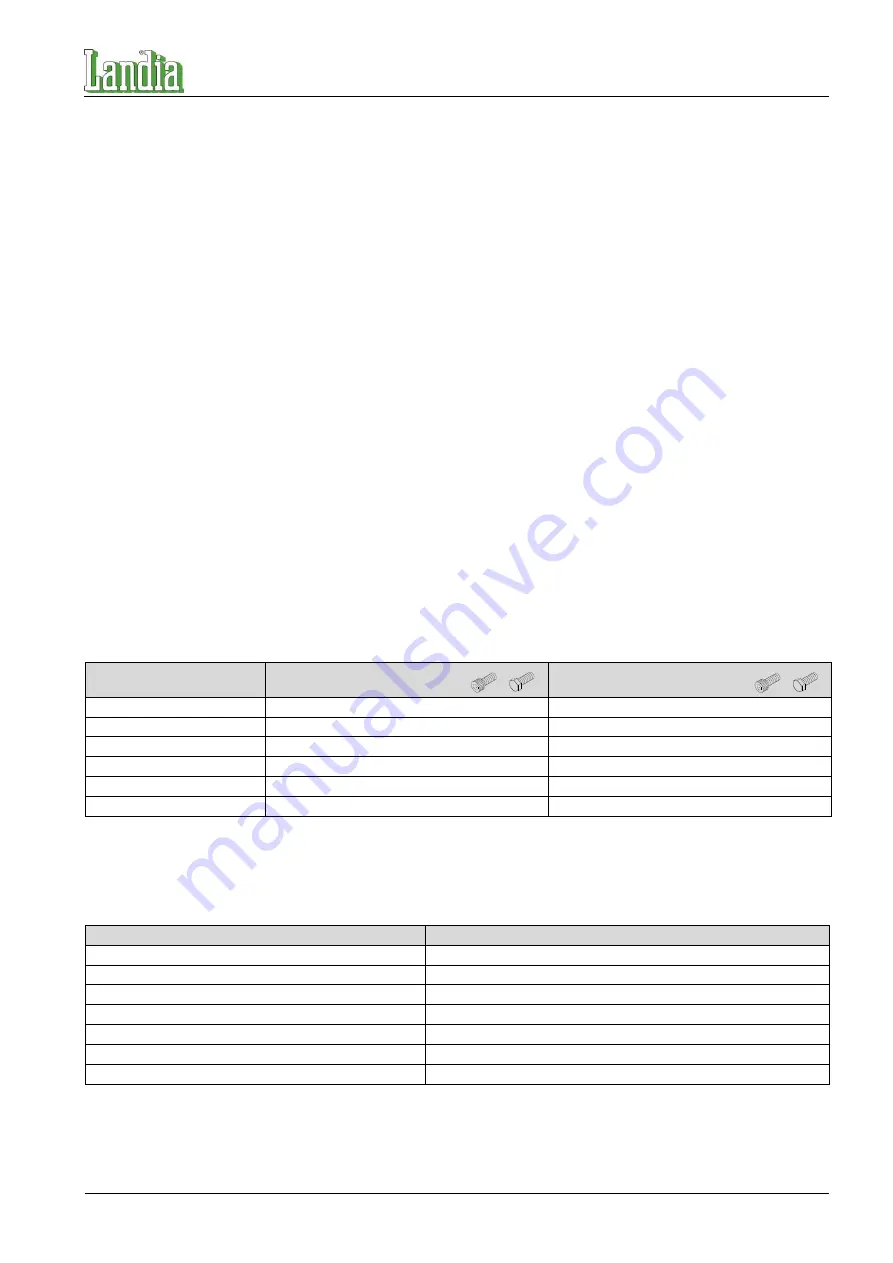
CA02A.C01
Service instruction: POP-I
Side 6/8
Executed by: HL
Issued on: 11 December 2002
Accepted by: SL
Rev. date: 22 November 2017
The oil is drained off by removing the plugs pos. B and pos. C (ms.100-180) or pos. C (ms.80-90). If the oil is dirty,
seal and wear bushes must be checked for wear and contamination.
During filling of oil through oil plug pos. A (ms.100-180) the oil plug pos. G must be removed to allow bleeding of the
gear. For ms.80-90 oil is filled at oil plug pos. G on the gear.
Lubricate the outer sealing system with grease (see spare parts list). This takes place through the grease nipple,
pos. F, which is fixed in the propeller behind one of the propeller blades. Prior to reinstalling the propeller fill up the
hub with grease lubricant.
The motor casing must be inspected in the following way: Remove the inspection plug, pos. D, beneath the motor.
Any seepage of oil or liquid can be seen immediately.
In case of abnormal seepage it is necessary to check the seal in the oil chamber. If in doubt, please contact Landia.
If it is necessary to dry up the motor windings, contact an electric motor repair workshop.
Equipment
The equipment should be inspected for wear and corrosion. The winch is to be lubricated with grease. Inspect brake
and lock. Retighten screws. If the screws are loose remove them and lubricate with Loctite 243 prior to
reinstallation.
Disassembling/Assembling the Unit
A major repair should take place at a workshop which is specialized in this type of repair. We can refer to a service
partner in your territory. Below please find some general conditions regarding disassembling/ assembling of Landia
mixer type POP-I. The drawing attached to the spare parts list shows the construction of the unit. Not all parts
can/should be removed, e.g. do not press the rotor off the shaft.
When disassembling the unit, handle the mechanical seals with care as they are not shock resistant. Prior to
reinstallation, all sealing surfaces must be cleaned; all O-rings must be checked and changed if necessary.
Adhesive substance (e.g. Loctite) must be applied on all bolt joints. All bolts must be tightened with a torque wrench
as specified in the table below.
Bolt sizes
Quality 10.9
– 12.9
Steel
Quality A4 kl. 80
St. steel
M6
10 ft-lbf
7 ft-lbf
M8
25 ft-lbf
18 ft-lbf
M10
49 ft-lbf
35 ft-lbf
M12
85 ft-lbf
60 ft-lbf
M16
118 ft-lbf
101 ft-lbf
M20
148 ft-lbf
133 ft-lbf
Please Note
End cover, oil chamber and gear must be turned anti-clockwise as much as possible, seen from the end of the
propeller, in order to balance the clearance in the bolt holes before the final tightening of the bolts.
After installing the bearing flange control the axial clearance; as stated in the table below.
Motor series (ms) see spare parts list
Acceptable clearance
ms.80
0.028 ± 0,002 inch
ms.90
0.028 ± 0,002 inch
ms.100
0.035 ± 0,002 inch
ms.112
0.039 ± 0,002 inch
ms.132
0.039 ± 0,002 inch
ms.160
0.043 ± 0,002 inch
ms.180
0.059 ± 0,002 inch