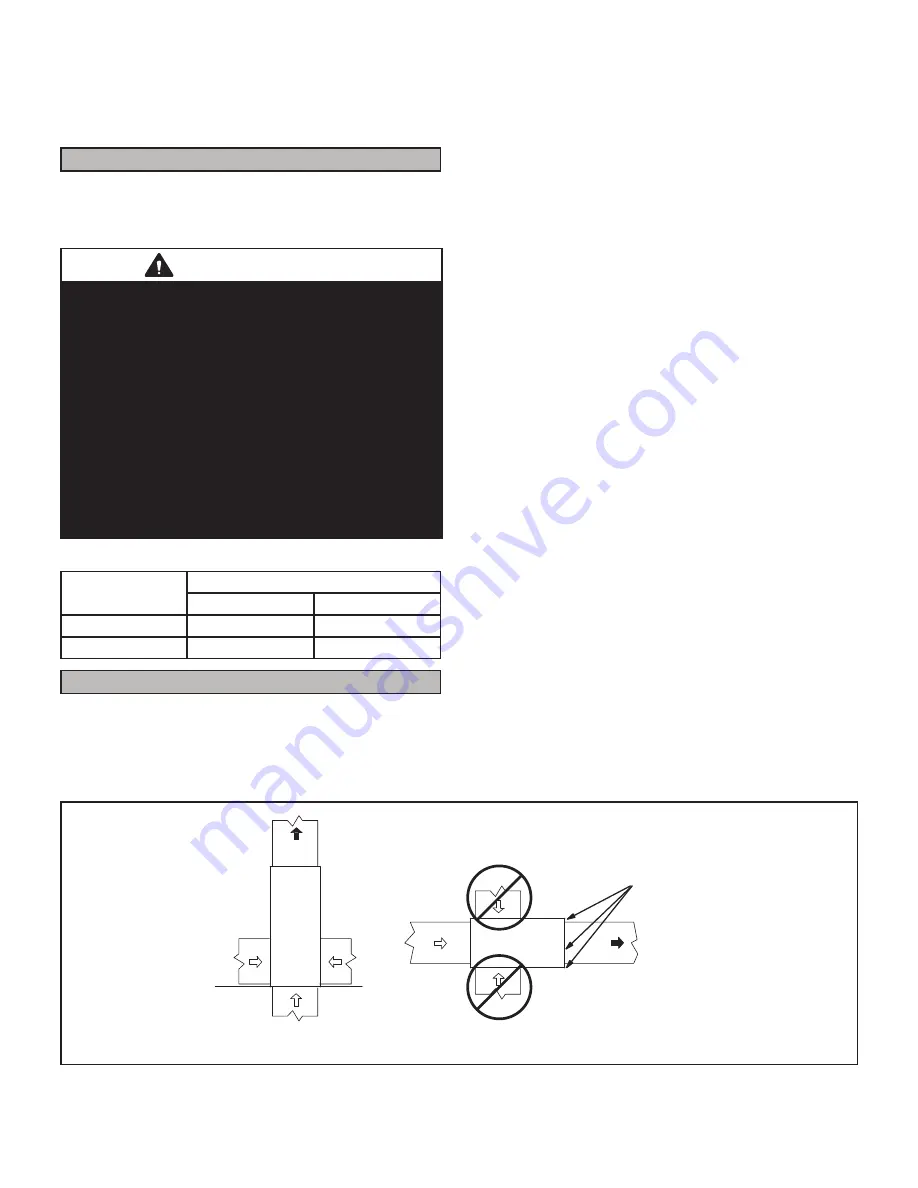
Page 10
Return Air -- Horizontal Applications
Return air may be brought in only through the end of a
furnace installed in the horizontal position. The furnace is
equipped with a removable bottom panel to facilitate in-
stallation. See figure 9.
Filters
This unit is not equipped with a filter or rack. A field-pro
-
vided high velocity rated filter is required for the unit to
operate properly. Table 1 lists recommended filter sizes. A
filter must be in place whenever the unit is operating.
IMPORTANT
If a highefficiency filter is being installed as part of this
system to ensure better indoor air quality, the filter must
be properly sized. Highefficiency filters have a higher
static pressure drop than standardefficiency glass/foam
filters. If the pressure drop is too great, system capacity
and performance may be reduced. The pressure drop
may also cause the limit to trip more frequently during
the winter and the indoor coil to freeze in the summer,
resulting in an increase in the number of service calls.
Before using any filter with this system, check the
specifications provided by the filter manufacturer against
the data given in the appropriate Lennox Product
Specifications bulletin. Additional information is provided
in Service and Application Note ACC002 (August 2000).
TABLE 1
Furnace
Cabinet Width
Filter Size
Side Return
Bottom Return
17-1/2”
16 X 25 X 1 (1)
16 X 25 X 1 (1)
21”
16 X 25 X 1 (1)
20 X 25 X 1 (1)
Duct System
Use industry-approved standards to size and install the
supply and return air duct system. Figure 14 shows the
correct supply and return duct installation. Refer to ACCA
Manual D. This will result in a quiet and low-static system
that has uniform air distribution.
NOTE -
This furnace is not certified for operation in heat
-
ing mode (indoor blower operating at selected heating
speed) with an external static pressure which exceeds 0.8
inches w.c. Operation at these conditions may result in
improper limit operation.
Supply Air Plenum
If the furnace is installed without a cooling coil, a remov-
able access panel should be installed in the supply air
duct. The access panel should be large enough to per-
mit inspection of the heat exchanger. The furnace access
panel must always be in place when the furnace is oper-
ating and it must not allow leaks. For horizontal units, in-
stall self tapping screws in the three evaporator coil screw
holes made for horizontal applications to seal the top cap
to the vestibule panel.
Return Air Plenum
NOTE - Return air must not be drawn from a room
where this furnace, or any other gas-fueled appliance
(i.e., water heater), or carbon monoxide-producing de-
vice (i.e., wood fireplace) is installed.
When return air is drawn from a room, a negative pressure
is created in the room. If a gas appliance is operating in
a room with negative pressure, the flue products can be
pulled back down the vent pipe and into the room. This
reverse flow of the flue gas may result in incomplete com
-
bustion and the formation of carbon monoxide gas. This
raw gas or toxic fumes might then be distributed through-
out the house by the furnace duct system.
Return air can be brought in through the bottom or either
side of the furnace (return air brought into either side of
furnace allowed only in upflow applications). If a furnace
with bottom return air is installed on a platform, make an
airtight seal between the bottom of the furnace and the
platform to ensure that the unit operates properly and
safely. Use fiberglass sealing strips, caulking, or equiva
-
lent sealing method between the plenum and the furnace
cabinet to ensure a tight seal. If a filter is installed, size the
return air duct to fit the filter frame.
HORIZONTAL UNIT
SUPPLY
AIR
SUPPLY
AIR
Install self tapping screws
to seal any potential air
leaks
UPFLOW UNIT
Figure 14
Summary of Contents for DAVE LENNOX SIGNATURE SL297UHNV
Page 39: ...Page 39 Figure 48...