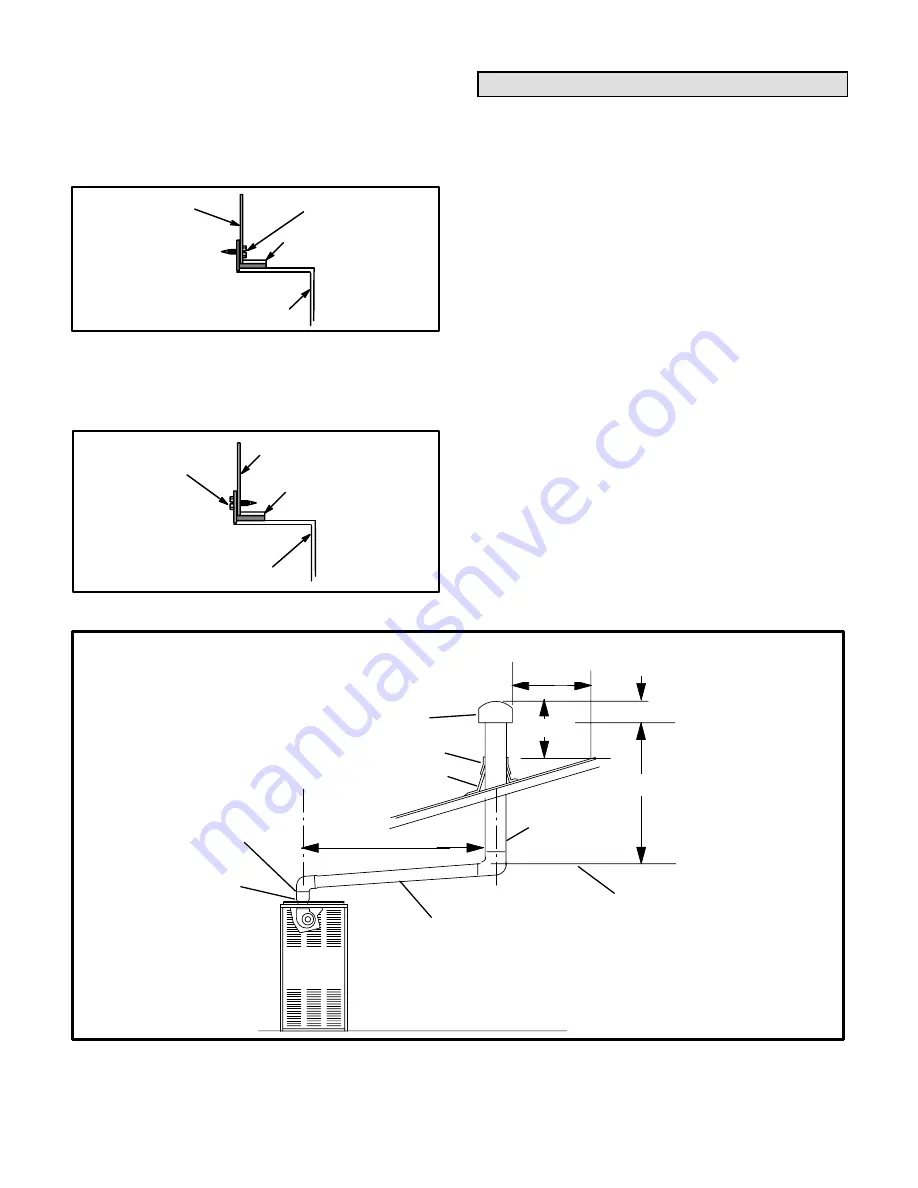
Page 10
In downflow applications, use the following steps when
installing return air plenum:
1 - Flange bottom edge of plenum with a hemmed edge.
See
figure 12.
2 - In all cases, secure the plenum to the top flanges of
the furnace using sheet metal screws. See
figure 12.
SECURE
HEMMED EDGE
PLENUM
CABINET SIDE PANEL
FIGURE 12
3 - In cupboard installations, it may be necessary to
install sheet metal screws from the inside. If this is the
case, make plenum with a removable front to install
screws as shown in figure 13.
SECURE
FROM
INSIDE
HEMMED EDGE
CABINET SIDE PANEL
PLENUM
FIGURE 13
Venting
The G24MCE unit is not certified for common venting.
A flue adapter is supplied with the furnace. It must be fieldĆ
installed between the induced draught fan flue outlet and
the flue connector using one or two corrosion-resistant
sheet metal screws.
Modification of or failure to install
the adapter will cause unsafe unit operation and will
void unit certification.
The flue adapter does not require
insulation.
VERTICAL FLUE USING METAL FLUE PIPE
The flue system should be of the same nominal diameter
as the adapter supplied with the unit and should be fitted
inside the adapter either directly or using a connector deĆ
signed for the flue system used. Where it is not possible to
use the same nominal diameter, a larger size may be
used with an appropriate conversion piece to suit the unit
adapter. A flue system of smaller nominal diameter than
the unit adapter must not be used.
NOTE - Use these instructions as a guide. They do not suĆ
persede local codes.
Size and install the G24MCE vertical flue per local codes
and regulations and these instructions.
See figure 14 for typical application of a vertical flue using
twin wall metal flue pipe.
DOUBLE
WALL
FLUE PIPE
VERTICAL FLUE USING METAL FLUE PIPE
FLUE
CONNECTOR
(Double-walled, single-walled pipe)
FLUE
ADAPTER
STORM COLLAR
FLASHING
FLUE CAP
.61M (2 FT.)
MINIMUM
MIN. LENGTH - AS SHORT AS PRACTICAL
MAXIMUM LENGTH - SEE NOTE AT SIDE
1M (3 FT.)
MINIMUM
HIGHEST FLUE
CONNECTOR
POINT
3.05M (10 FT.)
MINIMUM
1.5M (5 FT.)
MINIMUM
STRAIGHT PIPE
FIRST 152mm (6")
Note: See the regulations that are in force in the
country of installation for flue connector sizing.
FIGURE 14