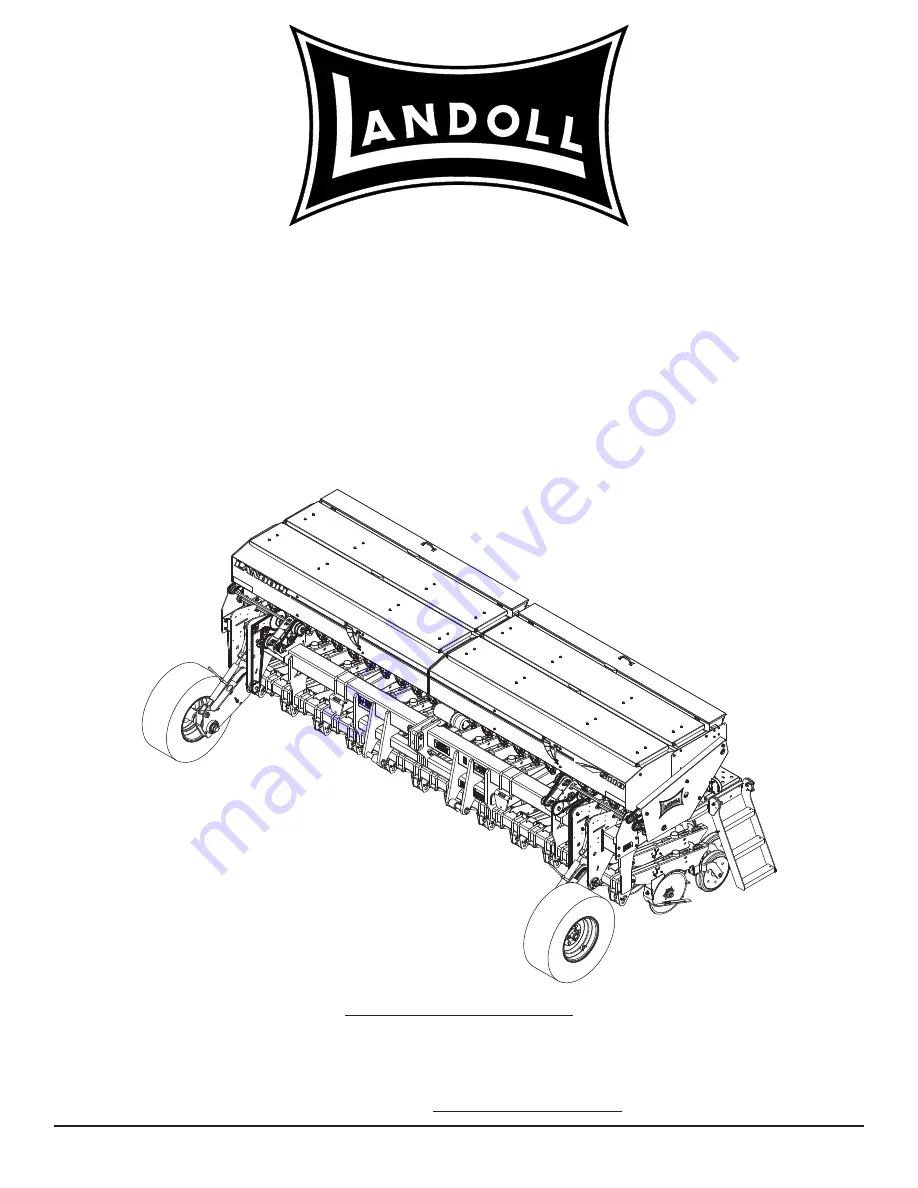
®
Model 5110NG
Native Grass Drill
Operator’s Manual
LANDOLL COMPANY, LLC
1900 North Street
Marysville, Kansas 66508
800-428-5655 ~ WWW.LANDOLL.COM
F-1058-0820
08/2020-Present
®
Model 5110NG
Native Grass Drill
Operator’s Manual
LANDOLL COMPANY, LLC
1900 North Street
Marysville, Kansas 66508
800-428-5655 ~ WWW.LANDOLL.COM
F-1058-0820
08/2020-Present