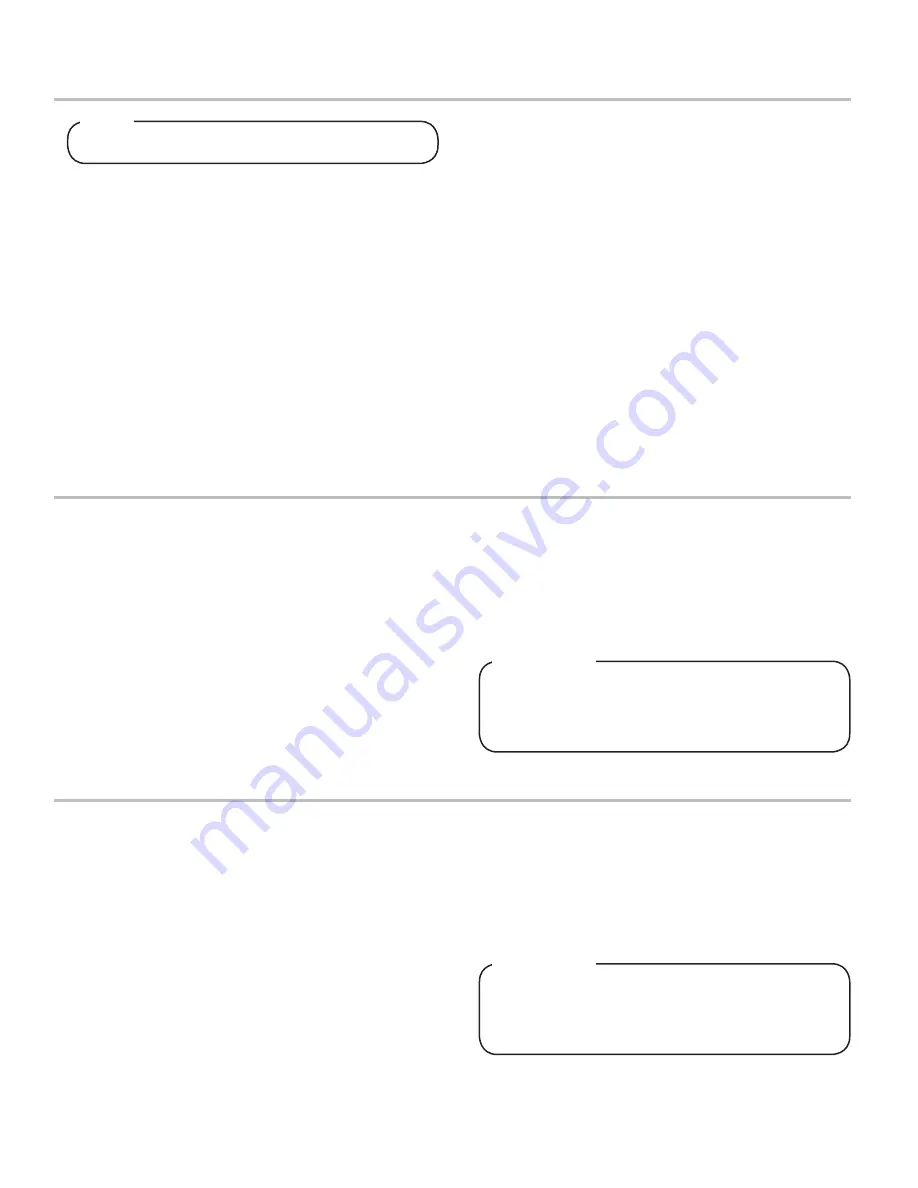
17
Ice Bin Cleaning - Start-Up and Monthly
1.
Disconnect power to the dispenser
2.
Remove Top Cover.
3.
Melt out any remaining ice from the bin.
4.
Remove Agitator Pin from Agitator Shaft. Slide Agitator
Shaft rearward out Hub and pull out of rear Bearing to
remove.
5.
Remove Ice Shroud by lifting and rotating out from beneath
the auger.
6.
Use the Cleaning Solution, and a clean cloth or soft brush,
to clean all removable parts, sides of the Ice Bin, Auger,
and surface of the aluminum casting.
7. Using the Cleaning Solution and the sponge brush
provided, clean all interior surfaces of the ice chute and the
ice chute feed through.
Refer to the Automatic Agitation Warning on page 4.
NOTE
8.
Repeat Step 6 for all exterior surfaces of the dispenser.
9.
Using hot water, thoroughly rinse away the cleaning
solution.
10.
Wearing sanitary gloves, soak and clean cloth towel in
Sanitizing Solution and wash all surfaces of removable
parts, sides of the Ice Bin, Auger, and surface of the
aluminum casting.
11. Using the Sanitizing Solution and the sponge brush
provided, clean all interior surfaces of the ice chute and the
ice chute feed through.
12.
Repeat Step 10 for all exterior surfaces of the dispenser.
13.
Wearing sanitary gloves, reassemble all removable parts.
Ensure agitator clip is locked.
14.
Fill Unit with ice and replace Top Cover.
15.
Reconnect Dispenser to power source.
Cleaning and Sanitizing Syrup Lines - Bag in Box
Cleaning and Sanitizing Flavor Shot Lines
1. Disconnect syrup lines from BIB’s
2.
Place syrup lines, with BIB connectors, in a bucket of warm
water.
3.
Activate each valve to fill the lines with warm water and
flush out syrup remaining in the lines.
4. Prepare Cleaning Solution described above.
5.
Place syrup lines, with BIB connectors, into cleaning
solution.
6. Activate each valve until lines are filled with cleaning
solution then let stand for ten (10) minutes.
7. Flush out cleaning solution from the syrup lines using clean,
warm water.
1.
Disconnect the four (4) flavor injector lines from their bag-
in-box containers.
2.
Place flavor injector lines, with BIB connectors, in a bucket
of warm water.
3.
Activate each flavor injector line to fill the with warm water
and flush out any syrup remaining in the lines.
4. Prepare Cleaning Solution described on previous page.
5.
Place flavor injector lines, with BIB connectors, into clean-
ing solution.
6. Activate each flavor injector line until lines are filled with
cleaning solution then let stand for ten (10) minutes.
7.
Flush out cleaning solution from the flavor injector lines
using clean, warm water.
Following sanitization, rinse with end-use product
until there is no aftertaste. Do not use a fresh water
rinse. This is a NSF requirement. Residual sanitizing
solution left in the system creates a health hazard.
!
CAUTION
Following sanitization, rinse with end-use product
until there is no aftertaste. Do not use a fresh water
rinse. This is a NSF requirement. Residual sanitizing
solution left in the system creates a health hazard.
!
CAUTION
8. Prepare Sanitizing Solution described above.
9. Place syrup lines into sanitizing solution and activate each
valve to fill lines with sanitizer. Let sit for ten (10) minutes.
10.
Reconnect syrup lines to BIB’s and draw drinks to flush
solution from the dispenser.
11.
Taste the drink to verify that there is no off-taste. If off-taste
is found, flush syrup system again.
8. Prepare Sanitizing Solution described on previous page.
9.
Place flavor lines into sanitizing solution and activate each
line to fill with sanitizer. Let sit for ten (10) minutes.
10.
Reconnect syrup lines to bag-in-box container and draw
drinks to flush solution from the dispenser.
11.
Taste the drink to verify that there is no off-taste. If off-taste
is found, flush syrup system again.