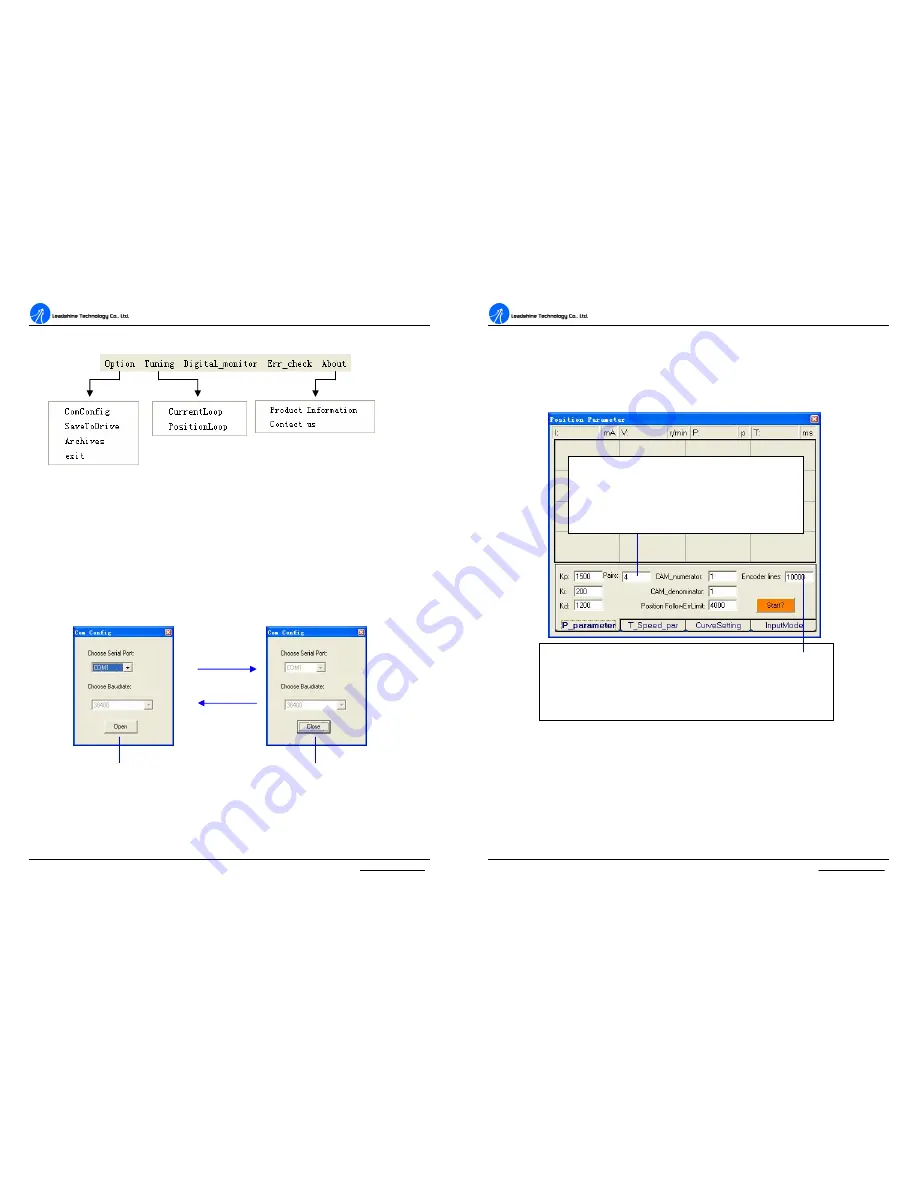
A
A
C
C
S
S
8
8
0
0
6
6
D
D
i
i
g
g
i
i
t
t
a
a
l
l
A
A
C
C
S
S
e
e
r
r
v
v
o
o
d
d
r
r
i
i
v
v
e
e
M
M
a
a
n
n
u
u
a
a
l
l
R
R
e
e
v
v
1
1
.
.
0
0
Tel: (86)755-26434369
26
Website: www.leadshine.com
2.
Menu Bar and Submenu
Figure 23: Menu of ProTuner for the ACS806
Communication Setup
Select
Option->ComConfig
, a dialogue window for setting the RS232
communication parameters would appear as figure 24. Select a correct port
according to the actual port used. Click the
‘
Open
’
button to establish
communication between the ACS806 and ProTuner. The caption of the button
should change to
‘
Close
’
if communication has been successfully established. Click
the button again to release the communication.
Figure 24: Establish and release series communication
Communication setup
Communication Release
A
A
C
C
S
S
8
8
0
0
6
6
D
D
i
i
g
g
i
i
t
t
a
a
l
l
A
A
C
C
S
S
e
e
r
r
v
v
o
o
d
d
r
r
i
i
v
v
e
e
M
M
a
a
n
n
u
u
a
a
l
l
R
R
e
e
v
v
1
1
.
.
0
0
Tel: (86)755-26434369
27
Website: www.leadshine.com
Software Configuration before Tuning
Some parameters must be configured before tuning the drive and the motor. Select
Tuning ->PositionLoop
to open the position-loop window. Set the parameters as
according to the description in figure 25.
Figure 25: Software configuration before Tuning
Current Loop Tuning
For most of the ACS606 drives which are shipped with Leadshine
’
s ACM series
servo motors, Leadshine will tune the current loop before sending them to customers.
Current Loop tuning is a reserved function, and when opening the current tuning
Set the Encoder Lines according to encoder specification. The input
number should be 4 times of the actual encoder lines/resolution since
the ACS806 decodes the encoder signals in X4 mode (ie. 10000 for
2500 lines encoder).
Set number of pole pairs of the servo motor according
to motor manual (For Leadshine BLM series DC
brushless servo motor, it is 2; For Leadshine ACM
series AC servo motor, it is 4. )