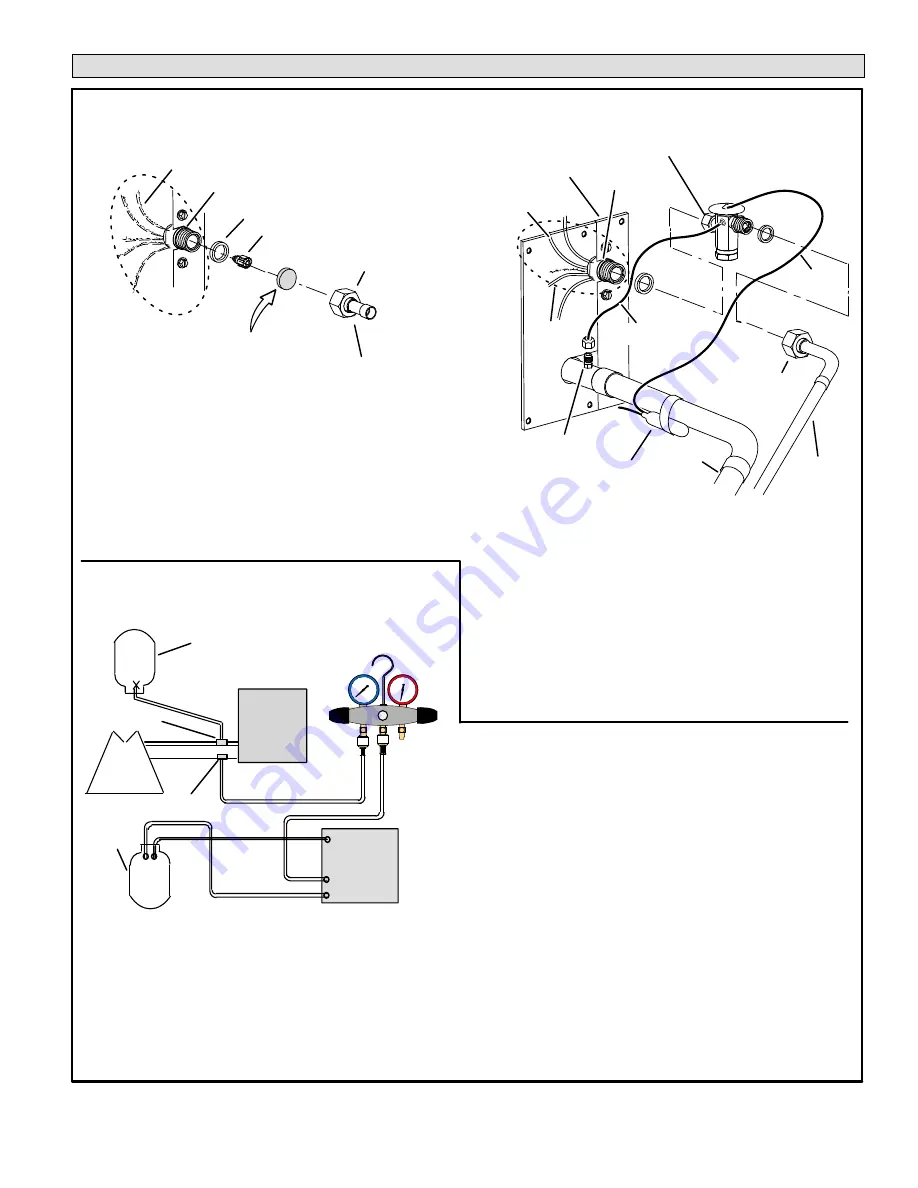
Page 11
SL18XP1 SERIES
STEP 4 -- REFRIGERANT PIPING -- Removing Existing Indoor Metering Device
SENSING
LINE
TEFLON
®
RING
FIXED ORIFICE
BRASS NUT
LIQUID LINE ASSEMBLY
(INCLUDES STRAINER)
LIQUID LINE ORIFICE HOUSING
DISTRIBUTOR TUBES
DISTRIBUTOR
ASSEMBLY
REMOVE AND DISCARD
WHITE TEFLON
®
SEAL
(IF PRESENT)
TYPICAL EXISTING FIXED ORIFICE
REMOVAL PROCEDURE
(UNCASED COIL SHOWN)
TYPICAL EXISTING EXPANSION VALVE REMOVAL
PROCEDURE (UNCASED COIL SHOWN)
TWO-PIECE PATCH PLATE
(UNCASED COIL ONLY)
VAPOR
LINE
DISTRIBUTOR
ASSEMBLY
DISTRIBUTOR
TUBES
LIQUID
LINE
MALE EQUALIZER
LINE FITTING
EQUALIZER
LINE
CHECK
EXPANSION
VALVE
TEFLON®
RING
STUB END
TEFLON
®
RING
SENSING BULB
LIQUID LINE
ORIFICE
HOUSING
LIQUID LINE
ASSEMBLY WITH
BRASS NUT
LOW
HIGH
EXISTING
INDOOR
UNIT
GAUGE
MANIFOLD
CYLINDER CONTAINING
CLEAN HCFC-22* TO BE
USED FOR FLUSHING
(Positioned to deliver liquid
refrigerant)
LIQUID LINE SERVICE
VALVE
INLET
DISCHARGE
TANK
RETURN
CLOSED
OPENED
RECOVERY
CYLINDER
RECOVERY MACHINE
NEW
OUTDOOR
UNIT
VAPOR LINE
SERVICE VALVE
V
APOR
LIQUID
1
A.
HCFC-22 cylinder with clean refrigerant* (positioned to deliver liquid
refrigerant) to the vapor service valve.
B.
HCFC-22 gauge set (low side) to the liquid line valve.
C.
HCFC-22 gauge set center port to inlet on the recovery machine with an
empty recovery tank connected to the gauge set.
D.
Connect recovery tank to recovery machine per machine instructions.
CONNECT GAUGES AND EQUIPMENT FOR
FLUSHING PROCEDURE
A
B
C
D
OR
FLUSHING LINE SET
The line set and indoor unit coil must be flushed with at least the same
amount of clean refrigerant* that previously charged the system.
Check the charge in the flushing cylinder before proceeding.
1A
2
3
1B
1. On fully cased coils, remove the coil access and plumbing panels.
2. Remove any shipping clamps from the liquid line and distributor as
sembly.
3. Using two wrenches, disconnect liquid line from liquid line orifice hous
ing. Take care not to twist or damage distributor tubes during this pro
cess.
