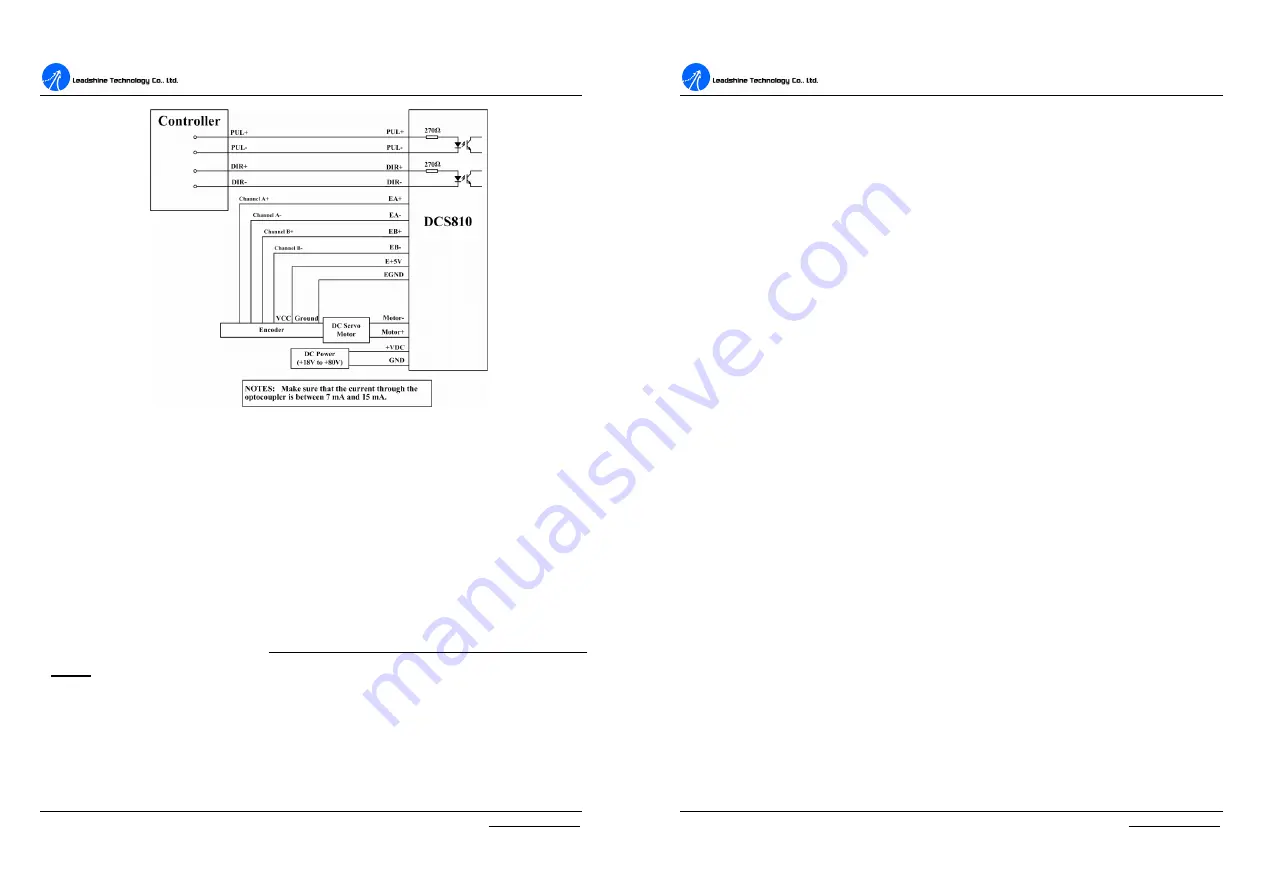
D
D
C
C
S
S
8
8
1
1
0
0
V
V
2
2
D
D
i
i
g
g
i
i
t
t
a
a
l
l
D
D
C
C
S
S
e
e
r
r
v
v
o
o
D
D
r
r
i
i
v
v
e
e
r
r
M
M
a
a
n
n
u
u
a
a
l
l
R
R
e
e
v
v
1
1
.
.
0
0
Tel: (86)755-26434369
10
Website: www.leadshine.com
Figure 3-10: Typical connection (Differential control signal and differential encoder.)
4. Servo Setup
Before you start the servo, you can follow the below steps.
Install Encoder
If your motor has no encoder, you must have an encoder (more than 200 lines)
properly mounted on the motor before you start. And please assemble the encoder
according to its factory manual.
Here, we recommend use differential encoder
again.
If you do have to use a single-ended encoder, please use shielded cables and
separate encoder signal cable from interference sources, such as motor wires and
power wires at least 5 cm.
D
D
C
C
S
S
8
8
1
1
0
0
V
V
2
2
D
D
i
i
g
g
i
i
t
t
a
a
l
l
D
D
C
C
S
S
e
e
r
r
v
v
o
o
D
D
r
r
i
i
v
v
e
e
r
r
M
M
a
a
n
n
u
u
a
a
l
l
R
R
e
e
v
v
1
1
.
.
0
0
Tel: (86)755-26434369
11
Website: www.leadshine.com
Prepare Power Supply
Regulated or Unregulated Power Supply
Both regulated and unregulated power supplies can be used to supply the driver.
However, unregulated power supplies are preferred due to their ability to withstand
current surge. If regulated power supplies (such as most switching supplies.) are
indeed used, it is important to have large current output rating to avoid problems
like current clamp, for example using 4A supply for 3A motor-driver operation. On
the other hand, if unregulated supply is used, one may use a power supply of lower
current rating than that of motor (typically 50%
~
70% of motor current). The reason
is that the driver draws current from the power supply capacitor of the unregulated
supply only during the ON duration of the PWM cycle, but not during the OFF
duration. Therefore, the average current withdrawn from power supply is
considerably less than motor current. For example, two 3A motors can be well
supplied by one power supply of 4A rating.
Selecting Supply Voltage
The DCS810V2 can actually operate within +18V to +80VDC, including power
input fluctuation and back EMF voltage generated by motor coils during motor shaft
deceleration. The rated voltage of the motor is an important parameter when
selecting supply voltage. Generally speaking, do not use a power supply voltage
more than 5 volts of the rated voltage of the motor. Higher voltage may cause bigger
motor vibration at lower speed, and it may also cause over-voltage protection or
even driver damage.
Prepare Controller
Prepare a controller with pulse and direction signals. However, the DCS810V2 has a
built-in motion controller for self-test and Servo Tuning. The built-in motion
controller can generate control signal with trapezoidal velocity profile.