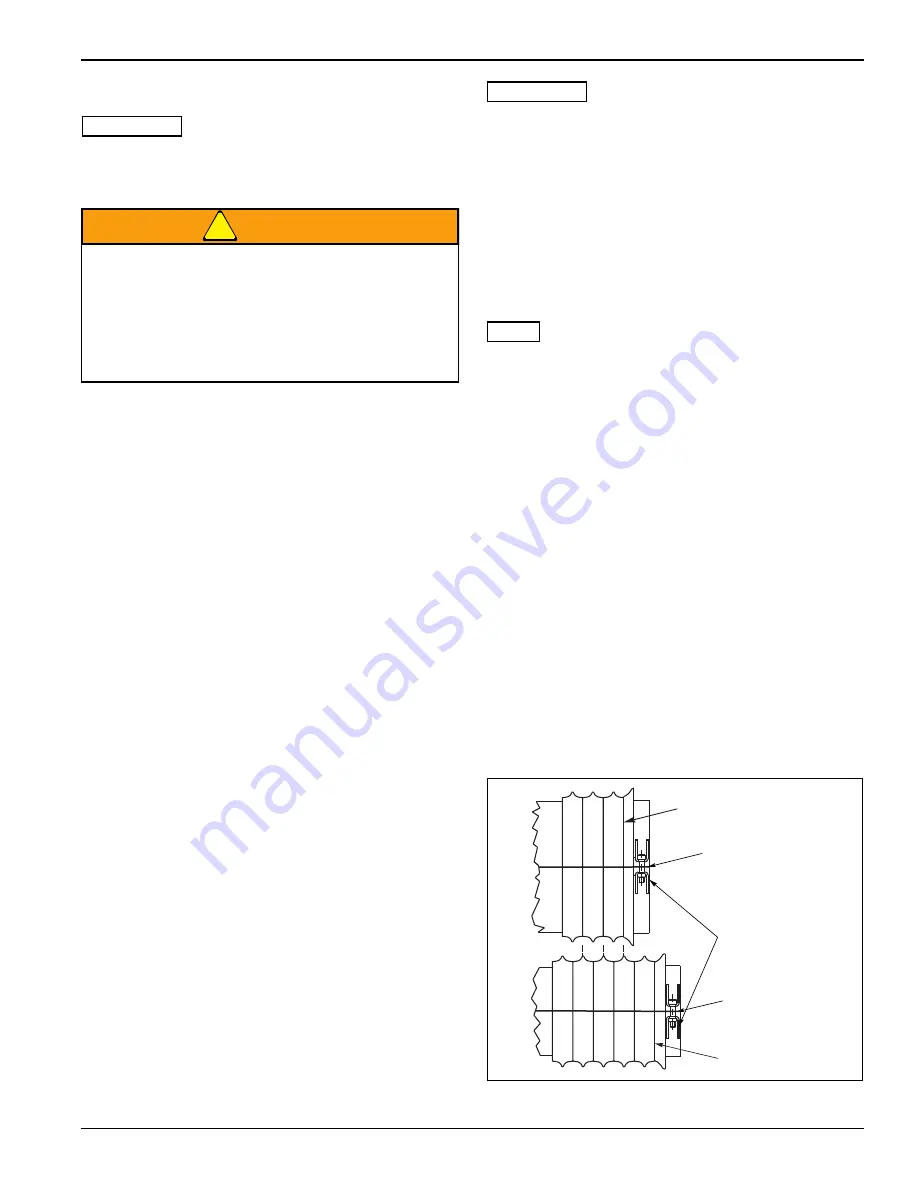
MAINTENANCE
9K998 4-5
Hydraulic Maintenance
IMPORTANT
Lower the unit to the ground, and relieve hydraulic
pressure before attempting to service any hydraulic
component.
WARNING
1. Check the tractor hydraulic fluid level per Tractor
owner's manual and after any leakage. Check fluid
level with the Hydraulic Cylinders in the extended
position.
2. If a Hydraulic Cylinder leaks, disassemble the parts
to determine the cause of the leak. Any time a
Hydraulic Cylinder is opened up, or whenever any
Seal replacement is necessary, it is advisable to
clean all parts and replace all Seals. Seal Kits are
available from your Brillion dealer.
