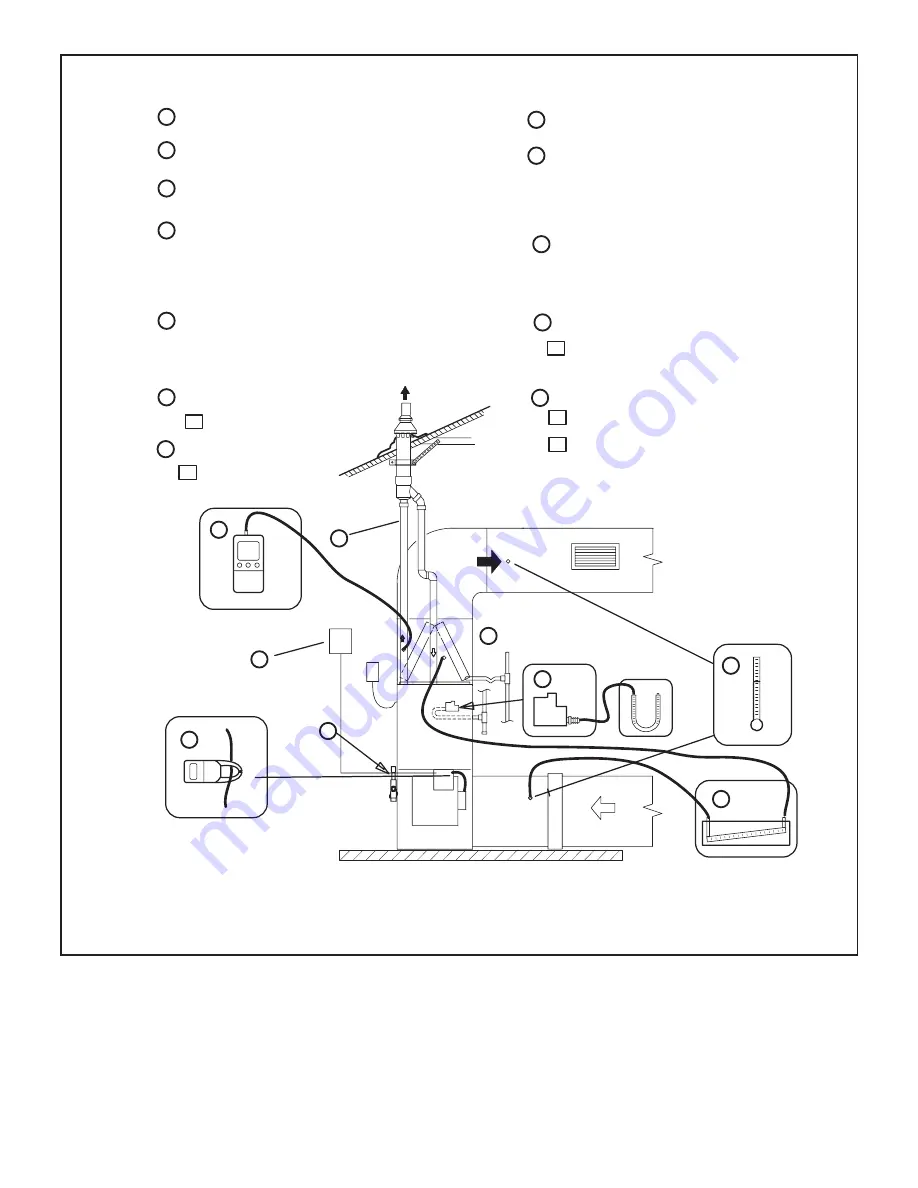
Page 50
Contractor's: Name_________________________Telephone_____________Checklist Completed____________________
Job Address_____-________________________________Technician's Name___________________________________
1
HEATING MODE
GAS MANIFOLD PRESSURE “W.C._____
COMBUSTION SAMPLE CO
2
%
______
CO PPM_______
2
INDOOR BLOWER AMPS______
3
TEMPERATURE RISE
4
Supply Duct Temperature ________
Return Duct Temperature
_
_____
Temperature Rise = ________
TOTAL EXTERNAL STATIC
5
Supply External Static _______
Return External ______
Total External Static = _______
CONDENSATE LINE
6
Leak Free
VENT PIPE
7
Leak Free
COOLING MODE
INDOOR BLOWER AMPS______
3
TEMPERATURE DROP
Return Duct Temperature _________
Supply Duct Temperature
_
_______
Temperature Drop = _________
4
DRAIN LINE
8
Leak Free
THERMOSTAT
Adjusted and Programmed
Explained Operation to Owner
9
SUPPLY
AIR
Blower Motor Amps
Duct Static
Thermostat
Gas Manifold Pressure
1
2
3
4
5
6
7
8
9
Temperatures
RETURN AIR
Combustion CO
2
UNIT OPERATION
TOTAL EXTERNAL STATIC (dry coil)
Supply External Static _______
Return External ______
Total External Static = _______
5