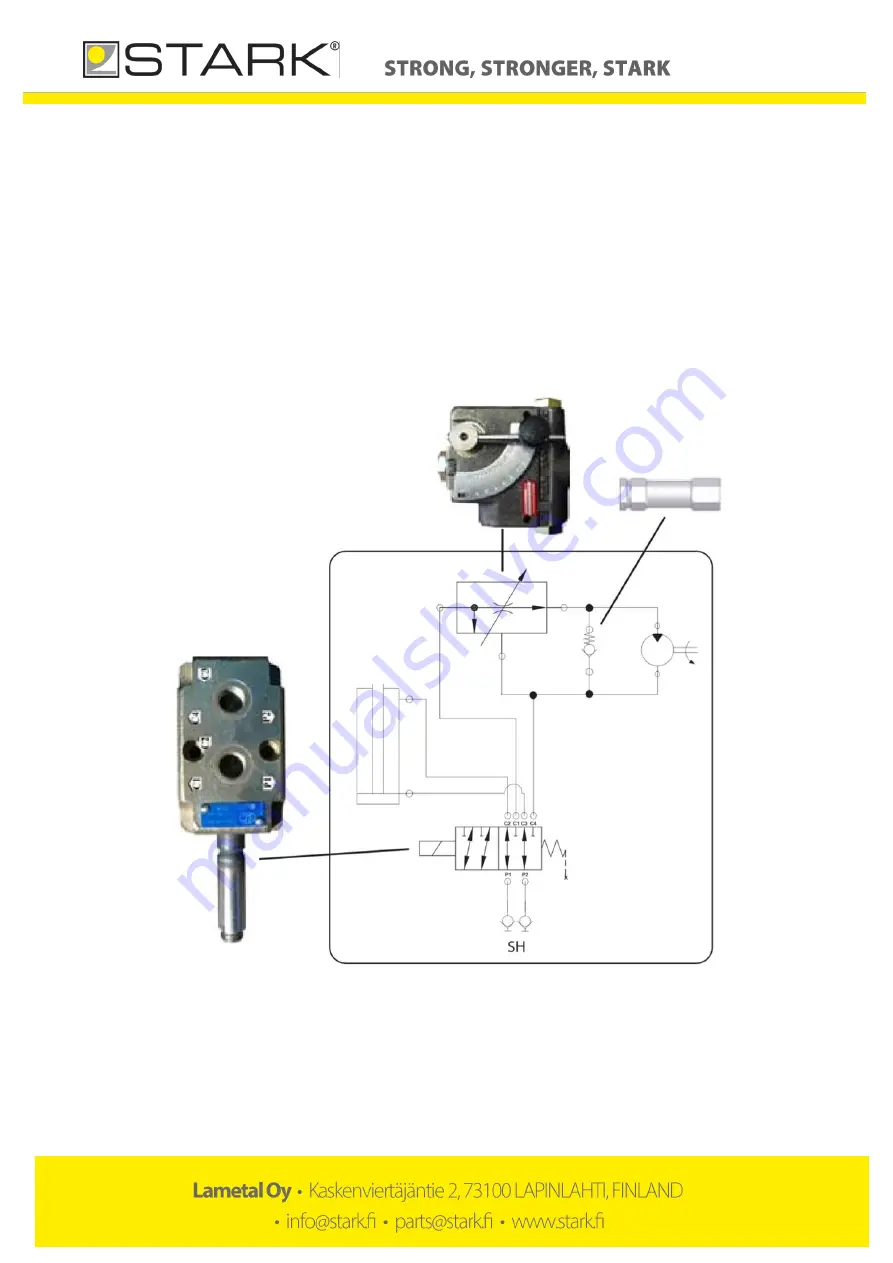
Sivu 18 / 20
9.
HYDRAULICS
The back broom can be connected in two different ways, either with two (figure 1) or four (figure 2) hoses. When
connecting with two hoses, the hydraulics of the basic machine is connected to quick connectors and a separate switch
is used to choose whether the broom is rotated or turned. When connecting with four hoses, a rotation cylinder and the
rolling of the engine are connected separately to the hydraulics of the basic machine. This means that the lifting and
rotating of the broom can be done with the hydraulics of the basic machine, and no separate control valve is needed.
The rotation speed of the broom is adjusted with the valve shown on figure 1. The suitable position is usually found
between 5 and 8. If there is a flow controller in the basic machine, the speed control valve can be set to position 10.
SH = Cylinder hydraulics
MH = Motor hydraulics
Figure 1. 2-hose hydraulics