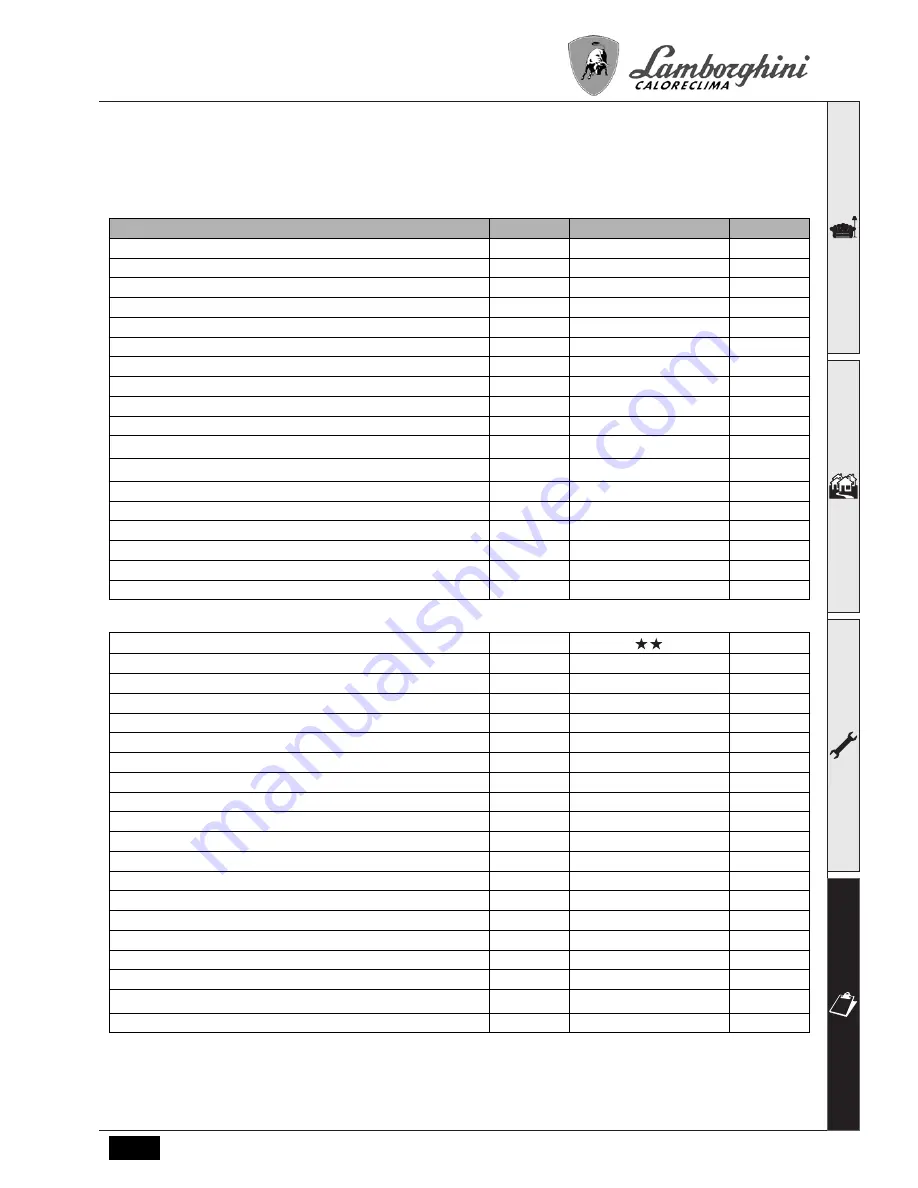
NINFA 32 MC
51
GB
cod. 3540G380 - 02/2007 (Rev. 00)
4.4 Technical data table
The column on the right gives the abbreviation used on the technical data plate.
Data
Unit
Setting
Max heating power
kW
34.4
(Q)
Min heating power
kW
11.5
(Q)
Max heating system heating power
kW
31.3
(P)
Min heating system heating power
kW
9.7
(P)
Max hot water heating power
kW
31.3
Min hot water heating power
kW
9.7
Burner nozzles G20
no. x Ø
15 x 1.35
Gas feed pressure G20
mbar
20
Maximum pressure downstream from the gas valve (G20)
mbar
12.0
Minimum pressure downstream from the gas valve (G20)
mbar
1.5
Max gas delivery G20
m
3
/h
3.64
Min gas delivery G20
m
3
/h
1.22
Burner nozzles G31
no. x Ø
15 x 0.79
Gas feed pressure G31
mbar
37
Maximum pressure downstream from the gas valve (G31)
mbar
35.0
Minimum pressure downstream from the gas valve (G31)
mbar
5.0
Max gas delivery G31
kg/h
2.69
Min gas delivery G31
kg/h
0.90
Efficiency class directive 92/42 EEC
-
NOx emission class
-
3 (<150 mg/kWh)
(NOx)
Max working pressure in heating
bar
3
(PMS)
Min working pressure in heating
bar
0.8
Max heating temperature
°C
90
(tmax)
Heating water content
litres
1.2
Heating expansion tank capacity
litres
10
Heating expansion tank pre-filling pressure
bar
1
Max working pressure in hot water production
bar
9
(PMW)
Min working pressure in hot water production
bar
0.25
Hot water content
litres
0.3
Hot water flow rate
'
t 25°C
l/min
17.9
Hot water flow rate
'
t 30°C
l/min
14.9
(D)
Protection class
IP
X5D
Supply voltage
V/Hz
230V/50Hz
Electrical power input
W
90
Electrical power input in hot water production
W
90
Weight with no load
kg
31
Type of unit
B
11BS
PIN CE
0461BR0843