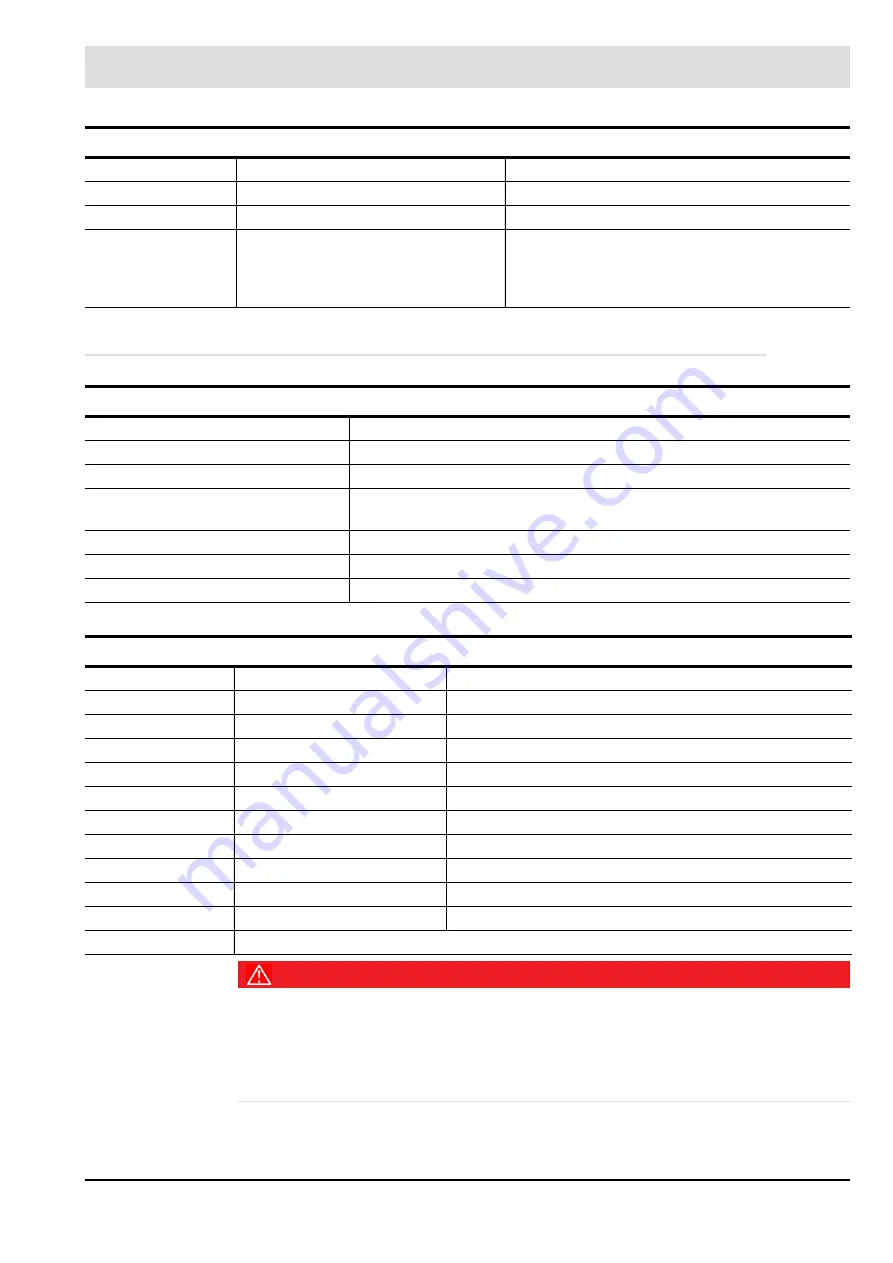
42
7
Technical Data
7.2
Actuators 662R550...
DANGER!
Danger by electrical shock!
If you don’t shut BurnerTronic down befor opening the cover, you may get in contact with con-
ducting parts. This may cause an electrical shock. You may open BurnerTronic only if you
have disconnected it all-pole.
Disconnect BurnerTronic all-pole.
Storage:
Climatic conditions
Class 1K3 according to DIN EN 60721-3
Mechanic conditions
Class 1M2 according to DIN EN 60721-3
Temperature range
-20 ... +70 °C (no condensation)
Electronic safety:
Degree of protection (DIN EN 60529):
BT300 – IP40 housing
IP20 terminals
UI300 – IP40 (clamping)
IP54 (glued assembly)
Environmental Conditions
Function
Floating time
5 s / 90° at 180 Hz
Direction of rotation 0° to 90°
right
Torque
0.8 Nm (both directions)
Holding torque
0.4 Nm (no power)
0.7 Nm
Permissible radial load
30 Nm (centre of output shaft)
Permissible axial load
5 N
Axial play of drive shaft
0.1 ... 0.2 mm
Environmental conditions
Operation
Climatic condition
Class 3K3 according to DIN EN 60721-3
Mechanical condition
Class 3M3 according to DIN EN 60721-3
Temperature range
-20 ... +60 °C (condensation is prohibited)
Transport
Climatic condition
Class 2K3 according to DIN EN 60721-3
Mechanical condition
Class 2M2 according to DIN EN 60721-3
Temperature range
-20 ... +70 °C (condensation is prohibited)
Storage
Climatic condition
Class 1K3 according to DIN EN 60721-3
Mechanical condition
Class 1M2 according to DIN EN 60721-3
Temperature range
-20 ... +70 °C (condensation is prohibited)
Bursting strength
Peak voltage
4 kV
Repeat frequency
2,5 kHz
Electrical safety
Protection class 2 as per DIN EN 60730
Summary of Contents for BurnerTronic BT320
Page 2: ......
Page 40: ...39 6 Leakage Test for Main Gas Valves Fig 6 1 Leakage test process diagram...
Page 46: ...45 7 Technical Data...
Page 47: ......