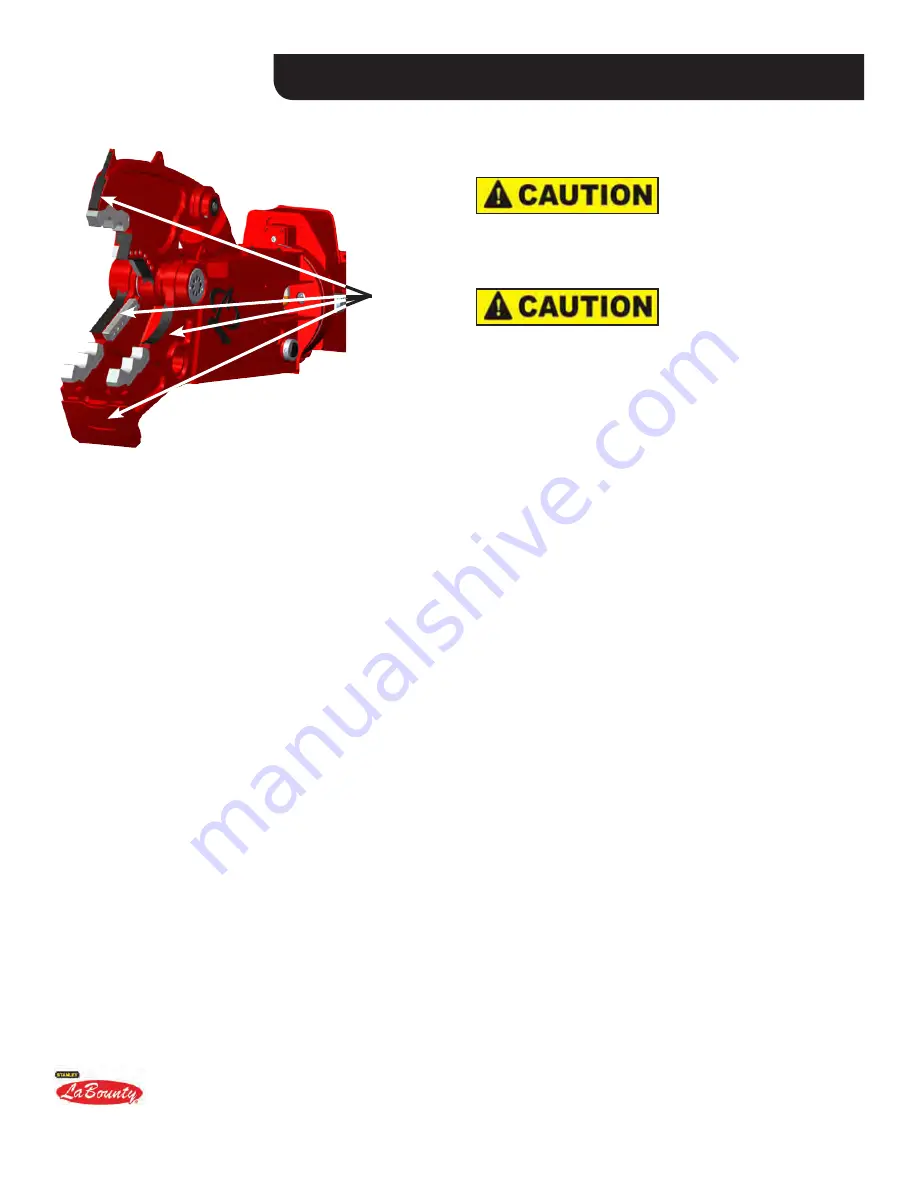
Maintenance
Section 5
Page 13
MOBILE DEMOLITION PROCESSORS
BUILD UP PROCEDURE
continued
WEAR PLATE REPLACEMENT
See Figure 5-5 for specific areas with wear plates installed; refer to Parts Catalog for specific wear plate part
numbers. Pay special attention to the preheat and post-heat instructions and follow them exactly.
1. Remove existing wear parts.
2. Clean the areas underneath old wear parts, removing any grease, paints, or other foreign materials that
may be harmful to the weld.
3. Preheat the area to 200-300˚F (100-150˚C) and maintain this temperature throughout the build up and hard-
surfacing procedure.
4. If necessary, build up along the top and front edges of the secondary blade seat flush with the blade. The
blade should not stick out beyond the edge of the seat in this area. However, do not weld in the apex area.
5. If the temperature within 6" (150 mm) of the weld area has dropped below 400°F (200°C) during the weld
process, post heat this area to 400°F (200°C).
6. Wrap with a heat blanket and allow the welded area to cool slowly to the ambient temperature. The MDP
should not be put back into service until it has cooled completely.
7. If you have any questions, contact LaBounty Service Department (800-522-5059) for specific welding in-
structions.
HARDSURFACING RECOMMENDATIONS
If hardsurfacing, Stanley LaBounty recommends Amalloy 814H rod or equivalent. It is important to always
use a hardsurfacing weld material with a chromium content of less than .10% ( or less than one-tenth of one
percent) and a severe impact-resistance rating to prevent cracking. If you have questions about what hardsur-
face material to use, please contact the Stanley LaBounty Customer Service Department. Failure to adhere to
LaBounty hardsurfacing recommendations may compromise the attachment warranty. Before hardsurfacing,
E7018 underlayment beads must be laid down. The hardsurfacing is then applied to the underlayment beads.
Hardsurfacing must not be applied directly to the parent material.
Amalloy Welding and Industrial Supply
Phone: 800-735-3040 (toll free)
Fax: 763-753-8263
Web site: amalloy.com
FIGURE 5-5
WEAR
PLATES
DO NOT use stainless hardsurface rod. It will
crack the base metal, which can cause a major
structural failure of MDP jaws.
Using improper build-up products may result
in premature wear or increased potential
for cracking and may compromise warranty
coverage.
Summary of Contents for 513914
Page 1: ...Mobile Demolition Processors Part Number 513914 Safety Operation Maintenance Manual...
Page 4: ......
Page 20: ...Page 8 Section 2 About the Attachment MOBILE DEMOLITION PROCESSORS...
Page 30: ......
Page 74: ......
Page 77: ...Pivot Adjustment and Jaw Changeout Guide Section 6 Page 3 MOBILE DEMOLITION PROCESSORS...
Page 97: ......