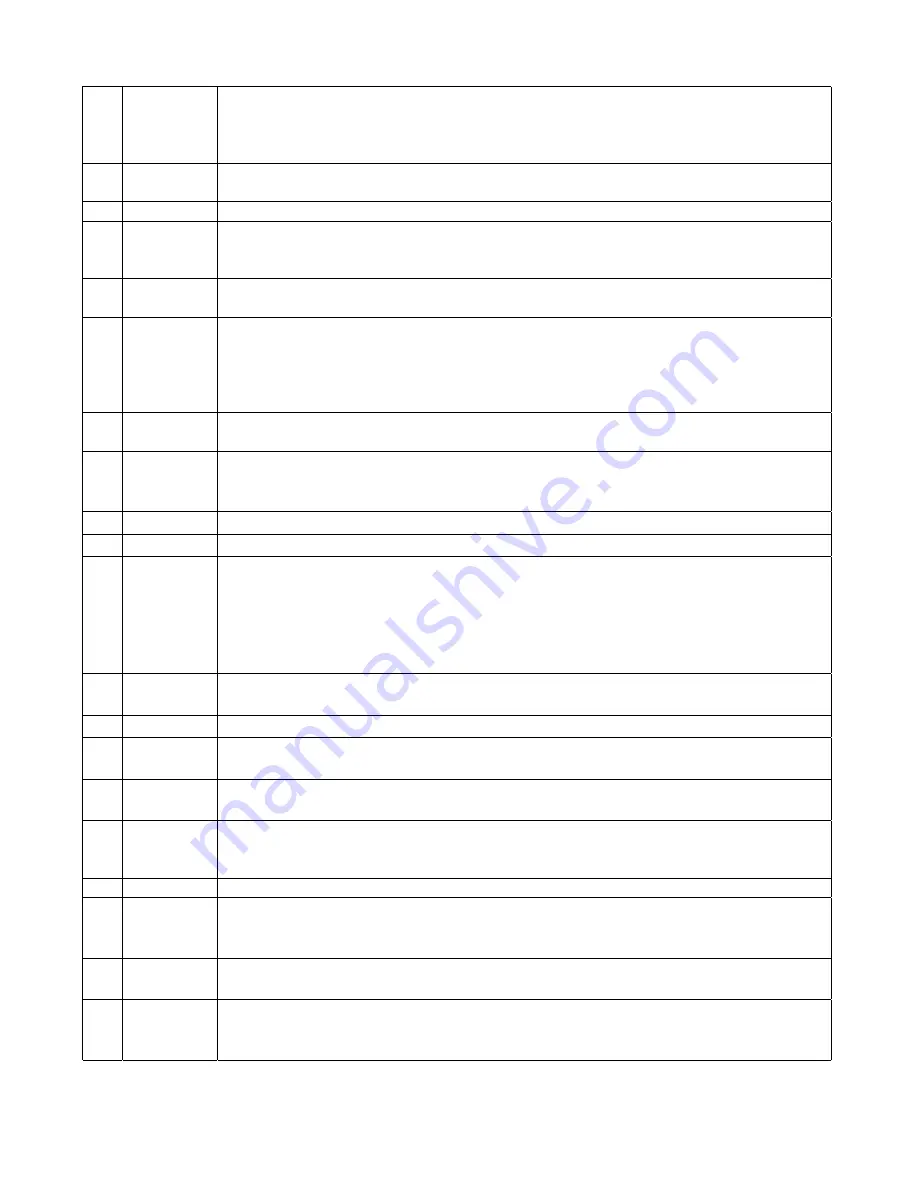
83-507-013 Rev. A
56
acters. A comma will separate the different fields. The fields, in order, are: Meas-
ured Voltage, Programmed Voltage, Measured Current, Programmed Current,
Over Voltage Set Point and Under Voltage Set Point.
Example: 5.9999,6.0000,010.02,010.00,7.500,0.000
8
FILTER
nn
Set the low pass filter frequency of the A to D Converter for Voltage and Current
Measurement where nn = 18, 23 or 46.
9
FILTER?
Returns the A to D Converter filter frequency: 18,23 or 46 Hz.
10 OUT
n
Turns the output to ON or OFF. Recover from Safe-Start, OVP or FLD fault.
OUT 1 (or OUT ON)-Turn On.
OUT 0 (or OUT OFF)-Turn Off
11 OUT?
Returns the output On/Off status string.
ON - output On. OFF - output Off.
12 FLD
n
Sets the Foldback protection to ON or OFF.
FLD 1 (or FOLD ON) - Arms the Foldback protection
FLD 0 (or FOLD OFF) - Cancels the Foldback protection.
When the Foldback protection has been activated, OUT 1 command will release
the protection and re-arm it, while FLD 0 will cancel the protection.
13 FLD?
Returns the Foldback protection status string:
“ON” - Foldback is armed. “OFF” - Foldback is cancelled.
14 FBD
nn
Add (nn x 0.1) seconds to the Fold Back Delay. This delay is in addition to the
standard delay. The range of nn is 0 to 255. The value is stored in eprom at AC
power down and recovered at AC power up.
15 FBD
?
Supply returns the value of the added Fold Back Delay.
16 FBDRST Reset the added Fold Back Delay to zero.
17 OVP
n
Sets the OVP level. The OVP setting range is given in Table 7-7. The number of
characters after OVP is up to 12. The minimum setting level is approximately
105% of the Output Voltage setting, or the value in Table 7-7, whichever is
higher. The maximum OVP setting level is shown in Table 5-1. Attempting to pro-
gram the OVP below this level will result in an execution error response (“E04”).
The OVP setting stays unchanged.
18 OVP?
Returns the setting “n” where “n” is the exact string in the user’s “OVP n”. When
in Local mode, returns the last setting from the front panel in a 4 digit string.
19 OVM
Sets OVP level to the maximum level. Refer to Table 7-7.
20 UVL
n
Sets Under Voltage Limit. Value of “n” may be equal to PV setting, but returns
“E06” if higher. Refer to Table 7-8 for UVL programming range.
21 UVL?
Returns the setting “n” where “n” is the exact string in the user’s “UVL n”. When in
Local mode, returns the last setting from the front panel in a 4 digit string.
22 AST
n
Sets the Auto-restart mode to ON or OFF.
AST 1 (or AST ON): Auto restart On.
AST 0 (or AST OFF): Auto restart Off.
23 AST?
Returns the string auto-restart mode status.
24 SAV
Saves present settings. The settings are the same as power-down last setting.
These settings are erased when the supply power is switched Off and the new
“last settings” are saved.
25 RCL
Recalls last settings. Settings are from the last power-down or from the last “SAV”
command.
26 MODE?
Returns the power supply operation mode. When the power supply is On (OUT 1)
it will return “CV” or “CC”. When the power supply is OFF (OUT 0 or fault shut-
down) it will return “OFF”.