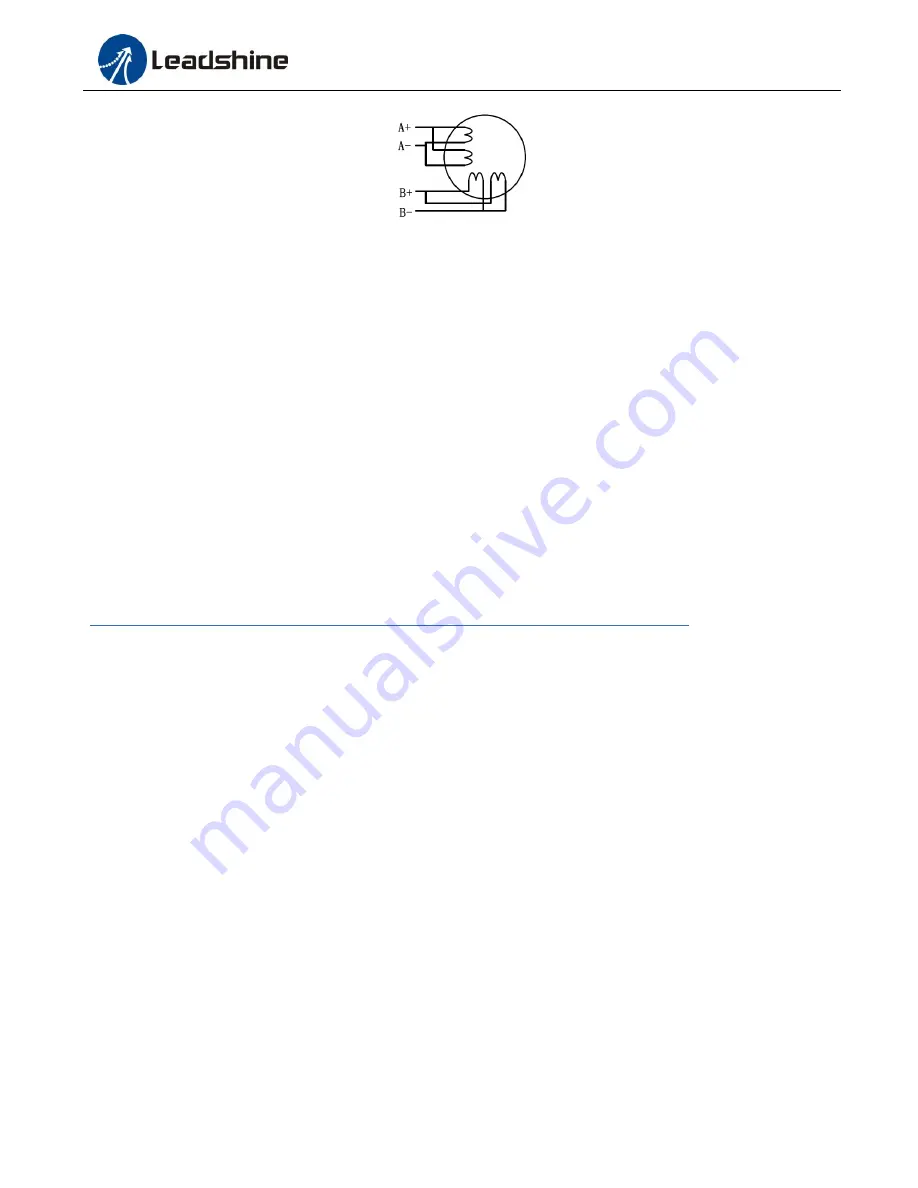
EM422S Digital Stepper Drive User Manual
Page | 7
P4
Figure 11
8-lead motor parallel connection
6. Power Supply Selection
EM422S is designed to power small and medium size stepping motors (frame sizes NEMA 8 to 17) made by Leadshine
or other motor manufacturers. To get optimal performances, it is important to select proper power supply type, voltage,
and supply output current. In general power supply voltage determines the high speed performance of a stepper motor,
while drive output current determines the driven motor torque output. Higher supply voltage can increases motor speed
torque performance, but at the same time result in more noise and motor heating. For low motor speed applications, it
is suggested to use lower supply voltage power supplies.
6.1 Regulated or Unregulated Power Supply
Both regulated and unregulated power supplies can be used to power an EM422S. Theoretically unregulated power
supplies are preferred due to their ability to withstand back EMF current surge and faster response for current change.
If you prefer to use a regulated power supply instead, it is suggested to choose one specially designed for stepper or
servo controls such as one Leadshine RPS series power supply
(http://www.leadshine.com/ProductSubType.aspx?subtype=regulated-switching-power-supplies
). In the case when
only general purpose switching power supplies are available, choose one with “OVERSIZED” current output rating
(for example, using a 4A power supply for 3A stepper motor) to avoid current clamp. On the other hand, if unregulated
supply is used, one may use a power supply of lower current rating than that of motor (typically 50%
~
70% of motor
phase current). The reason is that the drive only draws current from an unregulated power supply during the ON
duration of the PWM cycle, but not during the OFF duration.
6.2 Power Supply Sharing
Multiple EM422S drives can share the same power supply, if that power supply has enough capacity. To avoid cross
interference, connect each EM422S DIRECTLY to that shared power supply separately instead of connecting those
power connectors of drives in daisy-chain connection.
6.3 Selecting Supply Voltage
EM422S’s operating voltage is 18–36 VDC. Because of voltage increasing from potential power line voltage
fluctuation and back EMF voltage generated during motor deceleration, it is suggested to use a 24 VDC power supply.
7. DIP Switch Configurations
Each EM422S has two 2-bit DIP switch selectors. The first one is located on the side (DIP switch selector 1 in Figure 2)
and used to configure settings of micro step resolution, output current, and motor standstill current as shown below: