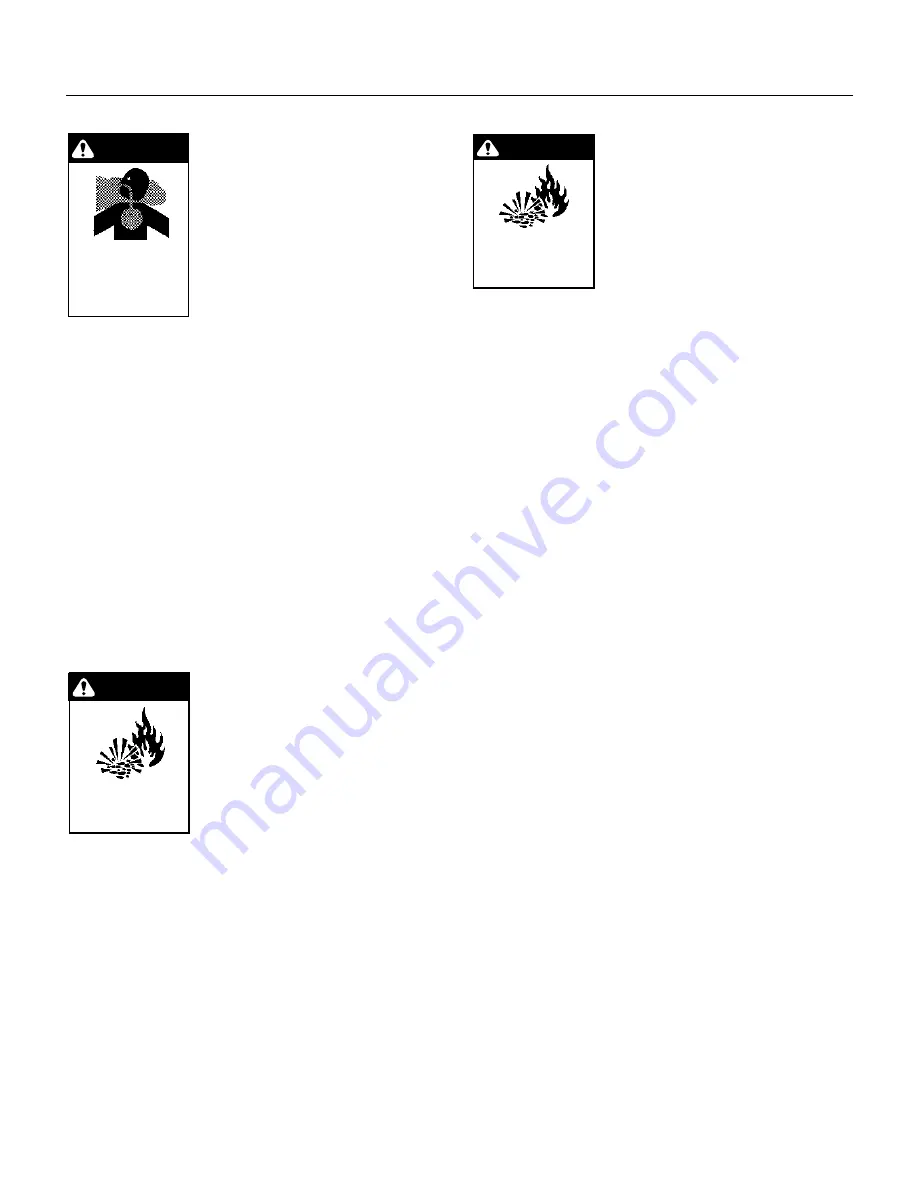
VNG/VLP SERIES PRESSURE WASHER
OPERATOR’S MANUAL
6
WARNING: Risk of asphyxiation.
Use this product in a well ventilated
area.
9. When the unit is working, do not
cover or place in a closed space
where ventilation is insufficient.
10. Units with shut-off gun should not
be operated with the trigger in the
off position for extensive periods
of time as this may cause dam-
age to the pump.
11. Protect from freezing.
12. Be certain all quick coupler fittings are secured be-
fore using pressure washer.
13. Do not allow acids, caustic, or abrasive fluids to pass
through the pump.
14. Inlet water must be cold.
15. Do not allow CHILDREN to operate the pressure
washer at any time.
16. The best insurance against an accident is precaution,
and knowledge of the machine.
17. Do not operate this product when fatigued or under
the influence of alcohol or drugs. Keep operating area
clear of all persons.
18. Do not replace LP Tank while unit is running. Serious
injury could result.
WARNING: Use vapor fuel only.
19. The VLP models are designed to
run on vapor propane fuel. Do not
use liquid fuel. Have a qualified
serviceman install and service
your equipment.
20. Never expose a spark or flame
where there may be unburned
gas present.
21. L.P. gases are heavier than air
and will spill out on the floor. Therefore always provide
adequate space and ventilation around these units.
Install the machine 18” above the floor.
22. Landa will not be liable for any changes made to our
standard units, or any components not purchased from
Landa.
23. Do not overreach or stand on unstable support. Keep
good footing and balance at all times.
24. Follow the maintenance instructions specified in the
manual.
25. When making repairs disconnect from electrical source
and shut off gas valve.
26. Turn burner off and cool to 100° before turning ma-
chine off.
WARNING: If you smell gas, shut off
the gas supply to the appliance
27. Extinguish any open flame, and
test all joints with a soap solution.
If the odor persists, call your gas
supplier immediately.
28. This machine must be attended
during operation.
29. Not suitable for connection to Type B gas vent if the
stack temperature exceeds 243° C (470° F).
30. A draft hood shall be installed if this machine is going
to be permanently installed and vented to the outside
of the building.
INSTALLATION
Place machine in a convenient location providing ample
support, draining and room for maintenance.
Location:
This machine is certified for indoor installation. Its location
should protect the machine from damaging environmen-
tal conditions, such as wind, rain and freezing.
1. The machine should be run on a level surface where
it is not readily influenced by outside sources such as
strong winds, freezing temperatures, rain, etc. The unit
should be located considering accessibility of the com-
ponents and the refilling of detergents, adjustments
and maintenance. Normal precautions should be taken
by the operator of the unit to prevent excess moisture
from reaching the power unit or electrical controls.
2. It is recommended that a partition be made between
the wash area and the machine to prevent direct spray
from the gun from coming in contact with the machine.
Excess moisture reaching the pressure washer or the
electrical controls will reduce the life of the unit and
may cause electrical shorts.
3. During installation of the unit, beware of poorly venti-
lated locations or areas where exhaust fans may cause
an insufficient supply of oxygen. Sufficient combus-
tion can only be obtained when there is a sufficient
supply of oxygen available for the amount of fuel be-
ing burned. If it is necessary to install a unit in a poorly
ventilated area, outside fresh air may have to be piped
to the burner and a fan installed bringing the air into
the area
4. Do not locate near any combustible material. Keep all
flammable material at least 20 feet away.
Allow enough space for servicing the unit.
Local code will require certain distances from floor
and walls. (Two feet away should be adequate.)
A
VOID
SMALL
LOCATIONS
OR
AREAS
NEAR
EXHAUST
FANS
.
WARNING
RISK OF EXPLOSION:
IF GAS SMELL IS
PRESENT, TURN OFF
SUPPLY.
WARNING
RISK OF
ASPHYXIATION. USE
THIS PRODUCT ONLY
IN A WELL
VENTILATED AREA.
WARNING
RISK OF FIRE OR
EXPLOSION, USE
VAPOR FUEL ONLY.