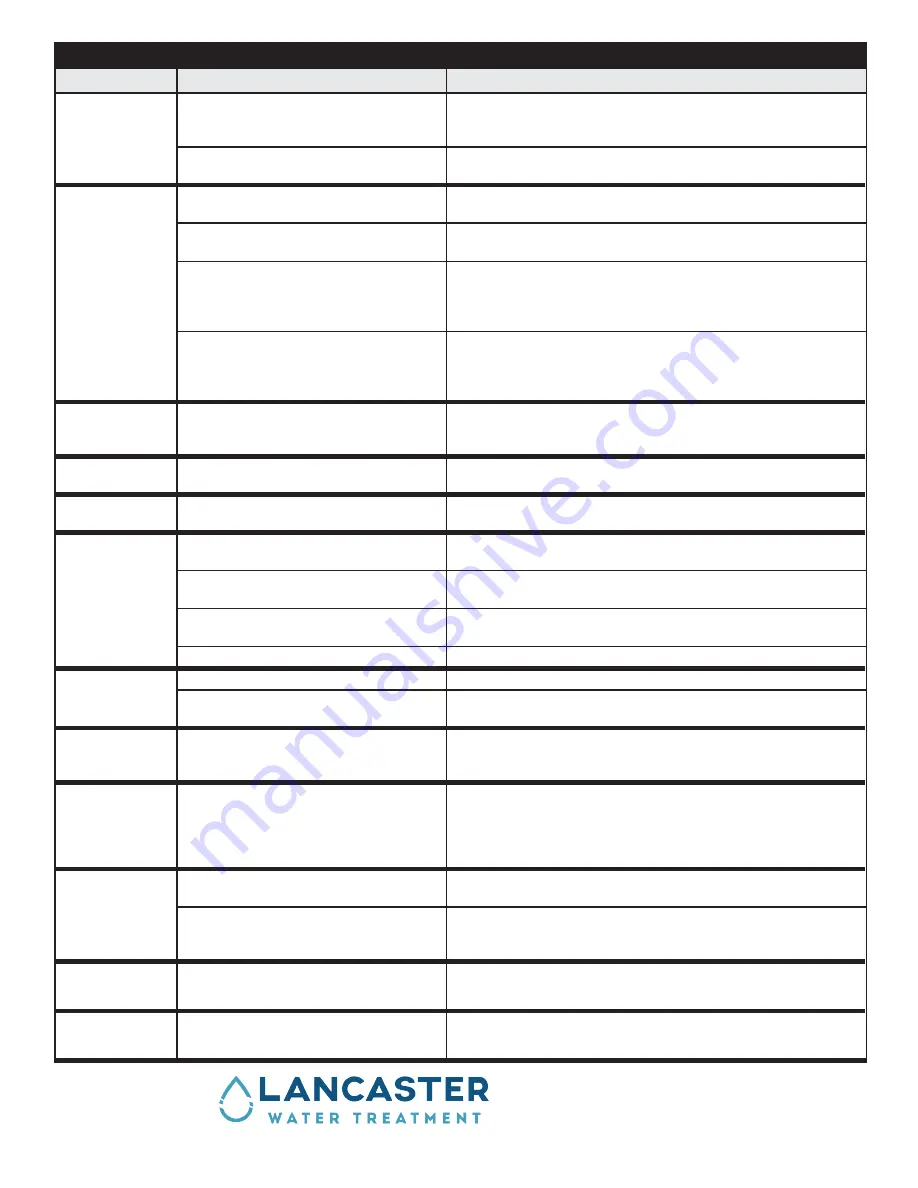
PAGE 16
11/19
A DIVISION OF C-B TOOL CO.
1340 MANHEIM PIKE ● LANCASTER PA 17601-3196 ● TEL:717-397-3521 ● FAX: 717-392-0266
www.lancasterwatertreatment.com ● E-mail: [email protected]
TROUBLESHOOTING GUIDE
Symptom
Possible Causes
Solutions
Pressure Drop
Sediment pre-filter clogged
•
replace filter cartridge with appropriate 5 micron cartridge
Note:
check source water supply as fluctuations may occur in
source pressure
Flow regulator (not provided)
•
flow regulator will result in pressure drop when approaching full
flow
High Bacteria
Counts
Quartz sleeve is stained or dirty
•
clean sleeve with scale cleaner and eliminate source of staining
problem (i.e. soften hard water, see page 3)
Change in feed water quality
•
have source water tested to ensure that water quality is still
within allowable limits for this system
Contamination in water lines after UV
system due to a power failure, plumbing
dead ends, etc.
•
it is imperative that effluent water stream be shocked with
chlorine (bleach) before water leaves UV system - disinfection
system must have a bacterial free distribution system to work
effectively (see page 10-11 disinfection procedure).
Possible break-through of sediment
through pre-filter
•
have source water tested for turbidity - may need stepped
filtration in order to catch all sediment entering water system
(20 micron filter followed by a 5 micron filter followed by UV
system)
Heated Product
Water
Common problem caused by infrequent
use of water; water sitting in UV chamber
and heating up
•
run water until it returns to ambient temperature
Excessive Heat
Generated
Water temperature is too high
•
Ensure treatment is on cold water side only (prior to heating of
water)
Water Appears
Milky
Caused by air in the water lines
•
run water until air is purged
UV Chamber
Leaking Water
Problem with o-ring seal on gland nut
•
ensure o-ring is in place, check for cuts or abrasions, clean
o-ring, moisten with water and re-install, replace if necessary
Condensation on reactor chamber caused
by excessive humidity & cold water
•
check location of disinfection system and control humidity
Inadequate (misaligned or cross-threaded)
inlet/outlet port connections
•
check thread connections, reseal with Teflon® tape and re-
tighten
Water hammer causing pressure spikes
•
Install a “water hammer” arrestor in the plumbing system
Leaks Between
Filter Sump and
Filter Head.
Sump not sufficiently tightened.
•
Tighten further the sump with the wrench.
O-ring affected/old.
•
If the sump still leaks, change the sump’s O-ring with a new one
(use original replacement / spare parts).
Leaks in Filter
Inlet / Outlet
Connections.
Not enough sealant and/or connection not
sufficiently tightened.
•
Remove the previous sealing tape from the fitting and place
more sealing tape and/or tighten the connection properly.
System
Shutting Down
Intermittently
Interrupted power supply
•
ensure system has been installed on its own circuit, as other
equipment may be drawing power away from UV (i.e. pump or
refrigerator)
•
UV system should not be installed on a circuit which is
incorporated into a light switch
Lamp Failure
Alarm on - New
Lamp
Loose connection between lamp and
connector
•
disconnect lamp from connector and reconnect, ensuring that a
tight fit is accomplished
Moisture build up in connector may keep
lamp and connector from making a solid
connection
•
eliminate chanc e of any moisture getting to the connector and/
or lamp pins
LED Display
reads “A3”
Lamp life expired - countdown is at “0”
days
•
Press and hold button 2 to 5 seconds for an alarm silence
delay, replace lamp (see page 12 UV lamp replacement)
LED Display is
Blank
No power to electronic ballast;
GFCI wall socket is tripped
•
Reset, following GFCI manufacturer’s instructions
•
Check socket with other applications