2 elbows of 3" or 4"
diameter pipe
*Any approved termination may be added to the minimum equivalent length
listed.
**G51MP−48C−110 and G51MP−60C−110 must have 90° street ell (supplied or
field replacement Canadian kit) installed directly into unit flue collar.
***G51MP−60D−135 must have 3" to 2" reducing ell (supplied or field replace-
ment Canadian kit) installed directly into unit flue collar.
TABLE 7
MAXIMUM VENT PIPE LENGTHS
DIRECT (2 PIPE) AND NON−DIRECT (1 PIPE) APPLICATIONS
ALTITUDE
G51MP
MODEL
MAXIMUM EQUIVALENT VENT
LENGTH FEET
2" dia.
2−1/2" dia.
3" dia.
4" dia.
0 − 2000
(0 − 609 m)
045
110
135
160
250
070
70
135
160
250
090
50
100
125
225
110*
30
70
125
200
135**
n/a
n/a
***125
180
2001 − 4500
(610 − 1371 m)
045
110
135
160
250
070
70
135
160
250
090
50
100
125
225
110*
20
70
125
200
135**
n/a
n/a
***90
180
4501−7500
(1372−2286 m)
045
110
135
160
250
070
70
135
160
250
090
30
100
125
225
110*
n/a
70
125
200
135**
n/a
n/a
***90
180
7501 − 10000
(2287 − 3048 m)
045
110
135
160
250
070
70
135
160
250
090
n/a
100
125
225
110*
n/a
70
125
200
135**
n/a
n/a
***90
180
n/a −− Not allowed.
*G51MP−48C−110 and G51MP−60C−110 must have 90° street ell (supplied or
field replacement Canadian kit) installed directly into unit flue collar.
**G51MP−60D−135 must have 3" to 2" reducing ell (supplied or field replace-
ment Canadian kit) installed directly into unit flue collar.
***90° elbows used in configuration of G51MP−60D−135 vent, must be lim-
ited to 3" sweep elbows.
Joint Cementing Procedure
All cementing of joints should be done according to the
specifications outlined in ASTM D 2855.
WARNING
DANGER OF EXPLOSION!
Fumes from PVC glue may ignite during system
check. Allow fumes to dissipate for at least 5 minutes
before placing unit into operation.
1 − Measure and cut vent pipe to desired length.
2 − Debur and chamfer end of pipe, removing any ridges
or rough edges. If end is not chamfered, edge of pipe
may remove cement from fitting socket and result in a
leaking joint.
3 − Clean and dry surfaces to be joined.
4 − Test fit joint and mark depth of fitting on outside of pipe.
5 − Uniformly apply a liberal coat of PVC primer for PVC or
use a clean dry cloth for ABS to clean inside socket
surface of fitting and male end of pipe to depth of fitting
socket.
NOTE
− Furnace flue collar and air inlet fitting are both
made of ABS material. Use transition solvent cement
when joining ABS fittings to PVC pipe.
6 − Promptly apply solvent cement to end of pipe and in-
side socket surface of fitting. Cement should be ap-
plied lightly but uniformly to inside of socket. Take
care to keep excess cement out of socket. Apply sec-
ond coat to end of pipe.
NOTE
− Time is critical at this stage. Do not allow prim-
er to dry before applying cement.
7 − Immediately after applying last coat of cement to pipe,
and while both inside socket surface and end of pipe
are wet with cement, forcefully insert end of pipe into
socket until it bottoms out. Turn PVC pipe 1/4 turn dur-
ing assembly (but not after pipe is fully inserted) to dis-
tribute cement evenly. DO NOT turn ABS or cellular
core pipe.
NOTE
− Assembly should be completed within 20 sec-
onds after last application of cement. Hammer blows
should not be used when inserting pipe.
8 − After assembly, wipe excess cement from pipe at end
of fitting socket. A properly made joint will show a
bead around its entire perimeter. Any gaps may indi-
cate a defective assembly due to insufficient solvent.
9 − Handle joints carefully until completely set.
Venting Practices
The thickness of construction through which vent pipes
may be installed is 24" (610mm) maximum and 3/4"
(19mm) minimum.
1 − Use recommended piping materials for exhaust pip-
ing.
2 − Secure all joints, including drip leg, gas-tight using ap-
proved cement.