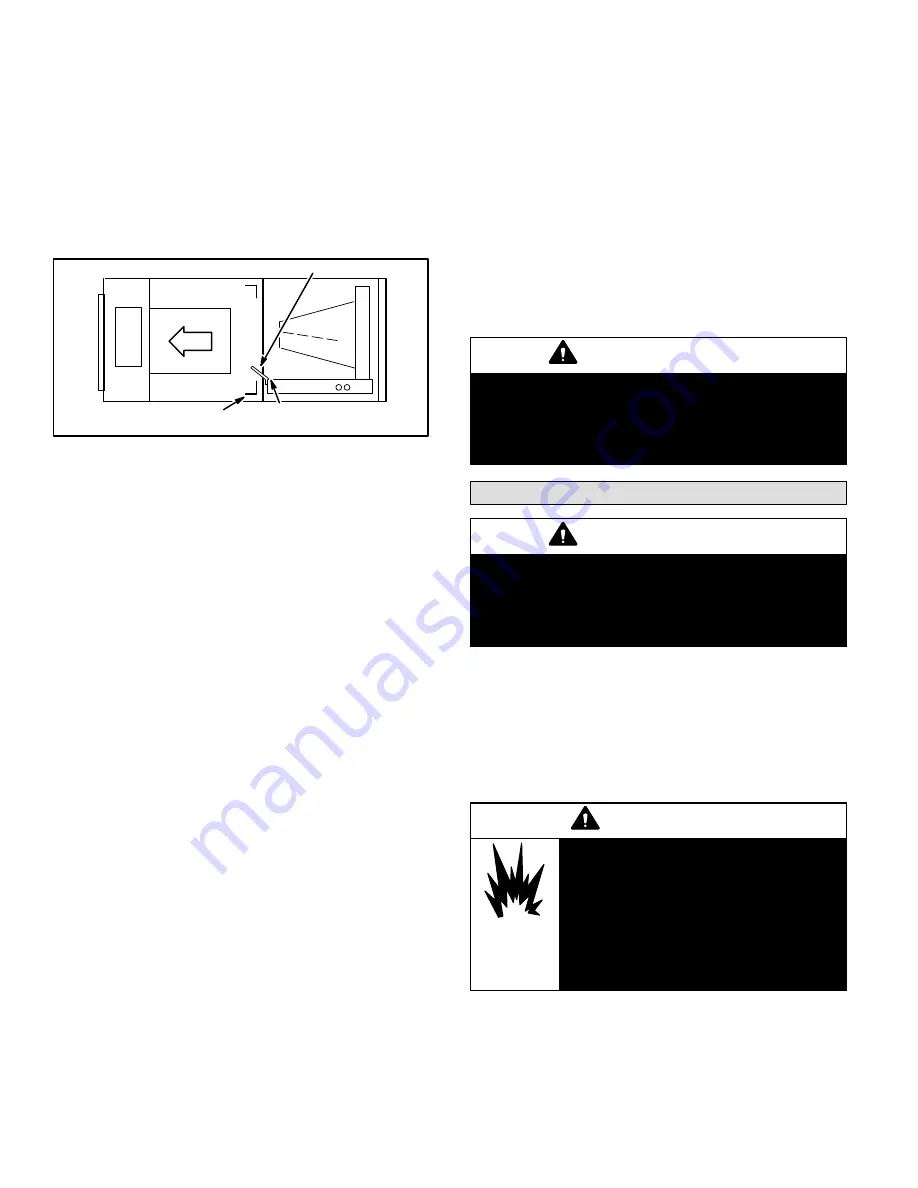
Page 6
506294−01
4. Rotate drain pan 180º front-to-back and install it on the
opposite side of the coil.
5. Remove screws from top cap. Remove horizontal drip
shield screw located in the center of the back coil end
seal as illustrated in figure 4 on page 5.
6. Rotate horizontal drip shield 180º front to back.
7. Remove plastic plug from left hole on coil front end
seal and reinstall plug in back hole. Reinstall horizontal
drip shield screw in front coil end seal. Drip shield
should drain downward into horizontal drain pan inside
coil.
HORIZONTAL DRIP SHIELD (−060 MODEL)
DOWN−FLOW
RAIL
FRONT EDGE OF HORIZONTAL
DRAIN PAN
Figure 5. Left−Hand Discharge Configuration
8. Rotate top cap 180º front-to-back and align with
unused screw holes. Holes must align with front and
back coil end plates. The top cap has a 45º bend on
one side and a 90º bend on the other.
The 90
º
bend
must be on the same side as the horizontal drain
pan
as illustrated in figure 4 on page 5.
NOTE − Be very careful when you reinstall the screws into
coil end plate engaging holes. Misaligned screws may
damage the coil.
9. From the up−flow position, flip cabinet 90º to the left
and set into place. Replace blower assembly. Secure
coil in place by bending down the tab on the cabinet
support rail as illustrated in figures 4 and 5.
10. Install the horizontal shield (−060 model) on the front
edge of the horizontal drain pan as illustrated in figure
5 on page 6.
NOTE − For horizontal applications in
high humidity
areas
, remove the down−flow rail closest to the drain pan.
To remove rail, remove screw from rail at back of unit and
at cabinet support rail. Remove down−flow rail then replace
screws. Also, seal around the exiting drain pipe, liquid and
suction lines to prevent infiltration of humid air.
11. Knock out drain seal plate from access door. Secure
plate to cabinet front flange with screw provided.
12. Flip access door and replace it on the unit.
13. Set unit so that it is sloped 1/4" toward the drain pan
end of the unit. Connect return and supply air plenums
as required using sheet metal screws.
14. If suspending the unit, it must be supported along the
entire length of the cabinet. If using chain or strap, use
a piece of angle iron or sheet metal attached to the unit
(either above or below) so that the full length of the
cabinet is supported. Use securing screws no longer
than 1/2" to avoid damage to coil or filter. as illustrated
in figure 3 on page 5. Connect return and supply air
plenums as required using sheet metal screws.
DOWN−FLOW APPLICATION
NOTE − If down−flow application is required, separately
order kit number 83M57 and install per kit’s instructions.
Also use metal or class I supply and return air plenums.
Use the installation instruction provided with the downflow
kit.
IMPORTANT
If electric heat section with circuit breakers
(ECB29/ECB31) is applied to down−flow and CBX27UH
units, the circuit breakers must be rotated 180° to the UP
position. See ECB29/ECB31 installation instructions for
more details.
Brazing Connections
IMPORTANT
To prevent the build up of high levels of nitrogen when
purging, be sure it is done in a well ventilated area. Purge
low pressure nitrogen (1 to 2 psig) through the refrigerant
piping during brazing. This will help to prevent oxidation
and the introduction of moisture into a system.
All coils are equipped with a factory−installed, internally
mounted check/expansion valve.
The air handler’s coil line sizes are listed in table 2. Use
Lennox L15 (sweat) series line sets (refer to the outdoor
unit Engineering Handbook for proper size, type and
application). For field−fabricated refrigerant lines, see the
piping section of the Lennox Unit Information Service
Manual.
WARNING
Danger of explosion!
Can cause equipment damage, injury, or
death.
When using a high pressure gas such as
dry nitrogen to pressurize a refrigeration or
air conditioning system, use a regulator
that can control the pressure down to 1 or
2 psig (6.9 to 13.8 kPa).