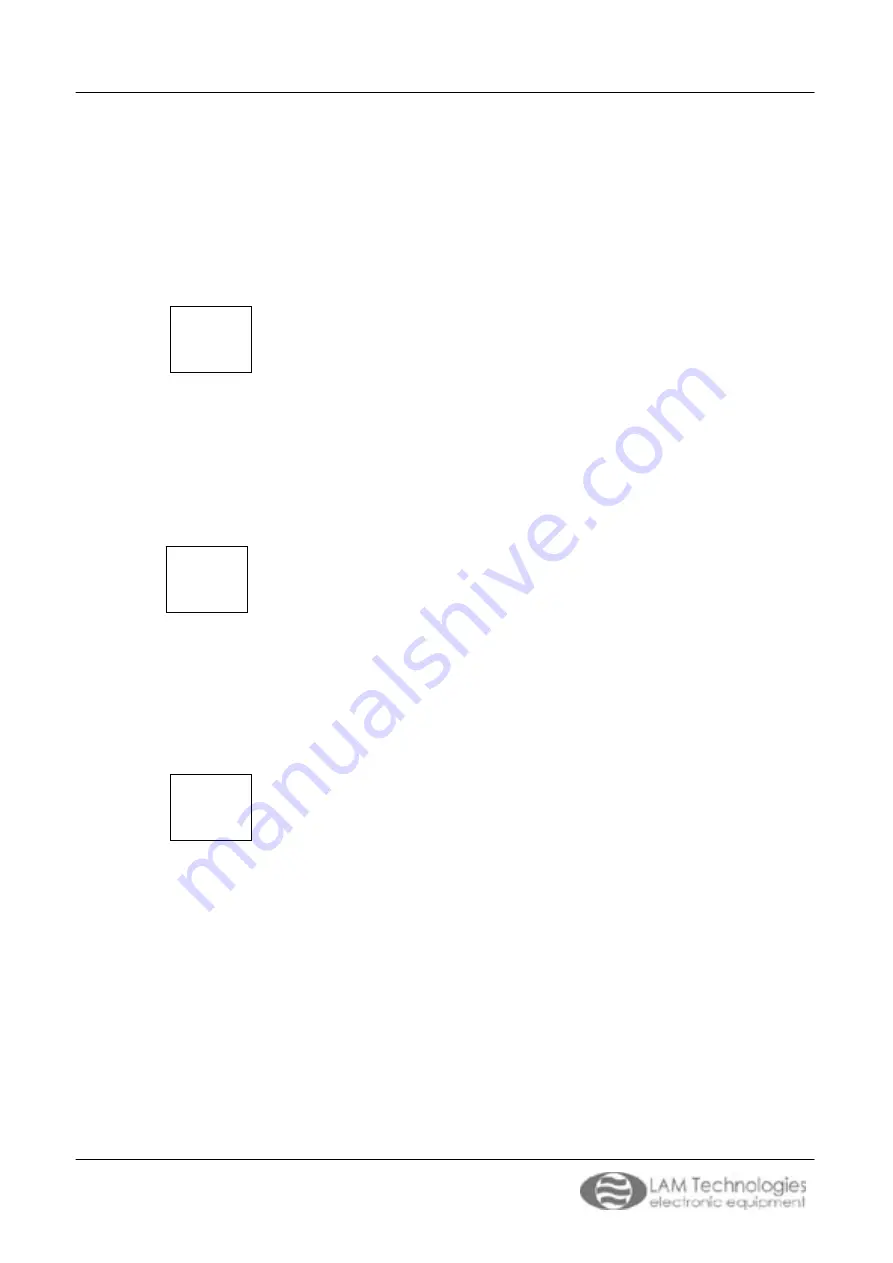
DS10xx
Functionality and Setting
37
If the motor works in a worm place or without a mechanic device capable
to discharge the heat, it is possible it reaches high temperatures even if
supplied by the nominal current. In this case it is possible to introduce a
forced ventilation on the motor or, if the torque margins allow it, to reduce
the current calibration on the driver. Remember that in this case the benefit
obtained in terms of temperature will go at the expense of the torque
supplied by the motor. Moreover, consider that when the driver calibration
current does not correspond to the motor nominal current, the
microstepping movement can lose regularity. In the same way, sometimes
it is possible to improve the microstepping movement by slightly
modifying the current calibration.
Typically a two phase stepping motor disposes of four wires, two per each
phase. In this case the driver current calibration must correspond to the
motor current plate. If for example the motor quotes 3A/phase also the
driver shall be to be calibrated to 3Arms.
Some motors, supplied with more windings, allow to choose between series
and parallel connections.
The series configuration requires a lower phase current but it also exposes a
superior inductance towards the driver which penalizes the motor torque at
high speeds. Therefore, this kind of connection is used in applications
where motor speed is limited or supply voltage sufficiently high.
When a series configuration is used it is necessary to calibrate the driver to
the motor phase current multiplied by the coefficient 0.71. If for example
we are using a motor with plate current 3A, with the windings connected in
series we should calibrate the driver to a current of 2.1Arms (3 * 0.71).
Furthermore take note that the inductance exposed by the motor to the
driver is 2 times the single phase one.
On the contrary, the parallel configuration requires an higher phase current
but it has the advantage to maintain the torque supplied by the motor more
constant to the increasing of the speed. It happens because the inductance
exposed by the parallel connection is inferior. This connection is preferable
when the supply voltage is low or the motor working speed is high.
When a parallel configuration is used it is necessary to calibrate the driver
to the motor phase current multiplied by the coefficient 1,41. If for example
we are using a motor with plate current 3A, with the windings connected in
parallel we should calibrate the driver to a current of 4.2Arms (3 * 1.41).
Furthermore take note that the inductance exposed by the motor to the
driver is in this case the same as the single phase one.
|
|
|
Summary of Contents for DS10 Series
Page 1: ...DS10xx Hardware rev 1 10 Firmware rev 1 13 Microstepping Stepper Motors Driver User s Manual ...
Page 4: ......
Page 10: ......
Page 14: ......
Page 62: ......