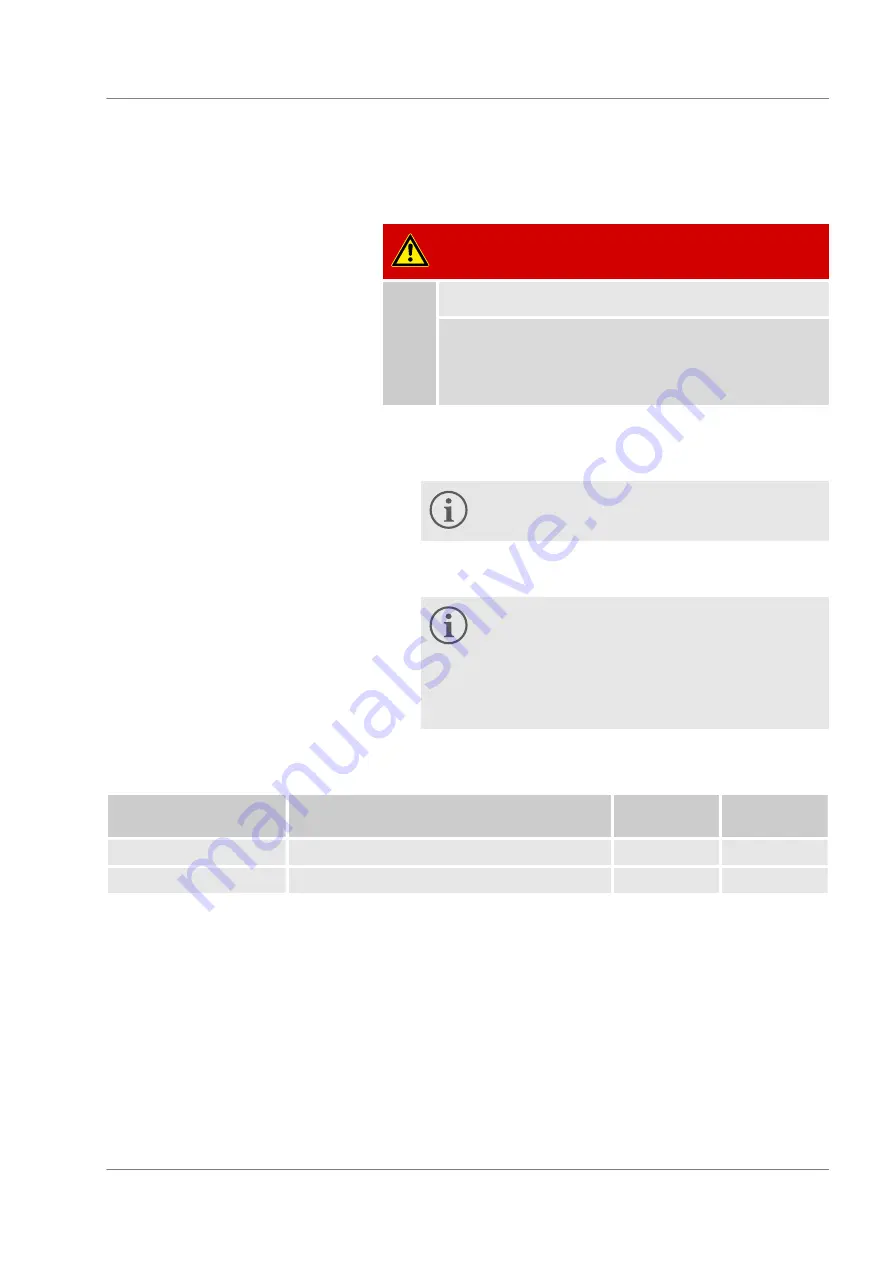
2
Unpacking
DANGER!
Transport damage
Electric shock
Inspect the device for transport damage before
commissioning.
Never put the device into operation if you have dis-
covered any transport damage.
Personnel:
Operating personnel
1.
Unpack the device.
Keep the original packaging of the device for later
transport.
2.
Inspect the device and the accessories immediately after
delivery for completeness and transport damage.
If there is unexpected damage to the device or
accessories, inform the carrier immediately so that
a damage report is produced and a check of the
transport damage can be made. Also inform
LAUDA Constant Temperature Equipment Service
immediately. Contact details can be found in
Chapter 12.3 ‘LAUDA contact’ on page 63
Accessories included as standard
Device type
Designation
Quantity
Catalogue
number
MC 600, MC 1200 (W)
¾" olive with ¾" union nut
2
EOA 004
All equipment
Operating manual
1
--
Unpacking
Microcool
11
Summary of Contents for MC 1200
Page 39: ...Fig 12 Menu Operation Microcool 39 ...
Page 56: ...Indication on the display Description NTC sensor break NTC short circuit Faults Microcool 56 ...
Page 67: ......
Page 68: ......
Page 70: ......
Page 71: ......