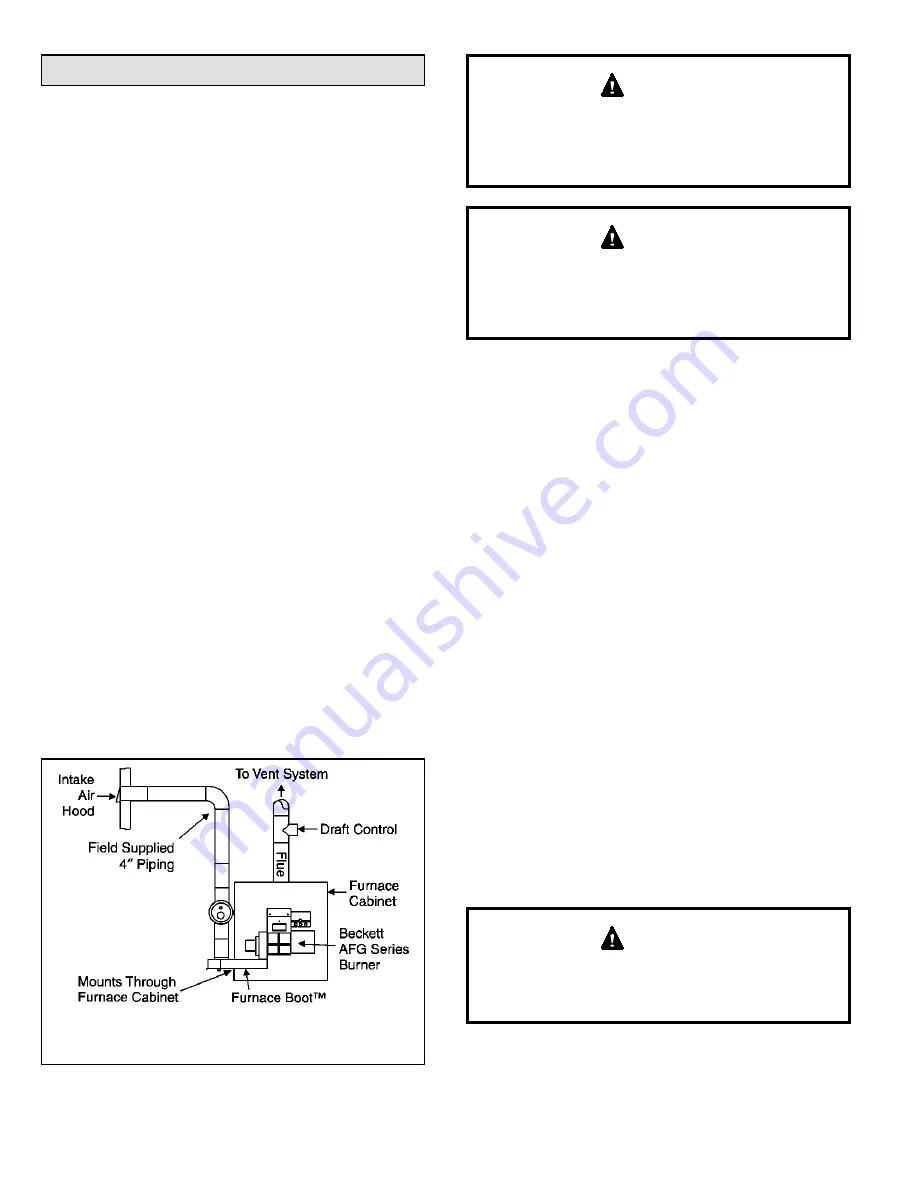
506794-01
Page 6 of 16
Issue 1243
Combustion and Ventilation Air
Adequate provisions for combustion air, ventilation of
furnace, and dilution of the gases must be made. When a
furnace is installed in an unconfined space in a building, it
can be assumed that infiltration will be sufficient to supply
the required air.
If the furnace is installed in a confined space and
combustion air is taken from the heated space, the supply
air and ventilating air must be through two permanent
openings of equal area. A confined space is “a space
whose volume is less than 50 cubic feet per 1000 btu per
hour of the combined input rating of all appliances installed
in that space.” One opening must be within 12” of the
ceiling and the other within 12” of the floor. Each opening
must have a minimum free area of at least 1 square inch
per 1000 btu per hour of total input rating of all appliances
with the space but not less than 100 square inches.
If the furnace is installed in a space within a building of
tight construction, air must be supplied from outdoors. In
this case, one opening shall be within 12” of the ceiling and
the other within 12” of the floor. If vertical combustion ducts
are run, each opening must have a free area of at least 1
square inch per 4000 btu per hour. If horizontal combustion
ducts are run, 1 square inch per 2000 btu per hour of the
total input of all appliances is required.
The furnace is designed to use air inside the dwelling
for combustion. If additional combustion air is required,
installing fresh air kit ABOOT571 allows air from outside
the dwelling to be brought in to the oil burner. This kit brings
air into the burner through air inlet ductwork run through
the furnace cabinet side panel and terminated outside the
dwelling (see Figure 5). The kit includes a vacuum relief
valve to guard against combustion problems associated
with directly connecting oil burners to the outside.
Figure 5. Fresh Air Kit ABOOT571 Installation
IMPORTANT
: No more than 10’ of vertical piping allowed without
weight support.
Combustion air openings in the front of the furnace
must be kept free of obstructions. Any obstruction will
cause improper burner operation and may result in a
fire hazard or injury.
WARNING
The barometric control shall be in the same atmospheric
pressure zone as the combustion air inlet to the furnace.
Deviation from this practice will cause improper burner
operation and may result in a fire hazard or injury.
WARNING
Circulating Air Supply
A return air duct system is recommended. Where there is
no complete return air duct system, a return connection
should be run full size to a location outside the confined
space and completely sealed so that no air from the
confined space can be circulated through the heating duct
system.
Outdoor Make Up Air
A minimum mixed return air temperature of 60 - 65°F
must be maintained for outdoor make up air to prevent
condensation and corrosion.
Venting
Chimney
Before installing the furnace, a thorough inspection of the
chimney should be made to determine whether repairs
are necessary and that the chimney is of the proper size
and constructed in accordance with the requirements
of the National Board of Fire Underwriters or Canadian
Standards Association. The smallest dimension of the
chimney should be at least equal to the diameter of the
flue pipe of the furnace. Be sure the chimney will produce
a steady draft sufficient to remove all the products of
combustion from the furnace. A fabricated vent system the
same size as the flue outlet of the furnace may also be
used. If a manufactured vent is used, it must be listed for
use with oil-fired equipment.
This furnace is certified for use with Type “L” vent, Type
“A”, and “factory-built” chimneys. “B” vent must not be
used with oil furnaces.
WARNING