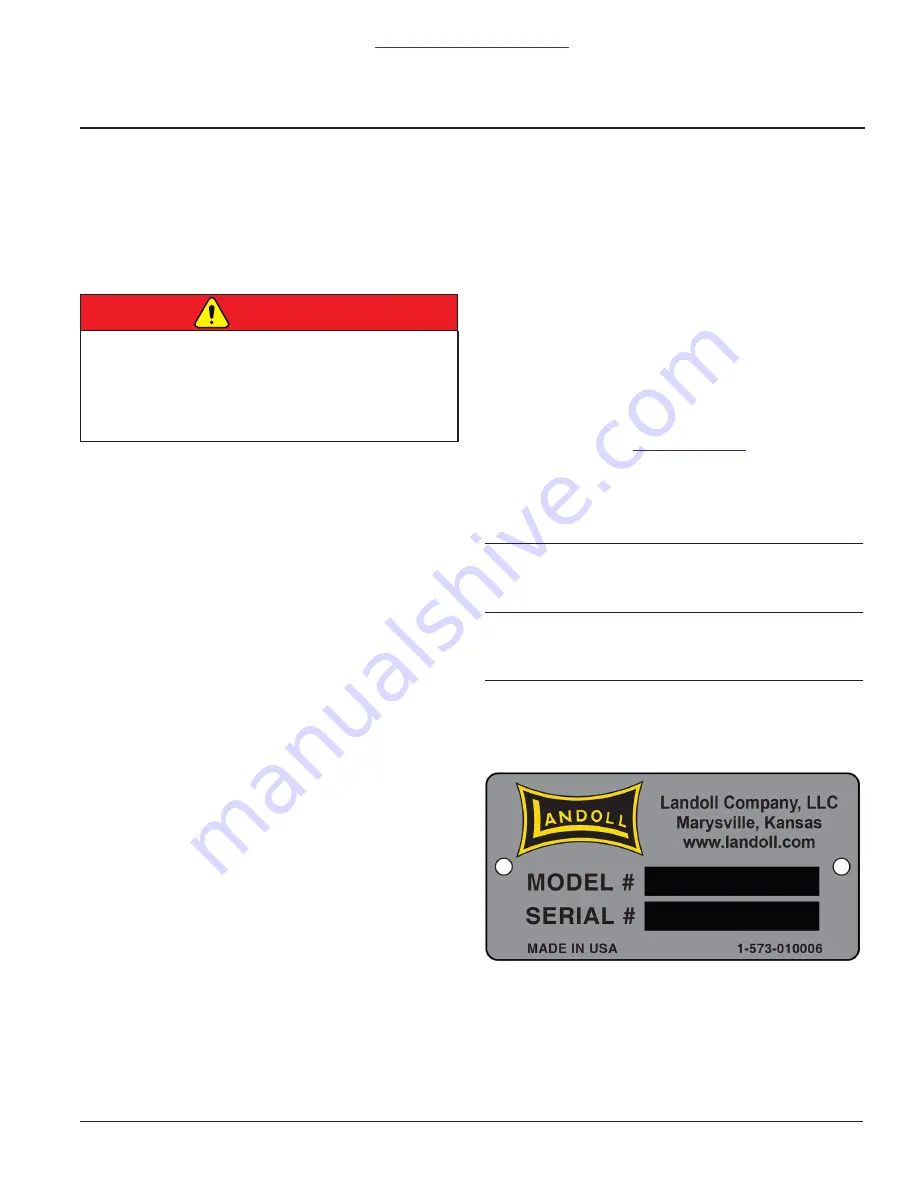
F-661-0321
1-1
Chapter 1
Safety Information
Introduction
The implement described in this manual has been
designed with care and built by skilled workers using
quality materials and processes. Proper assembly and
maintenance will provide you with satisfactory use for
seasons to come.
DANGER
DANGER
Description of Unit
The Brillion
Wing Float Pulverizer
is designed with a
telescoping drawbar making it versatile to use directly
behind a tractor or a companion tool in both pre-plant and
post-plant situations. By its patented design, the wings
and the center section operate independently during field
operation. The wings are capable of floating in two planes
vertically and horizontally without altering the position of
the center section. The Wing Float Pulverizer uses a
single hydraulic circuit that lifts and folds the machine.
Trunnions Bearings mount the 8" Rollers Axles with a
choice of 20" Notched Ductile, 20" Optimizer and 20"
Crowfoot Wheels.
Using this Manual
This manual will familiarize you with safety, assembly,
operation, adjustment, and maintenance. Read this
manual and follow the recommendations to help ensure
safe and efficient operation.
• The information in this manual is current at time of
printing. Some parts may have changed to assure top
performance.
• Location reference: Right and Left designations in this
manual are determined by facing the direction the
implement will travel during field operation, unless
otherwise stated.
Owner Assistance
If customer service or repairs are needed, contact your
Brillion dealer. They have trained personnel, parts and
service equipment specially designed for Brillion
products. Your implement’s parts should only be replaced
with Brillion parts. If items covered in this manual are not
understood, contact your local Brillion dealer.
Warranty Registration
instructions regarding product registration.
Enter your product information below for quick reference.
MODEL NUMBER
SERIAL NUMBER
DATE OF PURCHASE
Refer to the ID plate as shown.
Figure 1-1: ID Plate
Read this entire manual before attempting to
assemble, adjust or operate this implement.
Failure to comply with this warning can result in
personal injury or death, damage
to the
implement or its components and inferior
operation.