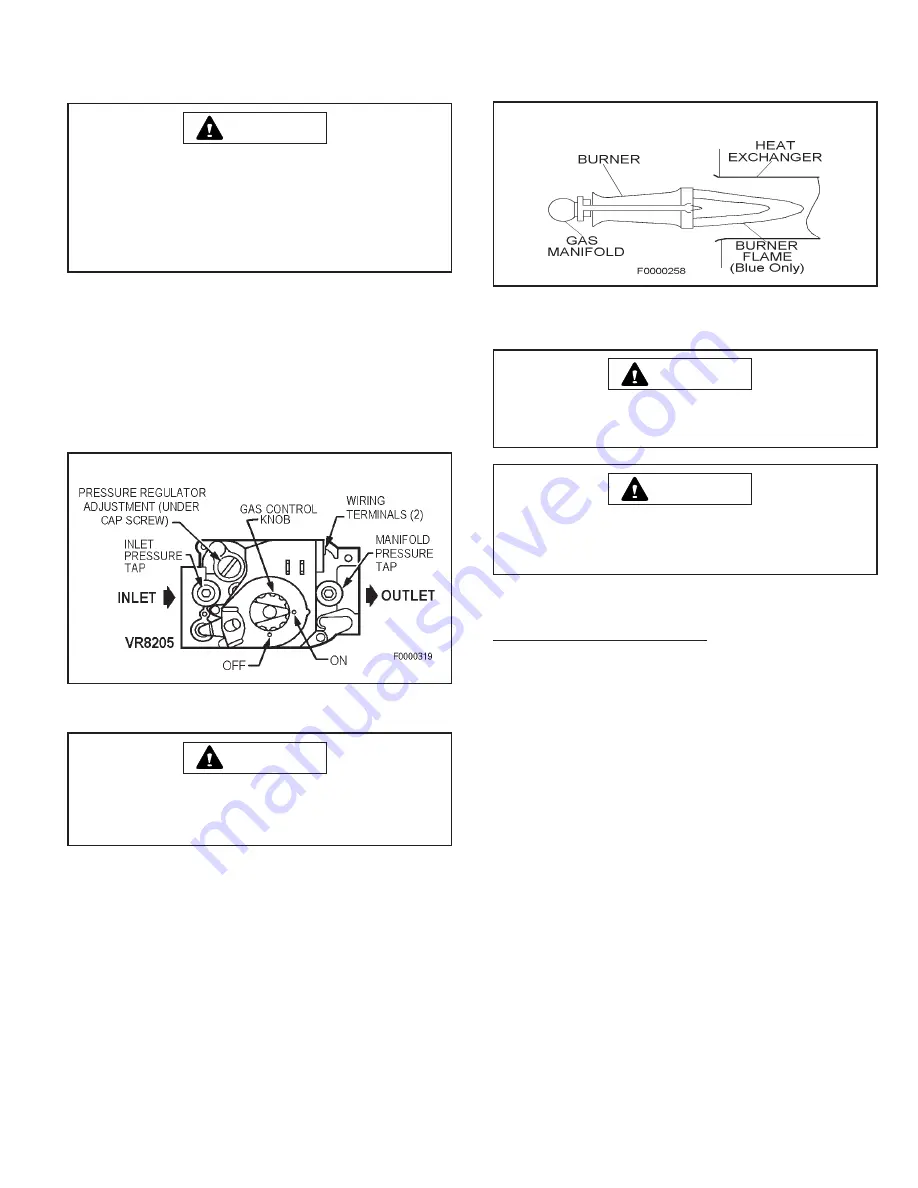
506307-01
Page 17 of 36
Issue 1207
STARTUP AND OPERATIONAL CHECKOUT
Do not use this furnace as a construction heater. Use of
this furnace as a construction heater exposes the furnace
to abnormal conditions, contaminated combustion air and
the lack of air filters. Failure to follow this warning can
lead to premature furnace failure and/or vent failure which
could result in a fire hazard and/or bodily harm.
WARNING
The automatic gas valve controls the flow of gas to the
main burners. The ignition system control switch built into
the automatic valve body has 2 positions: “OFF” and “ON”
(Figure 9). To shut off gas manually: Rotate switch from
“ON” to “OFF” position. When in “OFF” position, the main
burners are extinguished.
This furnace is equipped with an automatic spark ignition
control and does not require the manual lighting for furnace
operation.
GAS CONTROL DIAGRAM
Figure 9
After the ductwork connections have been made, gas
piping and electrical wiring completed and the furnace has
been properly vented, the unit should be started and adjusted
for proper operation. Check off the following steps as they
are completed.
1. Be sure all electrical power is OFF.
2. Check all wiring using proper wiring diagram on inside
of the control box cover.
3. Turn ON the electrical power.
4. Set the gas control knob in the “ON” position.
5. Set the thermostat above room temperaturae.
6. The ignitior will spark and the main burners will ignite.
Do not attempt to manually light the burners. Failure to
follow this warning can lead to electrical shock that could
result in bodily harm.
WARNING
TYPICAL FLAME APPEARANCE
(Main Burners)
7. Recheck for leaks in the manual shut off valve, gas control
valve and gas connections using a soap solution.
Never use an open flame when testing for gas leaks!
Use of an open flame could lead to a fire or explosion.
WARNING
Manifold Pressure Adjustment:
Turn OFF the gas and electrical before proceeding!
Remove the manifold pressure tap pipe plug from the gas
valve (Figure 9 outlet pressure tap) and install a pressure
tap and connect it to a manometer. Turn on the gas and
electrical supplies, then measure the manifold pressure
with
the furnace in operation.
Remove the cap to access the screw for input
adjustment (Figure 9 Pressure Regulator).
Turn regulator-
adjusting screw IN to increase pressure, OUT to
decrease pressure.
Replace the cap. Measure the
manifold pressure.
For natural gas, best results are obtained with a manifold
pressure of 3.2” to 3.5” w.c. For units that have been
converted to LP (Propane) gases, a manifold pressure of
10” w.c. is necessary. After proper adjustment, turn OFF
gas, replace manifold pressure tap pipe plug and turn ON
gas.
Many soaps used for leak testing are corrosive to certain
metals. Piping must be rinsed thoroughly with clean water
after leak check has been completed.
CAUTION
Summary of Contents for B050A3B
Page 3: ...506307 01 Page 3 of 36 Issue 1207...
Page 5: ...506307 01 Page 5 of 36 Issue 1207 FURNACE WIRING SPECIFICATIONS...
Page 23: ...506307 01 Page 23 of 36 Issue 1207 SEQUENCE OF OPERATION DIRECT IGNITION SYSTEM CONTROL...
Page 25: ...506307 01 Page 25 of 36 Issue 1207 WIRING DIAGRAM f0000321...