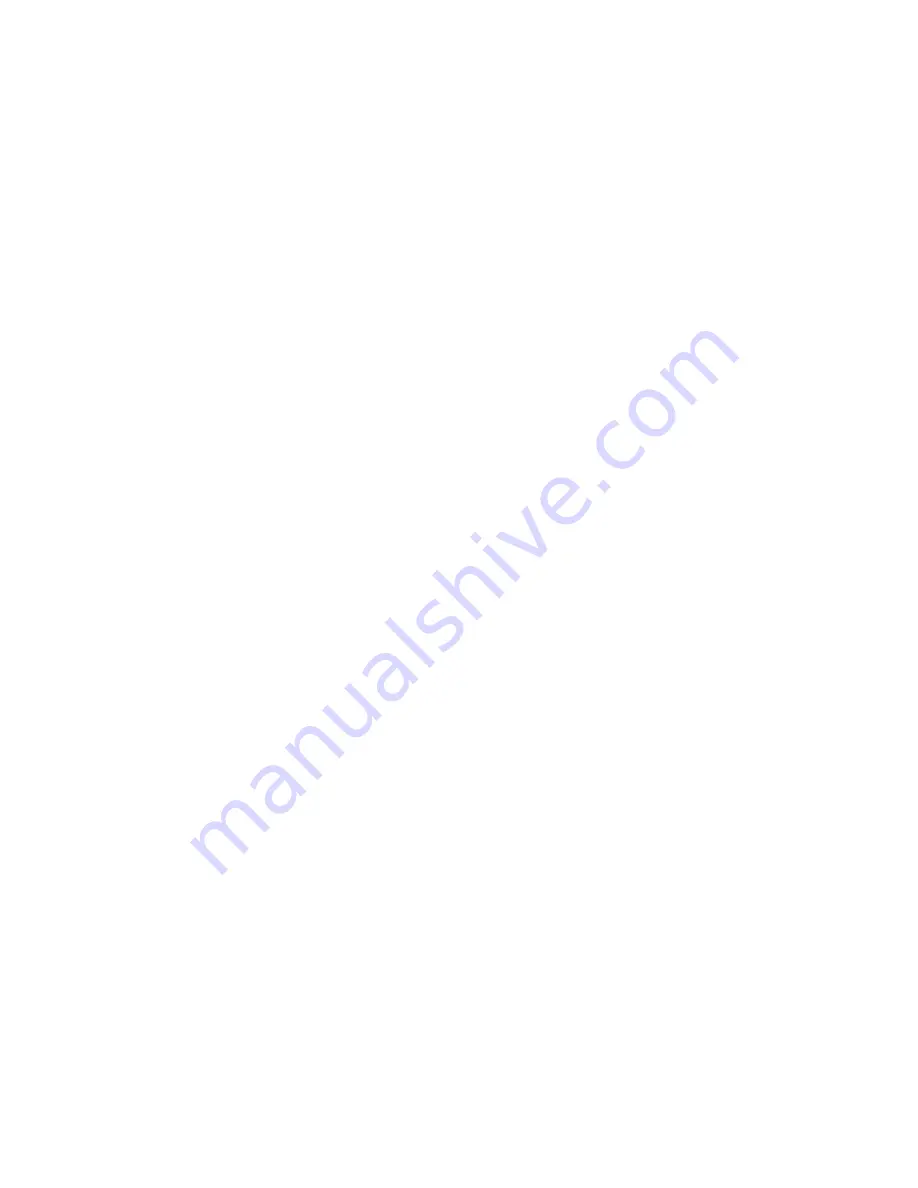
START UP
1. Check proper installation and settings of safety valve,
high limit cutout(s), low water cut-off and all other
control and safety devices. Adjust water temperature
set point on controller to desired value (less than 240
degrees F). If provided, adjust automatic cutout for
temperature setting approximately 10 degrees F above
set point of controller. Manual reset cutout should be
set approximately 10 degrees above automatic reset
controller, subject to maximum setting above.
2. Inspect all controls, wiring, and terminals for possible
damage during shipment or installation. Make sure
control circuit switch is in “OFF” position. Check all
internal wire terminations for tightness. Verify controller
and sequencer settings. Verify dip switch settings for
15 seconds “ON” time and 2 seconds “OFF” time,
delay, and number of stages required.
3. Open all gauge cocks. Purge piping system of all dirt,
sludge, and foreign material. Open vessel drain.
4. Close drain valve. Open all valves in supply and return.
5. Fill boiler and piping system with city water. Purge all
air from vessel and piping system through air vents.
6. As boiler fills check all piping and connections for
leaks. If necessary, correct immediately before
proceeding.
7. Energize circulating pump(s). Check pump rotation.
Change phases if necessary. Clean pump inlet
strainers.
8. When boiler is full and flow is established, turn on main
power disconnect switch.
9. Turn on control circuit switch. Pilot lights in control
panel will come on. Press low water reset button to
establish control after boiler is filled.
10. As water temperature increases, check pressure and
temperature gauges for proper indication. Open vent
cock again to purge air for the boiler.
11. After 8 – 24 hours of operation check system water Ph
with test kit or litmus paper. Ph should read 7.5 to 8.5.
If test is too acidic (less than 7.0) add neutralizer or
water treatment.
12.
Refer to operation manuals on components
included at the end of this section for sequencing
timing, temperature settings etc.
MAINTENANCE
Always disconnect main power to boiler before attempting to service equipment.
1. Routine
Maintenance
A. Make visual inspection of all controls.
B. Check for buzzing contactors in control panel;
clean or replace if necessary.
C. Observe pressure and temperature gauges for
normal operation.
D. Inspect for water leaks at piping connections and at
element bundle end.
2. Monthly
Maintenance
A. Inspect all wiring in control panel and check for
tightness.
B. Check all piping connections and fittings for
tightness.
C. Check boiler water Ph with test kit or litmus paper.
Ph should read 7.5 to 8.5.
3. Quarterly
Maintenance
A. Check low water cut-off for proper operation.
B. Check all other valves and controls for proper
operation.
C. Check heating element terminations for tightness.
4. Yearly
Maintenance
A. Shut down entire unit and conduct complete
inspection.
B. Access to inspect and clean vessel is obtained
through inspection opening (element flange).
C. Replace any defective elements (see next section).
D. Inspect heating elements for scale. If scale has
formed, clean with descaling compound such as
OAKITE DRYCID.
4