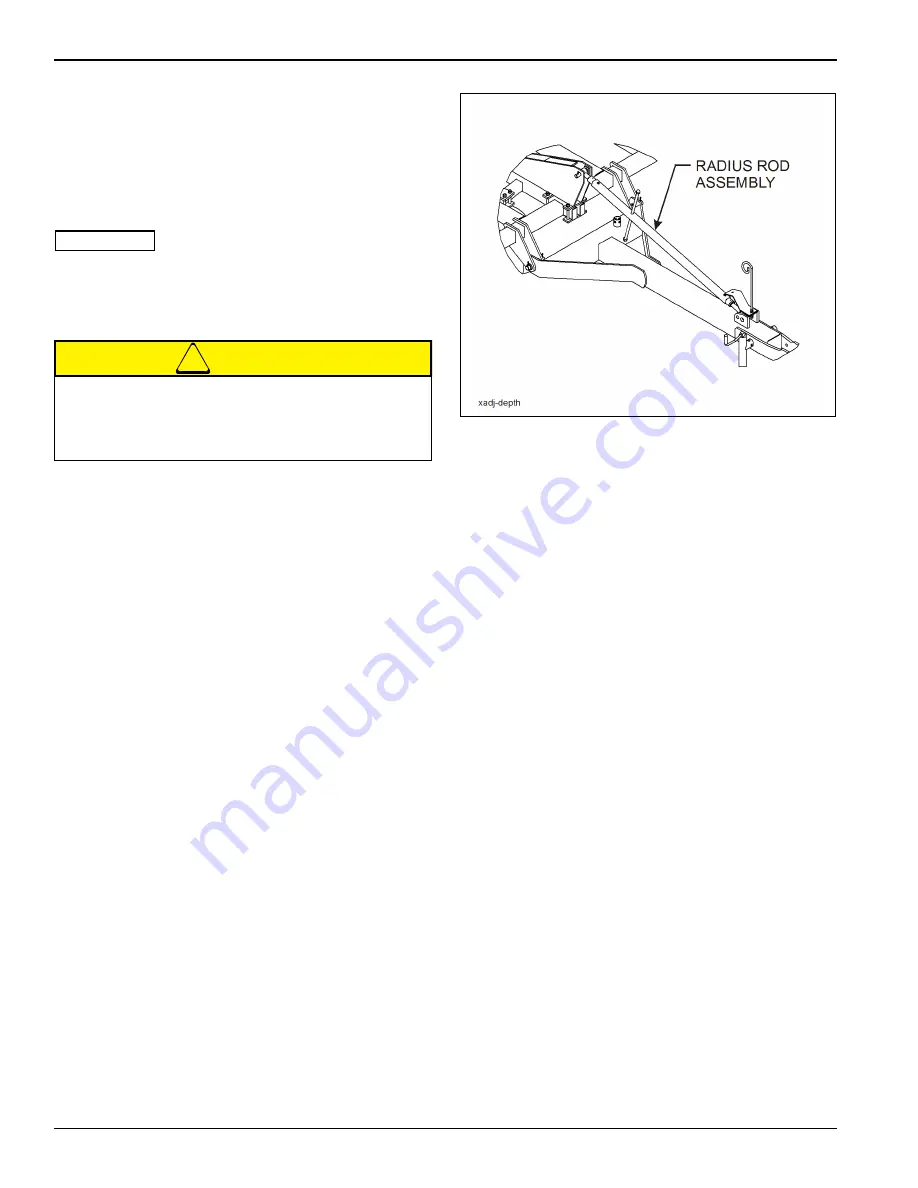
4-4
F-143-0211 Edition
OPERATION AND MAINTENANCE
Field Operation
1.
Raise the unit to take the weight off of the transport
locks. Remove the transport locks from the lift
cylinders (on the main frame only)
2.
Unfold the wings and extend the fold cylinders
completely
IMPORTANT
When folding or unfolding wings, operate tractor
engine at a fast idle on 30’, 35’, 40’ units, and hold
hydraulic valve on tractor open to assure smooth
operation.
CAUTION
3.
Check the front to rear leveling of the frame. Adjust
radius rod until frame is level at working depth and all
sections of the machine are cutting at the same
depth
Figure 4-3: Adjusting Unit Working Depth
Drive at reasonable speeds to insure your safety.
Slow down before making sharp turns or using
the brakes. Drive slowly over rough ground, side
hills, and around curves to avoid tipping.
Summary of Contents for Wing Tilloll 876 Series
Page 2: ......
Page 16: ...2 10 F 143 0211 Edition STANDARD SPECIFICATIONS ...
Page 18: ...3 2 F 143 0211 Edition ASSEMBLY INSTRUCTIONS Figure 3 1 Frame Assembly ...
Page 19: ...ASSEMBLY INSTRUCTIONS 3 3 Figure 3 2 Wing Assembly 876 30 876 35 Models ...
Page 22: ...3 6 F 143 0211 Edition ASSEMBLY INSTRUCTIONS Figure 3 4 Shank Clamp and Sweep Assembly ...
Page 26: ...3 10 F 143 0211 Edition ASSEMBLY INSTRUCTIONS Figure 3 7 Hydraulic Lift Assembly 876 40 H ...
Page 28: ...3 12 F 143 0211 Edition ASSEMBLY INSTRUCTIONS Figure 3 8 Hydraulic Fold Assembly ...
Page 32: ...3 16 F 143 0211 Edition ASSEMBLY INSTRUCTIONS Figure 3 10 Center Reel Assembly Installation ...
Page 33: ...ASSEMBLY INSTRUCTIONS 3 17 Figure 3 11 Outer Reel Assembly Installation ...
Page 36: ...3 20 F 143 0211 Edition ASSEMBLY INSTRUCTIONS Figure 3 12 Harrow Assembly Installation ...
Page 38: ...3 22 F 143 0211 Edition ASSEMBLY INSTRUCTIONS Figure 3 13 Pull Hitch Installation ...
Page 40: ...3 24 F 143 0211 Edition ASSEMBLY INSTRUCTIONS Figure 3 14 Electrical Installation ...
Page 42: ...3 26 F 143 0211 Edition ASSEMBLY INSTRUCTIONS Figure 3 15 Decal Installation ...
Page 44: ...3 28 F 143 0211 Edition ASSEMBLY INSTRUCTIONS Notes ...
Page 54: ...4 10 F 143 0211 Edition OPERATION AND MAINTENANCE Notes ...
Page 58: ...5 4 F 143 0211 Edition TROUBLESHOOTING GUIDE Notes ...
Page 59: ......