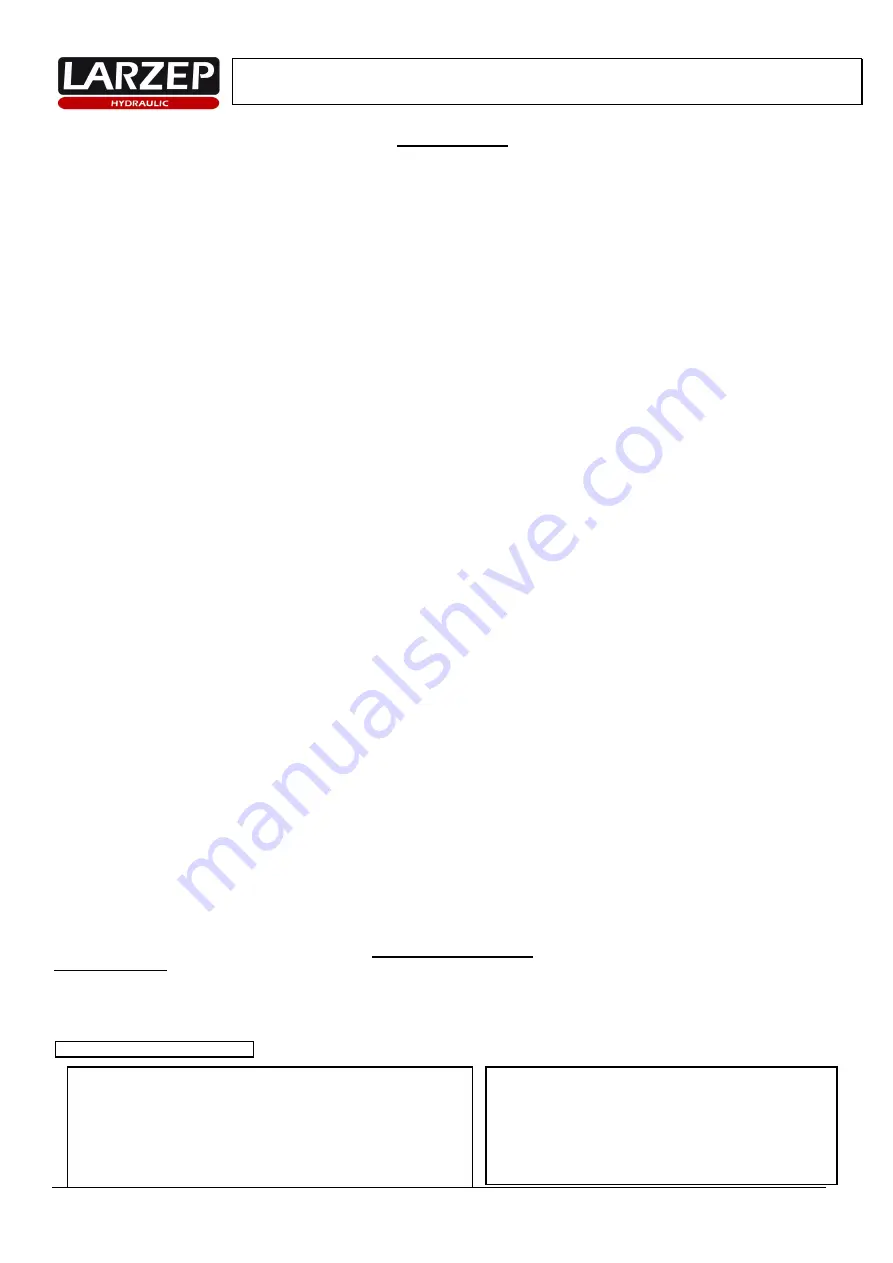
3
Instruction Manual
Modular Hand Pump “WI 105”
4. START UP.
This is a modular pump, it is supplied with a lever to pump the oil and its use is very simple.
These pumps are lightweight, easy to fix by the base so, we can use them with different sizes of tanks.
To start operating with the pump, we only have to place the lever in the upper of the pump and pump several times until reach the wished stroke of the hydraulic
element in the system.
CYLINDER-HAND PUMP INSTRUCTIONS
Unpack and visually check all the components, making sure that there are no oil leaks, loose or damaged plugs, damaged threads, etc. Never use components
that are damaged or appear to be in poor condition.
Assemble the device in accordance with the instructions given in the diagram, first checking that you have all the necessary material.
Check the correct installation and perfect functioning of the device with a load, in accordance with the procedure outlined below:
SINGLE ACTION INSTALLATION
Release the pump drive lever by removing the hook from the lever-holder housing.
Pump manually with the drive screw open (rotate a few times to loosen) in order to fill the pump’s internal circuit with oil.
Close the drive screw by turning clockwise manually. You do not need to close too tightly.
