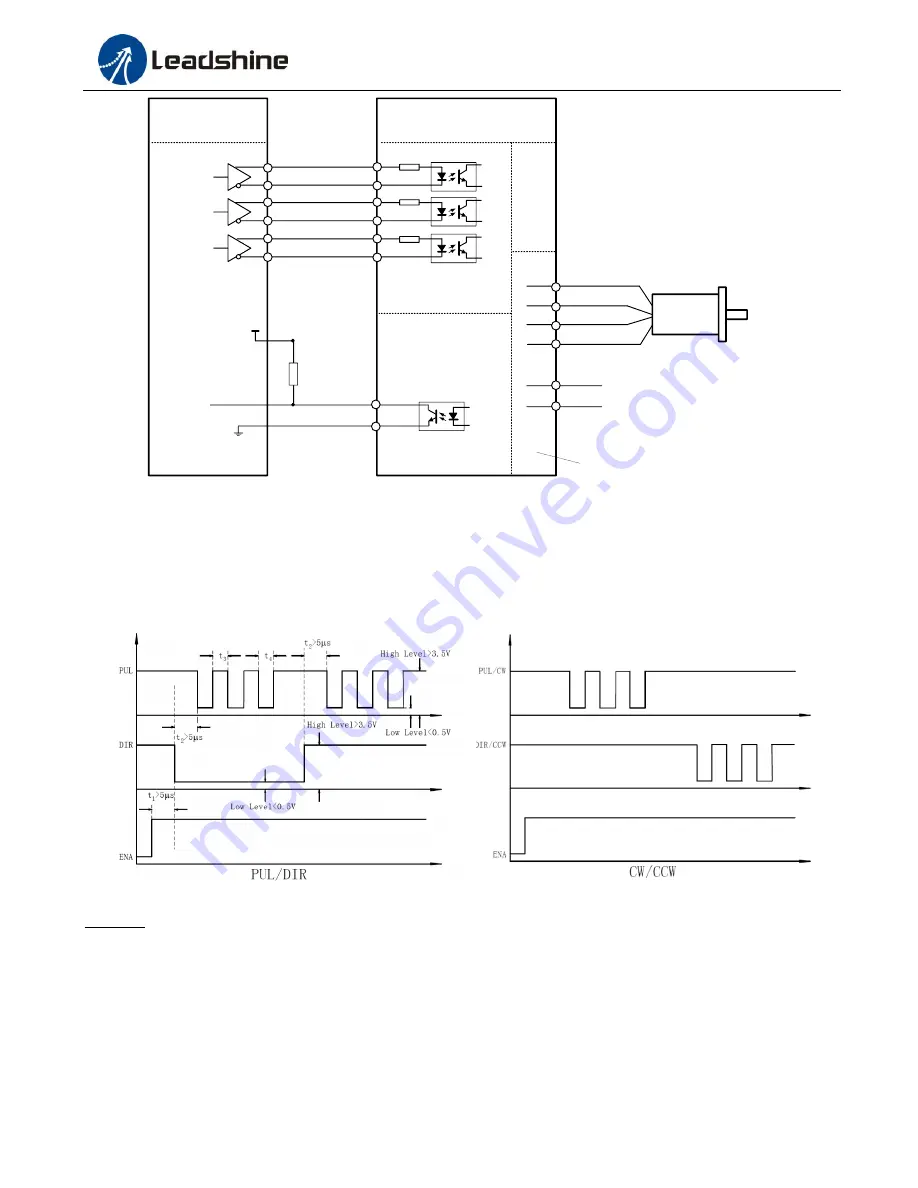
EM542S Digital Stepper Drive User Manual
Page | 11
GND
A+
A-
+Vdc
1
5
6
Power &
Motor Connector
Controller
Control Signal
Connector
4
PUL+
1
DIR+
3
PUL-
DIR-
2
4
ENA+
5
ENA-
6
Step
Direction
Enable
Fault
5-24VDC
ALM+
1
2
ALM-
Status Signal
Connector
24-48VDC recommended,
leaving rooms for voltage fluctuation
and back EMF of the motor
2
3
B+
B-
EM542S
Figure 12
Typical connection
10.
Sequence Chart of Control Signals
In order to avoid some fault operations and deviations, PUL, DIR and ENA should abide by some rules, shown as
following diagram:
Figure 13
Sequence chart of control signals
Remark:
a)
t1: ENA must be ahead of DIR by at least 5
s. Usually, ENA+ and ENA- are NC (not connected). See
“Connector P1 Configurations” for more information.
b)
t2: DIR must be ahead of PUL effective edge by 5
s to ensure correct direction;
c)
t3: Pulse width not less than 2.5
s;
d)
t4: Low level width not less than 2.5
s.