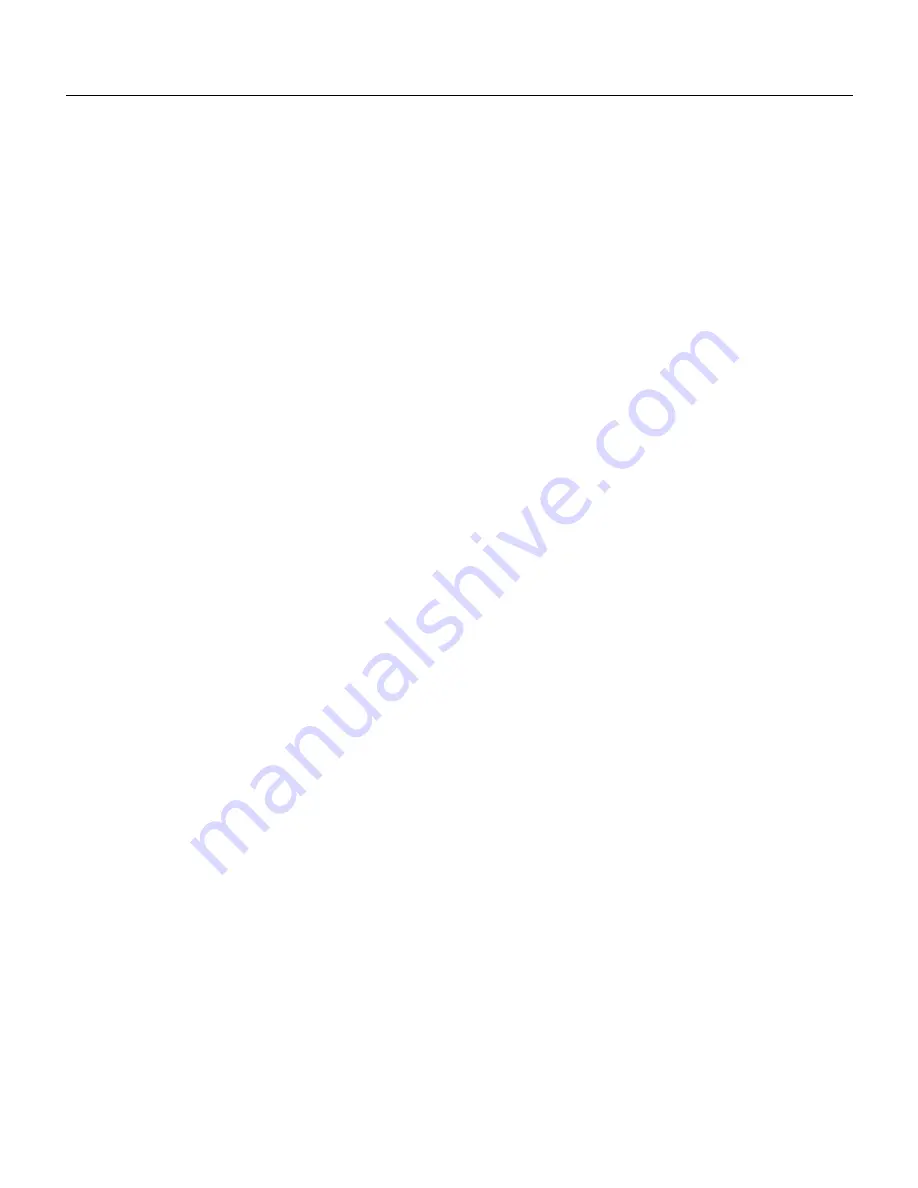
VNG/VLP SERIES PRESSURE WASHER
OPERATOR’S MANUAL
16
3. Attach a short section (3-5 ft.) of garden hose to ma-
chine to siphon solution from an elevated container or
add mixture to the float tank. Turn pump switch on
allowing solution to be pumped through coil and back
into the container. Solution should be allowed to cir-
culate 2-4 hours.
4. After circulating solution flush entire system with fresh
water. Reinstall nozzle in gun.
GAS VALVE REGULATOR
ADJUSTMENT
Adjustment of the built-in regulator isn’t normally neces-
sary, since it is preset at the factory. However, field adjust-
ment may be accomplished as follows:
1. Attach manometer at pressure tap port.
2. Remove regulator adjustment screw cap.
3. With a small screwdriver, rotate the adjustment screw
clockwise to increase or counterclockwise to decrease
gas pressure.
4. Replace regulator adjustment screw cap (see Figure
6, page 11).
In alkaline water areas, lime deposits can accumulate rap-
idly inside the coil pipes. This growth is increased by the
extreme heat build up in the coil. The best preventative for
liming conditions is to use high quality cleaning chemi-
cals. In areas where alkaline water is an extreme prob-
lem, periodic use of Landa Deliming Powder will remove
lime and other deposits before coil becomes plugged. (See
Deliming Instructions for use of Landa Deliming Powder.)
Pressure Relief Valve
Each unit is equipped with a relief valve to relieve pres-
sure in the system when higher than normally operating
pressures are encountered. If operating pressure of unit
is found to be normal and relief valve continues to leak,
repair or replace the valve. CAUTION: Relief valve can
become obstructed by deposits and must be unscrewed
at least once per year to allow discharge.
PROPANE GAS
General Safety Precautions
Have a qualified gas service person assist in any gas
burner installation or service. Few maintenance people or
mechanics are knowledgeable in gas controls or related
safety practices. Propane Gas is heavier than air; unburned
Propane Gas will gravitate to the floor rather than rise out
of the stack. Hence, adequate floor space and good ven-
tilation are especially important with propane systems.
Gas Pressure Requirements
All propane fired units operate on vapor propane fuel only.
They are designed to operate at a pressure of 11” water
column (between 1/3 and 1/2 of one psi), and are often
operated at even higher pressures when extra heat is
needed.
Exterior regulators are needed to control the system. Pro-
pane bottles are not included with the unit. A high pres-
sure regulator should be installed on the propane bottle
and a low pressure regulator attached to the pressure
washer.
Propane Cylinder Capacity
An important consideration with propane systems is the
capacity of the supply cylinder relative to the needs of the
burner. The burner operates on propane as a vapor gas.
As gas is used from the propane cylinder, the liquid in the
cylinder boils to maintain vapor gas pressure. This boiling
process cools the liquid, and in a heavy, continuous-de-
mand situation, the liquid temperature can fall to the point
at which it cannot provide vapor gas as rapidly as is
needed. In this case, it may be necessary to warm the
Propane Cylinder by directing a warm spray, not over 120°
F, on the cold cylinder or by manifolding two propane bottles
together to increase total vaporization capacity. It is rec-
ommended that a minimum 100 lb. vapor propane bottle
be used on the unit, depending on the length of running
time desired.
BURNER FEATURES
Operated Automatic Valve
This machine is equipped with an Intermittent Pilot Igni-
tion System. This System is designed to eliminate the need
for a constant burning pilot. Lighting of the pilot is accom-
plished through electronic spark ignition each time the
burner and flow switch call for heat. The pilot is not burn-
ing when there is no call for heat. Do not attempt to light
the appliance manually as a burn injury or electrical shock
may result. The pilot light will remain on and the main gas
valve is turned off when the spray gun is closed.
Care of Main Burner
Due to condensation from heater coils dripping down on
the burners, a scale build-up may occur in the burner jet
orifices.
1. TO REMOVE BURNER MANIFOLD FROM WATER
HEATER COIL:
Turn off the gas to the main burner by turning the
knob to the “OFF” position on the gas valve and the
main gas supply.