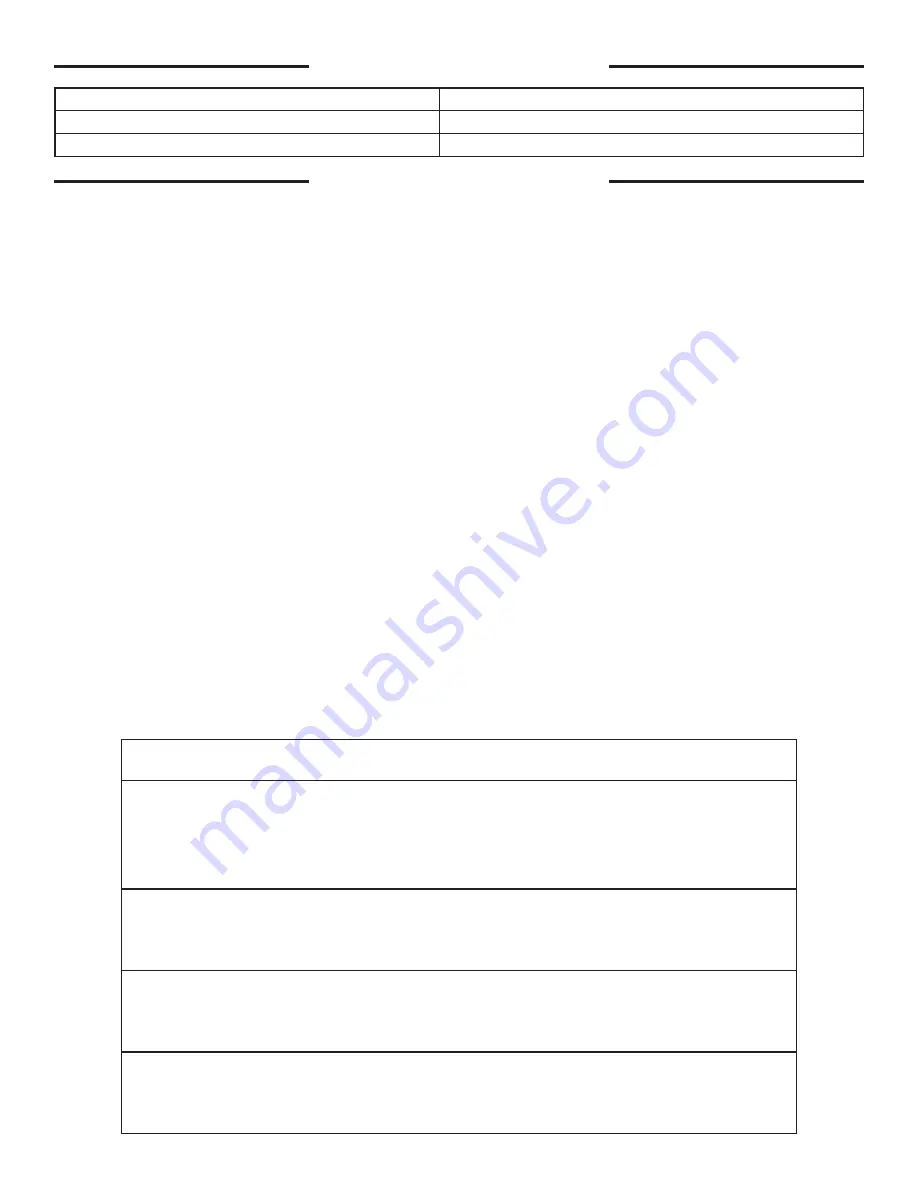
PAGE 2
Minimum / Maximum Operating Pressures
20 psi (138 kPa) - 125 psi (862 kPa)
Minimum / Maximum Operating Temperatures
40°F (4°C) - 110°F (38°C)
Current Draw & Voltage
0.5 Amperes - 110 Volts Other Options Available
The control valve, fittings and/or bypass are designed to accommodate minor plumbing misalignments but are not
designed to support the weight of a system or the plumbing.
DO NOT
use Vaseline, oils, other hydrocarbon lubrications or spray silicone anywhere. A silicone lubricant may be used
on black o-rings but is not necessary.
Avoid any type of lubricants, including silicone, on red or clear lip seals.
The nuts and caps are designed to be unscrewed or tightened by hand or with the optional maintenance wrench (p/n
V3193). If necessary, pliers can be used to unscrew the nut or cap.
DO NOT
use a pipe wrench to tighten or loosen nuts
or caps.
DO NOT
place screwdriver in slots on caps and/or tap with a hammer.
DO NOT
use pipe dope or any other sealant on threads. Teflon tape must be used on the threads of the 1” NPT elbow
or the 1/4” NPT connection and on the threads for the drain line connection. Teflon tape is not necessary on the nut
connection or caps because of o-ring seals.
After completing any valve maintenance involving the drive assembly and pistons, unplug power source jack from the
printed circuit (PC) board (black wire) and plug back in. This resets the electronics and establishes the service position.
All plumbing should be done in accordance with local plumbing codes. The pipe size of the drain line should be a
minimum of 1/2”. Backwash flow rates in excess of 7 gpm or length in excess of 20’ require 3/4” drain line.
Solder joints near the drain must be done prior to connecting the drain line flow control fitting. Leave at least 6” between
the drain line control and fitting solder joints when soldering pipes that are connected on the drain line control fitting.
Failure to do this could cause interior damage to the drain line flow control fitting.
When assembling the installation fitting package p/n V3007 (inlet and outlet - see page 9), connect the fitting to the
plumbing system first and then attach the nut, split ring and o-ring. Heat from soldering or solvent cements may damage
the nut, split ring or o-ring. Solder joints should be cool and solvent cements should be set before installing the nut, split
ring and o-ring.
Avoid getting primer and solvent cement on any part of the o-rings, split rings, bypass valve or
control valve.
Plug into an electrical outlet.
NOTE:
All electrical connections must be connected according to local codes. (Be certain the
outlet is uninterrupted.) Install grounding strap on metal pipes.
COMPONENTS:
MODEL
MINERAL TANK
(dia. & ht.)
MIERAL-
(QUANTITY OF BAGS)
7-LETDAN-1
FG1047DVT, 10 X 47 (with dome plug)
A8021 CALCITE - (2)
7-LETDAN-1.5
FG1054DVT, 10 X 54 (with dome plug)
A8021 CALCITE - (3)
7-LETDAN-2
FG1348DVT, 13 X 48 (with dome plug)
A8021 CALCITE - (4)
7-LETDAN-3
FG1365DVT, 13 X 65 (with dome plug)
A8021 CALCITE - (6)
7-LETIM-1
FG1044VT,10 X 44
A8007 BIRM - (1)
7-LETIM-2
FG1348VT, 13 X 48
A8007 BIRM - (2)
7-LETIM-3
FG1465VT, 14 X 65
A8007 BIRM - (3)
7-LETCT-1
FG1044VT,10 X 44
A8009 CARBON - (1)
7-LETCT-2
FG1348VT, 13 X 48
A8009 CARBON - (2)
7-LETCT-3
FG1465VT, 14 X 65
A8009 CARBON - (3)
7-LETST-1
FG1044VT,10 X 44
A8014 FILTER AG - (1)
7-LETST-2
FG1348VT, 13 X 48
A8014 FILTER AG - (2)
7-LETST-3
FG1465VT, 14 X 65
A8014 FILTER AG - (3)
OPERATING PARAMETERS
GENERAL WARNINGS