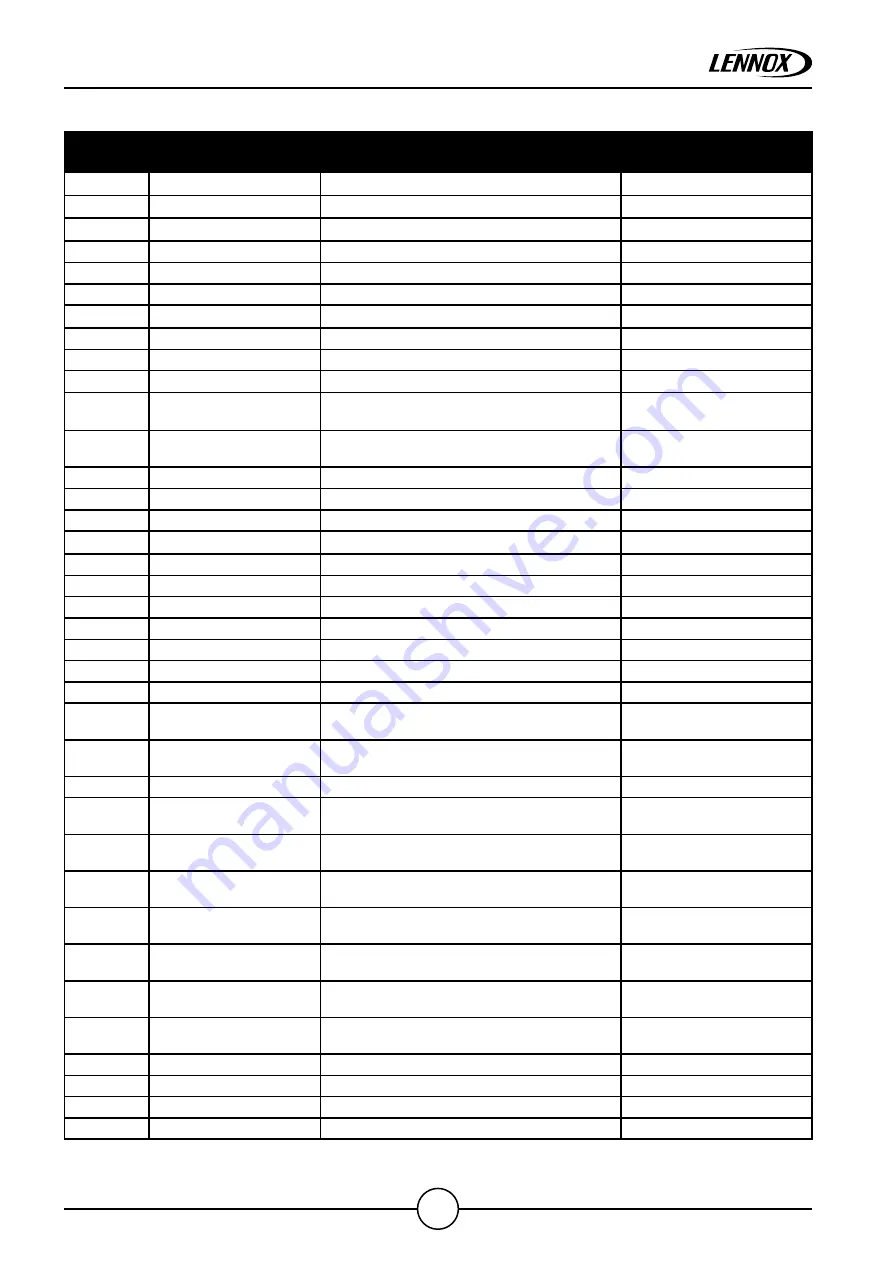
www.lennoxemea.com
e-MovAir-IOM-20.04-EN
26
e-MovAir-IOM-20.04-EN
13.0. LIST AND DESCRIPTION OF ALARMS ON DISPLAY
ALARM
NUMBER
ALARMS
ALARMS DESCRIPTION
REARM
1
Clock Alarm
Clock PCO Alarm
2
Memory Alarm
Internal memory Alarm
3
Alarm U1
Probe broken or disconnected
4
Alarm U2
Probe broken or disconnected
5
Alarm U3
Probe broken or disconnected
6
Alarm U4
Probe broken or disconnected
7
Alarm U5
Probe broken or disconnected
8
Alarm U6
Probe broken or disconnected
9
Alarm U7
Probe broken or disconnected
10
Alarm U8
Probe broken or disconnected
11
Safety Damper Open
Safety damper not opened after movement
time
Manual
12
Smoke-fire Alarm
Doors, fire, smoke sensor alarm
Manual strong (5 seconds
alarm button pressed)
13
Dirty filter warning
Filter warning
Auto
14
Dirty filter Alarm
Filter alarm
Auto
15
Fans thermal prot.
Fans thermal protection
Auto
16
Alarm U9
Probe broken or disconnected
17
Alarm U10
Probe broken or disconnected
18
Alarm U11
Probe broken or disconnected
19
Alarm U12
Probe broken or disconnected
20
21
Compr. 1 thermal prot.
Compressor 1 thermal protection
22
Low press. switch c1
Low pressure switch circuit 1
Auto
23
High press. switch c1
High pressure switch circuit 1
Auto
24
Too many low sw c1
Too many low pressure switch alarm in
monitor time
Manual strong
25
Too many high sw c1
Too many high pressure switch alarm in
monitor time
Manual strong
26
Out of Enevelope c1
Compressor work out of envelope
Auto
27
Too many out Envel. c1
Too many out of enevelope alarm in monitor
time
Manual strong
28
High press. elec. c1
Condensation pressure over threshold circuit
1
Auto
29
Too many high elec. c1
Too many condensation pressure over
threshold in monitor time
Manual strong
30
out of limit time c1
Compressor is working out of limit for long
time
Auto
31
Too many out limit c1
Too many compressor out of limit in monitor
time
Manual strong
32
Low press. elec. c1
Evaporation pressure under threshold circuit
1
Auto
33
Too many low elec. c1
Too many evaporation pressure under
threshold in monitor time
Manual strong
34
35
36
37
IN
DEVEL
OPMENT
/PRELIMINAR