3. Check all Hydraulic Hoses weekly. Look for binding
or cracking. Replace all worn or defective parts
immediately.
4. Transport Locks are provided to hold the implement
in a raised position. Do not attempt to perform any
service work under the implement without first
installing the Transport Locks.
Before
servicing any hydraulic component, lower the
implement to the ground and relieve all system
pressure. If a hydraulic component is disconnected,
repaired, or replaced, it will be necessary to purge
the system of air before operation.
Front and Rear Rollers
After an initial run of 5-10 hours, check the Front and
Rear Roller Assemblies to ensure that the Wheels are
tight to one another and that the Clamp Bands are tight. If
not slide the Roller Wheels tight together and adjust the
Roller Clamp Bands. Tighten the Clamp Band Socket
Head Bolt (Clamp Band open section) over Roller Drum
weld seam to 75ft-lbs. Thereafter check Front and Rear
Roller Assemblies every 50-100 hours.
IMPORTANT
To maximize seed germination, peaks on Rear Roller
Wheels should line up with valleys on the Front
Roller Wheels. This will require adjusting the Clamp
Bands on each end of the Rear Roller Drum and
moving the Wheels until valleys and peaks line up.
Turfmaker Sprockets may be added between the
Rear Roller Wheels to improve the alignment of the
peaks and valleys. Add as many Turfmaker
Sprockets between the Wheels as required to
achieve proper alignment. Each Sprocket is 3/8”
wide. Figure 2-56.
NOTE
Failure to position the Clamp Band Socket Head Bolt
(Clamp Band open section) over the Roller Drum weld
seam will cause Clamp Band to loosen and slide.
Roller Adjustment Procedure
1. Adjust the Front Roller Wheels first. Loosen Clamp
Bands and slide the Roller Wheels snug against
each other, centering the entire assembly under the
Deflector.
2. Position the Clamp Band Socket Head Bolt (Clamp
Band open section) over the weld seam on the Roller
Drum.
3. Slide the Clamp Band against the End Wheel on
each end of the Roller and tighten the Clamp Band
Bolt to 75ft-lbs.
Adjust the Rear Roller Wheels in the same manner as
you adjusted the Front Roller Wheels except, start at the
center of the Rear Roller and align the peaks of the Rear
Roller Wheels with the valleys of the Front Roller Wheels.
This will provide the best alignment of worn Roller
Wheels.
Figure 4-3: Clamp Bands
Escaping fluid under pressure can be nearly
invisible and have enough force to penetrate the
skin causing serious injury. Use a piece of
cardboard, rather than hands to search for
suspected leaks. Wear protective gloves and
safety glasses or goggles when working with
Hydraulic System
5HDU5ROOHU
)URQW 5ROOHU
&ODPS%DQGV
:HOGHG6HDP
:HOGHG6HDP
Summary of Contents for BRILLION TURFMAKER II SL
Page 2: ......
Page 6: ...iv...
Page 14: ...1 8 9K998 INTRODUCTION AND SAFETY INFORMATION Figure 1 6 Safety Signs 4 of 5 6 HFDOV RXEOH R...
Page 15: ...INTRODUCTION AND SAFETY INFORMATION 9K998 1 9 Figure 1 7 Safety Signs 5 of 5 6 LWFK HFDOV...
Page 16: ...1 10 9K998 INTRODUCTION AND SAFETY INFORMATION Table provided for general use NOTES...
Page 25: ...ASSEMBLY 9K998 2 9 Table provided for general use NOTES...
Page 31: ...ASSEMBLY 9K998 2 15 Table provided for general use NOTES...
Page 36: ...2 20 9K998 ASSEMBLY Table provided for general use NOTES...
Page 58: ...2 42 9K998 ASSEMBLY Table provided for general use NOTES...
Page 80: ...3 22 9K998 OPERATION Table provided for general use NOTES...
Page 92: ...4 12 9K998 MAINTENANCE Table provided for general use NOTES...
Page 99: ......