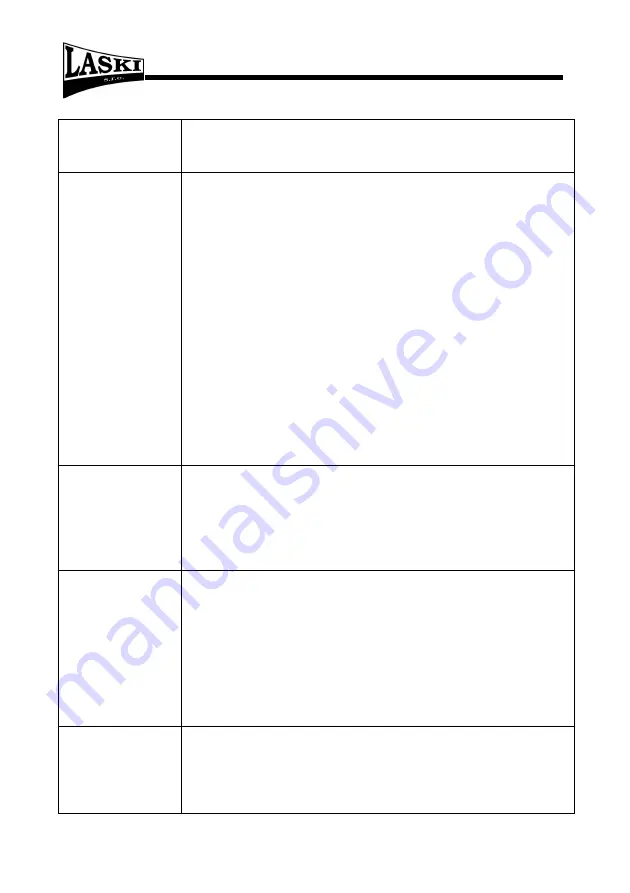
29
new oil of proper viscosity through the filler neck and then
screw up the filler plug.
In case of any failure in the lubrication system the engine stops
Air Filter
The air filter with two filter elements provides maximum
protection against mechanic impurities and keeps continuous
air flow into the fuel system. Remove the filter cap and
unscrew the locking nut and remove the filter element.
Check the air pre-cleaner every 25 working hrs as follows:
a)
Remove the pre-cleaner carefully from the paper element
and clean it in the warm water with a non-foamy
detergent.
b)
Rinse the element with the water, press the water out and
dry it up. Put the cleaned element into the body, tighten up
the nut and fit the cap again. In case of heavy fouling
check up the element more frequently.
Check up the paper element every 10 working hours. If
fouled, change the element immediately.
CAUTION! - Never oil the element and never clean it with
paraffin or similar detergents
Ignition
The electromagnetic ignition system requires no further
adjustment. Its spark plug, power cable and plug socket should
be checked every 100 hrs. This check consists in cleaning of
electrodes and setting of the spark gap to 1,00 mm. Spark plugs
should be changed every 300 hrs.
Cleaning of
Engine
Clean the engine according to its actual impurity grade by
means of the pressure air (pressure water).
CAUTION! When cleaning with pressure water, avoid its
penetration into the air intake and ignition systems.
Clean the engine also after every change of oil or air filter
element. Check up also bolted joints for tightening. Any repairs
of the engine should be done by an authorised Kohler/Honda
service only.
Starting
Equipment
This cutter is equipped with a mechanical cord starter. Check
up especially condition of the starting cord.
CAUTION! The starting winch includes also a preloaded
spring which may cause injury at unskilled handling
Summary of Contents for F-360 SW
Page 1: ...Orig version 02 2015 OPERATING INSTRUCTIONS...
Page 3: ...3...
Page 4: ...4...
Page 38: ...38 Service Report...
Page 39: ...39 Service Report...
Page 40: ...40 Service Report...