Now pump using the drive lever. First, fill the hose with oil. The number of thrusts required will depend on the length of the hose and the flow supplied by the
pump piston. With single-speed pumps, the flow will remain the same at all times, regardless of the load or pressure. With two-speed pumps, the large piston
will be activated during the load-free feed movement, and when the device comes into contact with the load, an internal large piston relief value will be
automatically triggered and only the oil supplied by the small piston will be available up to 700 kg/cm”, which is the maximum pressure for the device.
Once the hose is full of oil, the cylinder piston will start to advance.
If the cylinder has a mechanical limit switch capable of withstanding the maximum device pressure, continue pumping until the limit switch is reached.
If any control elements (pressure gauges) are available, you will be able to see how the pressure increases along with the effort required moving the lever.
Keep pumping until you obtain the maximum pressure (700 kg/cm”). In this way you will be able to check the correct functioning of the internal safety valve
and the absence of oil leaks in the installation.
Maintain pressure in the installation for a short period of time (1 minute) without pumping, in order to check the correct functioning of the pump’s check valve.
Gently open the pump’s drive screw (by turning anticlockwise) in order to protect the fall of the pressure gauge needle. Do not force the drive screw open. The
cylinder will not move back more quickly because the screw is looser. A couple of turns will be sufficient.
If the cylinder has a return spring (SM, SMP, SMX, SH, TE, T, SMA, SHA, CY, KC) the piston will move back automatically. The return speed may be slow
in some applications. In this case, we recommend the use of double effect cylinders. In the case of load return cylinders(SP,SX,SL,SS,ST,STX), you will need
to push the piston back using more or less force, depending on the size and position of the cylinder.
In cylinders without a mechanical limit switch (SS, ST, STX) this type of test cannot be carried out. If you do not have a test bench, you will have to test the
installation using the actual load in the application. This operation should be carried out with extreme care by experienced personnel and maximum safety
measures should be applied.
Repeat the process as many times as necessary until you are comfortable handling the device.
If using close or check valves, or working with various cylinders via flow distributors, remember to take into consideration the effect these accessories may
have on the functioning of the device, and establish an operating procedure in order to avoid unwanted effects.
DOUBLE ACTION INSTALLATION
The connection of the quick plugs is, if possible, even more important here, since a bad connection will not only prevent the device from functioning, it may
also generate excessive pressure build-up that may cause the cylinder to break. Take note of which hose connects to the thrust chamber and which to the return
chamber.
All double action LARZEP cylinders are equipped with a mechanical limit switch capable of withstanding the nominal pressure. You can therefore carry out
the test described in the previous section. If you are working with another type of cylinder and are not 100% sure, do not carry out this test.
Release the pump drive lever by removing the hook from the lever-holder housing.
Turn the control of the distributing valve to the central position and pump and few times to fill the internal channels with oil.
Turn the lever to one side and pump. Oil will flow through the hose connected to the side to which the valve lever is rotated. If this hose is connected to the
cylinder’s thrust chamber, the piston will move forward. The oil in the return chamber will flow freely through the other hose to the pump tank. Until the
moment the cylinder connects with the load, flow is supplied by both the large and small pistons.
Continue pumping until you reach the limit switch. At this moment an internal large piston relief value will be triggered, and only the oil supplied by the small
piston will be available. Subject the installation to pressure to check for leaks.
Stop pumping and check (preferably using a pressure gauge) that the installation maintains the pressure level.
Turn the valve lever to the other side and pump. Oil will flow to the return chamber and the piston will move back. The oil in the thrust chamber will flow
freely back to the tank.
Repeat the process as many times as necessary until you are comfortable handling the device.
If using close or check valves, or working with various cylinders via flow distributors, remember to take into consideration the effect these accessories may
have on the functioning of the device, and establish an operating procedure in order to avoid unwanted effects.
5. MAINTENANCE.
Checking the oil level.
With the pump in vertical position (base downwards), unscrew or pry off the plug. Check the level on the dip stick.
This check must be carried out with the cylinder fully retracted. Excessive amount of oil in the tank will lead to internal pressures which will hamper the
function of the pump.
Filter the oil before filling up the pump.
Once the equipment is being used the areas exposed to wear and oxidation must be cleaned and greased.
BREAK DOWNS AND
REPARATIONS
THE CYLINDER DOESN´T AVANCE
Lack of oil in the tank ____
Check the oil.
Couplers not fully inserted ____
Check couplers.
Admission ball valve failure (19) ____
Clean the seat and
replace the ball.
Closing ball valve failure (22) ____
Clean the seat and
replace the ball.
THE CYLINDER DOESN´T REACH WORKING PRESSURE
.
Relief valve decalibrated (12) ____
Calibrate the valve.
Retention ball valve failure (20) ____
Clean the seat and replace the ball.
Closing ball valve failure (22) ____
Clean the seat and replace the ball.
Pressure seal damaged (26) ____
Replace the seal.
Cylinder pressure seal damaged (see cylinder) ____
Replace the seal.
THE CYLINDER DOES NOT RETRACT
Too much oil in the tank ____
Check the level.