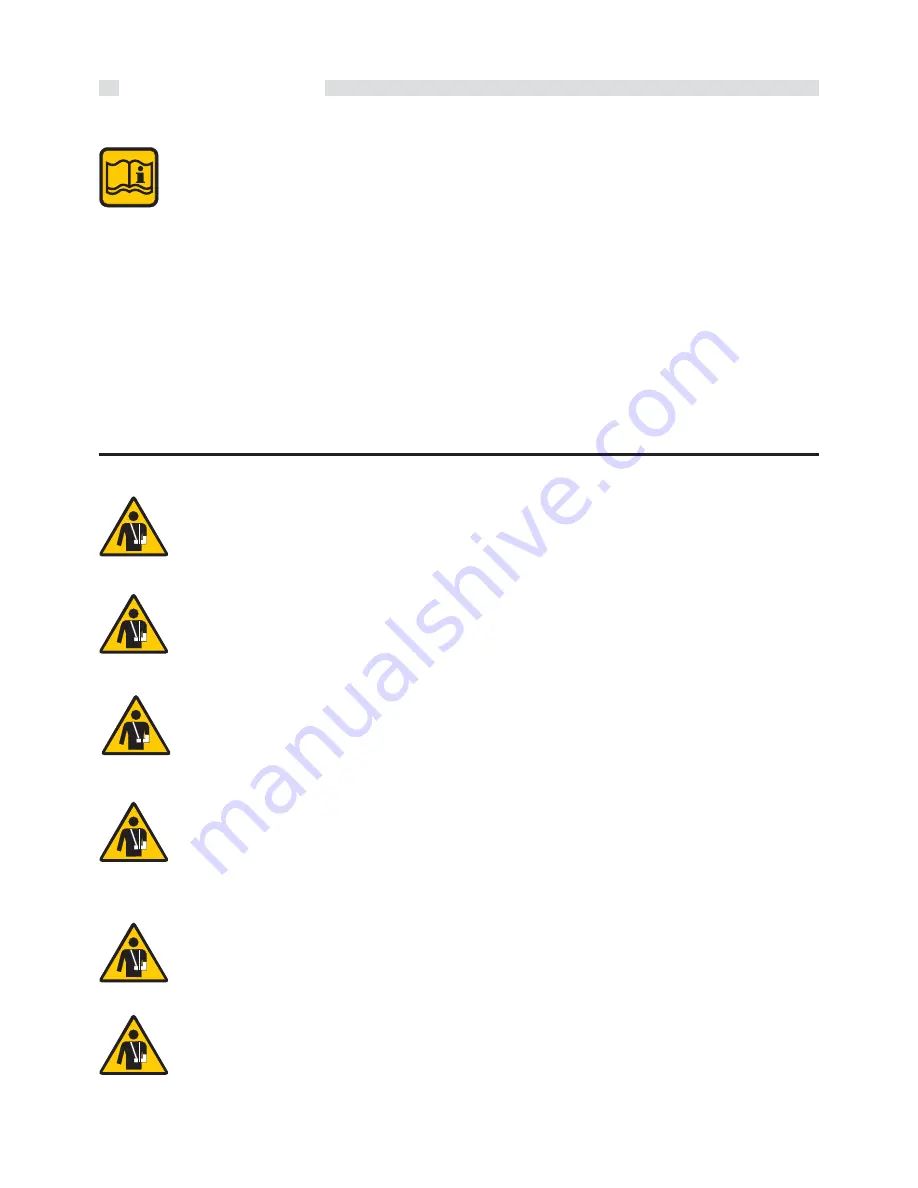
4
General Information
WARNING!
The device should not be used by people with reduced physical, mental and sensory, experience and
knowledge. These people must be well-informed and supervised during the work. Children must be
supervised so they do not play with the appliance.
WARNING!
The installation, adjustment, and servicing of this appliance must be carried out by a competent person and
installed in accordance with the current standards and regulations. Failure to correctly install this appliance
could cause injury to persons, animals or damage to property. The manufacturer shall not be held liable for
any injury and/or damage.
DANGER!
Servicing or repairs of the appliance must be carried out by LATTNER authorised service technicians; LATTNER
recommends drawing up a service contract. Bad or irregular servicing could compromise the safe operation
of the appliance, and could cause injury to persons, animals or damage to property for which LATTNER shall
not be held liable.
WARNING!
Modifications to parts connected to the appliance
Do not carry out any modifications to the following parts:
-
the boiler
-
to the gas, air, water supply pipes and electrical current
-
to the flue pipe, safety relief valve and its drainage pipe
-
to the constructive components which influence the appliance’s safe operation
WARNING!
When tightening or loosening the screw pipe connections, use only adequate fork spanners.
The improper use and/or the use of inadequate equipment can cause damages (for example water or gas
leakages).
WARNING!
Indications for appliances operating with propane gas
Ensure yourself that before installing the appliance the gas tank has been purged.
For a correct purging of the tank contact the liquid gas supplier or a competent person who has been legally
authorized.
If the tank has not been correctly purged problems could occur during ignition.
If this occurs contact the liquid gas tank’s supplier.
1.5 -
SAFETY WARNINGS
1.4 -
INFORMATION TO BE HANDED OVER TO THE USER
Go through the information in this manual with the owner/operator and make sure that he or she is familair
with all necessary operating instructions,
in particular:
•
Hand over these instructions to the end user, together with any other literature regarding this appliance,
placed inside the envelope contained in the packaging.
The user has to keep these documents in a safe
place in order to always have them at hand for future reference.
•
Inform the user on the importance of air vents and of the flue outlet system, stressing the fact that is absolutely
forbidden to make any alterations to the boiler.
•
Inform the user how to check the system’s water pressure as well as informing him how to restore the correct
pressure.
•
Explain the function of time and temperature controls, thermostats, heating controls and radiators, to ensure
the greatest possible fuel economy.
•
Remind the user that it is obligatory to carry out a comprehensive service annually and a combustion analysis
every two years (in compliance with the national law).
•
If the appliance is sold or transferred to another owner or if the present user moves home and leaves the
appliance installed, ensure yourself that the manual always follows the appliance so that it can be consulted
by the new owner and/or installer.
Failure to follow the instructions indicated in this guide, which is supplied with the boiler, could cause injury
to persons, animals or damage to property. The manufacturer shall not be held liable for any such injury and/
or damage.
Summary of Contents for Alkon 90
Page 34: ...34 Instructions for the installer ...
Page 49: ...49 Spare parts ...
Page 50: ......
Page 51: ......