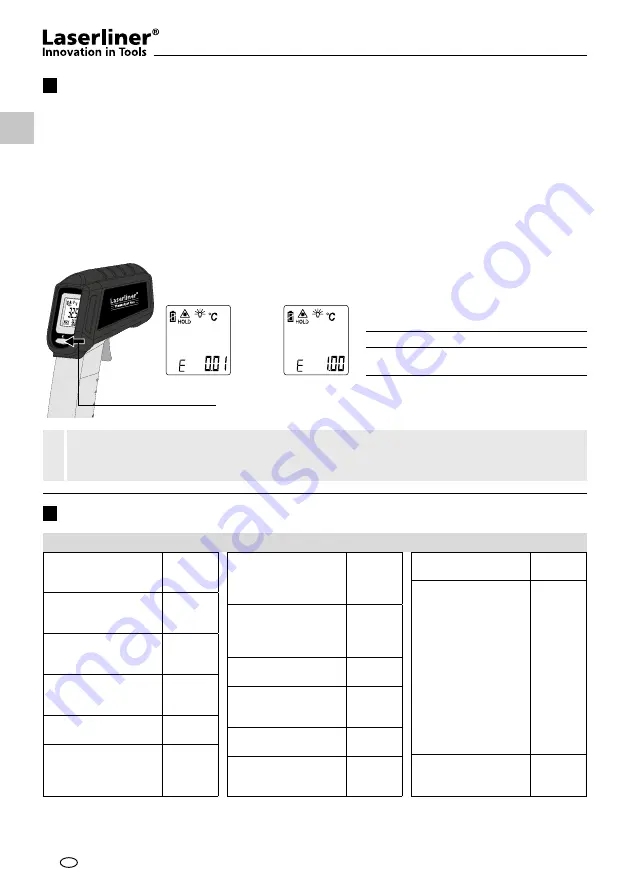
5
6
...
E 0.01...1.00
08
GB
Alloy A3003
Oxidised
Roughened
0.3
0.1 - 0.3
Aluminium
Oxidised
Polished
0.2 - 0.4
0.04 - 0.06
Brass
Polished
Oxidised
0.3
0.5
Copper
Oxidised
Elect. terminal strips
0.4 - 0.8
0.6
Haynes
Metal alloy
0.3 - 0.8
Inconel
Oxidised
Sandblasted
Electropolished
0.7 - 0.95
0.3 - 0.6
0.15
Iron
Oxidised
With rust
With red rust
0.5 - 0.9
0.5 - 0.7
0.61 - 0.85
Iron, cast
Oxidised
Non-oxidised
Molten mass
0.6 - 0.95
0.2
0.2 - 0.3
Iron, forged
Matt
0.9
Lead
Rough
Oxidised
0.4
0.2 - 0.6
Molybdenum
Oxidised
0.2 - 0.6
Nickel
Oxidised
0.2 - 0.6
Platinum
Black
0.9
Steel
Cold rolled
Ground plate
Polished plate
Alloy (8% nickel,
18% chromium)
Galvanised
Oxidised
Heavily oxidised
Freshly rolled
Rough, flat surface
Rusty, red
Sheet, nickel plated
Sheet, rolled
0.7 - 0.9
0.4 - 0.6
0.1
0.35
0.28
0.80
0.88
0.24
0.95 - 0.98
0.69
0.11
0.56
Zinc
Oxidised
0.1
Setting the emission coefficient
Table of emission coefficients
A built-in sensor head detects the material/surface-specific infrared rays emitted by every object. The level of
these emissions is determined by the material‘s emission coefficient (0.01 to 1.00). After switching on for the
first time, the device is preset to an emissivity coefficient of 0.95, which is suitable for most organic materials
as well as plastics, ceramics, wood, rubber and stone. For materials with different emissivity coefficients,
please refer to the table under point 6.
Unknown emission coefficient:
Apply masking tape or black matt paint to the surface of the area whose temperature you wish to measure.
Wait until the tape/paint has heated up. The temperature of the surface can then be measured with an
emission coefficient of 0.95.
Button pressed briefly: Value +0.01
Keep button pressed:
Value runs through 0.01 … 1.00
Metals
The emissivity coefficient last selected is set after the device is switched on. Check the emissivity
coefficient setting before each measurement.
!
Summary of Contents for 082.042A
Page 90: ...90 ...
Page 91: ...ThermoSpot Plus 91 ...