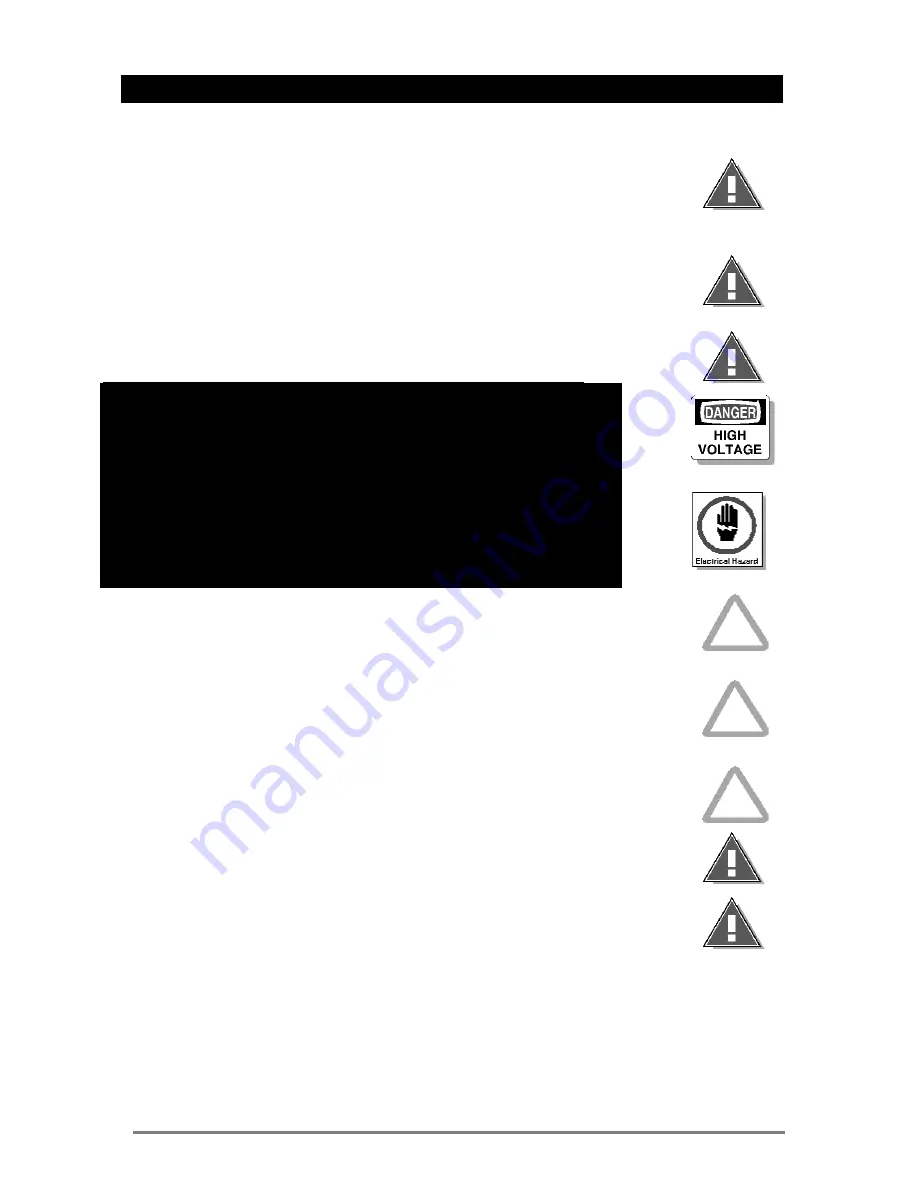
4
IMPORTANT READ
FIRST
IMPORTANT
CAUTION:
EACH UNIT IS EXTREMELY HEAVY. FOR SAFE
HANDLING, INSTALLER SHOULD OBTAIN HELP AS
NEEDED, OR EMPLOY APPROPRIATE MATERIALS
HANDLING EQUIPMENT (SUCH AS A FORKLIFT,
DOLLY, OR PALLET JACK) TO REMOVE THE UNIT
FROM THE SKID AND MOVE IT TO THE PLACE OF
INSTALLATION.
CAUTION:
ANY STAND, COUNTER OR OTHER DEVICE ON
WHICH THE MELTER WILL BE LOCATED MUST BE
DESIGNED TO SUPPORT THE WEIGHT OF THE
MELTER.
CAUTION:
SHIPPING STRAPS ARE UNDER TENSION AND CAN
SNAP BACK WHEN CUT.
DANGER:
THIS APPLIANCE MUST BE GROUNDED AT THE
TERMINAL PROVIDED. FAILURE TO GROUND THE
APPLIANCE COULD RESULT IN ELECTROCUTION
AND DEATH.
WARNING:
INSTALLATION OF THE UNIT MUST BE DONE BY
PERSONNEL QUALIFIED TO WORK WITH
ELECTRICITY AND PLUMBING. IMPROPER
INSTALLATION CAN CAUSE INJURY TO
PERSONNEL AND/OR DAMAGE TO EQUIPMENT.
UNIT MUST BE INSTALLED IN ACCORDANCE WITH
ALL APPLICABLE CODES.
NOTICE:
The data plate is located on the left side of unit
towards the front. The melter voltage, wattage, serial
number, wire size, and clearance specifications are
on the data plate. This information should be
carefully read and understood before proceeding
with the installation.
NOTICE:
The electric cheese melter must be installed more
than 12 inches above any cooking surface and never
above any open burners or charbroilers.
NOTICE:
The installation of any components such as a vent
hood, grease extractors, fire extinguisher systems,
must conform to their applicable National, State and
locally recognized installation standards.
NOTICE:
During the first few hours of operation you may
notice a small amount of smoke coming off the
melter, and a faint odor from the smoke. This is
normal for a new melter and will disappear after the
first few hours of use.
CAUTION:
ALWAYS KEEP THE AREA NEAR THE APPLIANCE
FREE FROM COMBUSTIBLE MATERIALS.
CAUTION:
KEEP FLOOR IN FRONT OF EQUIPMENT CLEAN
AND DRY. IF SPILLS OCCUR, CLEAN IMMEDIATELY,
TO AVOID THE DANGER OF SLIPS OR FALLS.