4. Remove and discard fixed orifice, valve stem assembly (if present)
and Teflon
®
washer as illustrated above.
5. Use a field-provided fitting to temporarily reconnect the liquid line to the
indoor unit's liquid line orifice housing.
1. On fully cased coils, remove the coil access and plumbing panels.
2. Remove any shipping clamps from the liquid line and distributor
assembly.
3. Disconnect the equalizer line from the expansion valve equalizer
line fitting on the vapor line.
4. Remove the vapor line sensing bulb.
5. Disconnect the liquid line from the expansion valve at the liquid line
assembly.
6. Disconnect the expansion valve from the liquid line orifice housing.
Take care not to twist or damage distributor tubes during this
process.
7. Remove and discard expansion valve and the two Teflon
®
rings.
8. Use a field-provided fitting to temporarily reconnect the liquid line to
the indoor unit's liquid line orifice housing.
1. Set the recovery machine for liquid recovery and start the recovery
machine. Open the gauge set valves to allow the recovery
machine to pull a vacuum on the existing system line set and indoor
unit coil.
2. Position the cylinder of clean HCFC-22* for delivery of liquid
refrigerant and open its valve to allow liquid refrigerant to flow into
the system through the vapor line valve. Allow the refrigerant to
pass from the cylinder and through the line set and the indoor unit
coil before it enters the recovery machine.
3. After all of the liquid refrigerant has been recovered, switch the
recovery machine to vapor recovery so that all of the HCFC-22
vapor is recovered. Allow the recovery machine to pull the system
down to 0.
4. Close the valve on the inverted HCFC-22 cylinder and the gauge
set valves. Pump the remaining refrigerant out of the recovery
machine and turn the machine off.
*IMPORTANT - Clean refrigerant is any refrigerant in a system that has not had compressor burn out. If the system
has experienced burn out, it is recommended that the existing line set and indoor coil be replaced.
FIGURE 10