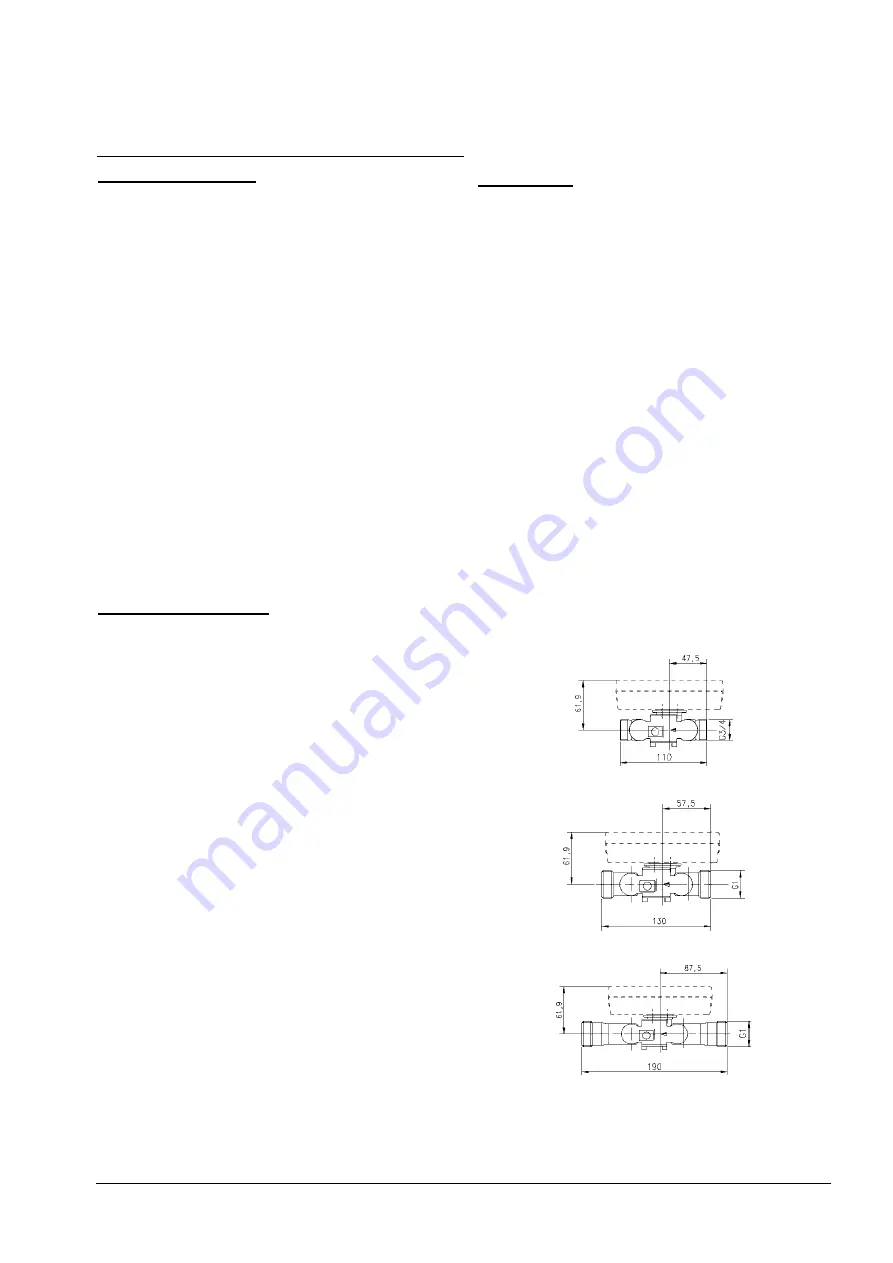
UH50 Ultrasonic Heat Meter
Subject to change without prior notice
UH 206-101c
Page 1 / 8
Heat Meter Ultrasonic
®
UH50
Installation
UH 206-101c
and Service Instructions
Version: October 2007
Safety information
)
Do not pick up by the electronic unit
)
Be careful of sharp edges (thread, flange,
measuring tube)
)
Installation and removal must be performed
by qualified personnel only
)
Mounting and unmounting are only permitted
when the system is not under pressure
)
After installation, a tightness test must be
conducted with cold pressure
)
Only ever use under service conditions,
otherwise dangers can arise and the warranty
may be voided
)
Breaking the calibration seal voids the
warranty
)
The 110
V
/
230
V versions must only be
connected by an electrician
)
The lithium batteries must be properly
returned
)
Lightning protection cannot be ensured; this
must be provided by the building wiring
)
Only one compartment for the power supply
must be equipped – do not remove the red
locking hatch
General information
The electronic unit is plugged onto an adapter plate
and can be separated by pushing the volume
measuring unit upward.
The packaging should be kept so that the heat
meter can be shipped in its original packing after the
calibation period has elapsed.
If the heat meter was not supplied with a battery
connected, the current date and time must be
entered during start-up (see “Parameter setting”).
The 110 V / 230 V power supply units comply with
safety class II, so the line voltage does not need to
be disconnected when changing the unit.
All cables must be laid at a
minimum distance of
300 mm
from power cables or radio-frequency
cables.
By overpressure, cavitation must be avoided in the
entire measuring range, i.e
. at least 1 bar at q
p
and
approx. 3 bar at q
s
(applies to approx. 80°C).
The heat meter left the factory in perfect safe
condition. Calibration, maintenance, component
replacement, and repairs must only be performed by
trained personnel who are familiar with the hazards
involved. The manufacturer will provide further
technical support on request. Heat meter safety
marks that are relevant for calibration must not be
damaged or removed! Otherwise the warranty and
calibration validity of the device will expire.
Installation
Choose the mounting location (return or flow) in
accordance with the labeling on the heat meter.
Study the table for the dimensions and check that
there is enough clearance.
No inlet or outlet sections are necessary. However,
if the heat meter is installed in the shared return of
two heating systems, e.g. heating and hot water, the
mounting location must be a sufficient distance from
the T element that forms the junction (
min. 10
×
DN
)
to allow the different water temperatures to mix well.
Before the heat meter is installed, the system must
be rinsed thoroughly.
As shown in the examples on Page 2, mount the
volume measuring unit horizontally or vertically
between two shut-off valves in accordance with the
arrow for the direction of flow. The sensors must be
mounted in the same heating circuit as the volume
measuring unit. For installation as a
cold meter,
see
the following notes.
The sensor can be mounted in ball valves, in
pockets or direct immersed. The end of the sensors
must extend in any case as far as the center of the
pipe cross-section. Temperature sensors and screw
joints must be sealed for protection from tampering.
Small heat meters (q
p
0.6 - 2.5 m³/h)
Overall length 110 mm (thread)
Overall length 130 mm (thread)
Overall length 190 mm (thread)
3250 006 101 c